Pumpengehäuse dienen dem flüssigkeitsdichten und druckfesten Abschluss des Pumpeninnenraumes nach außen. Bei Kreiselpumpen umschließen sie den Pumpenläufer, der dem Fördermedium durch Laufräder auf der rotierenden Welle Energie zuführt.
Bei den Verdrängerpumpen hingegen umschließen sie die rotierenden oder oszillierenden Verdränger (z. B. ein oder mehrere Kolben).
Der Zu- und Abführung des Förderstroms dienen die Eintritts- und Austrittsstutzen, die (ihrer Funktion nach) oft auch als Zulauf- oder Saug- sowie Druckstutzen bezeichnet werden. Sie werden mit Rohrverbindungen (z. B. Flanschen, Verschraubungen) an Rohrleitungen angeschlossen, sofern sie nicht:
- wie bei vertikalen Rohrgehäusepumpen saugseitig in den offenen Flüssigkeitsspiegel eintauchen;
siehe Abb. 1 Pumpengehäuse - wie bei Tauchmotorpumpen mit dem gesamten Pumpengehäuse eingetaucht sind.
siehe Abb. 2 Pumpengehäuse
Erfordert die Bauart der Pumpe, dass die Antriebswelle durch das Pumpengehäuse geführt wird, so verhindern Wellendichtungen das Austreten von größeren Flüssigkeitsströmen aus dem oder das Eindringen von Luft in das Pumpengehäuse. Diese Teile des Pumpengehäuses werden Dichtungs- oder Stopfbuchsgehäuse genannt.
Fast jede Pumpenbauart hat ihre eigene Gehäuseform, an der sie äußerlich erkennbar ist. Mit wachsenden spezifischen Drehzahlen werden als Gehäuseformen verwendet:
- Spiralgehäuse, bei dem zum Ausgleich des Radialschubs gelegentlich auch eine Doppelspirale mit zwei um 180° versetzt beginnenden Spiralen ausgeführt ist.
siehe Abb. 3 Pumpengehäuse und Abb. 6 Spiralgehäuse - Drallspirale, mit einem im Meridianschnitt stark unsymmetrischen Spiralquerschnitt.
siehe Abb. 4 Pumpengehäuse - Ringraumgehäuse, mit über dem Umfang gleichbleibendem Querschnitt.
siehe Abb. 13 und 15 Pumpengehäuse - Rohrgehäuse, das den aus dem Leitrad kommenden Förderstrom der Pumpe in axialer Richtung weiterführt. siehe Abb. 1 Pumpengehäuse
- Krümmergehäusepumpe, deren Leitrad jedoch in einen Rohrkrümmer (Krümmergehäuse) mündet.
siehe Abb. 2 Propellerpumpe
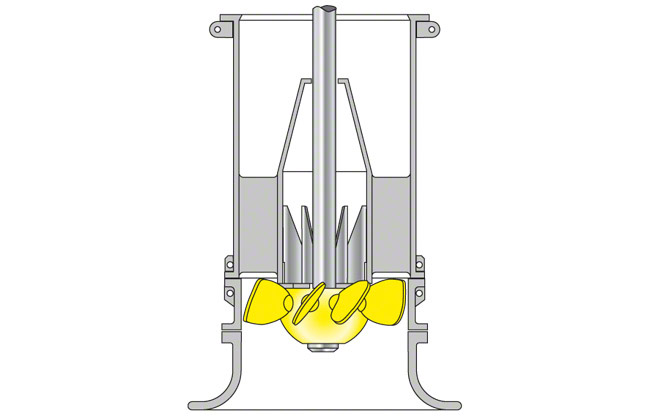
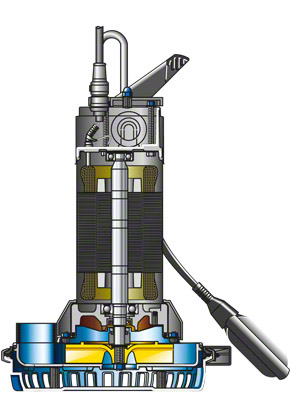
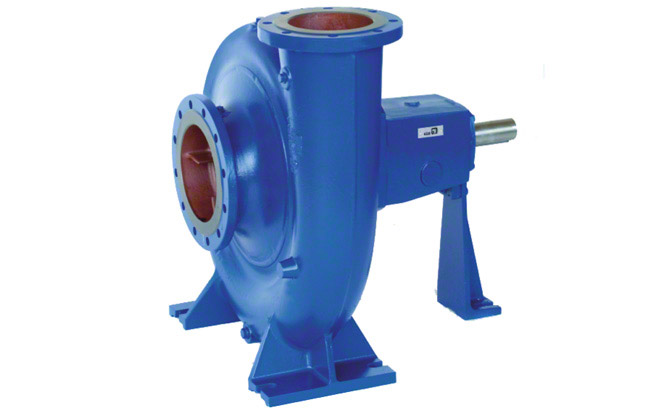
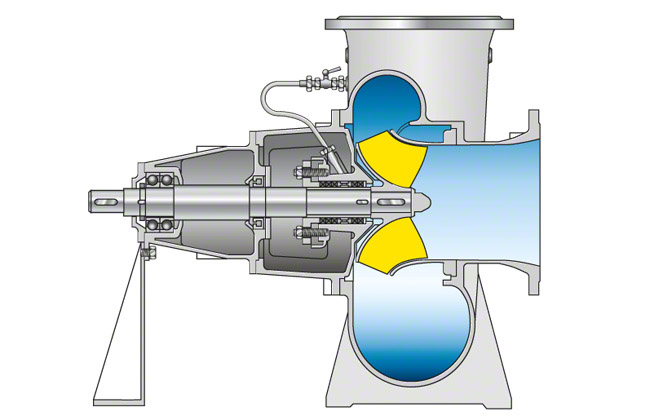
Auch der Druckbereich prägt die Pumpengehäuseformen. So erfordern die Niederdruckpumpen andere konstruktive Lösungen als Hoch- und Höchstdruckpumpen. Denn mit einem zunehmenden Druckniveau müssen die Wandstärken des Druckgehäuses erhöht werden. Dabei muss die Dimensionierung des Pumpengehäuses sowohl nationalen als auch internationalen Regelwerken entsprechen. Bei Spiralgehäuse- und mehrstufigen Hochdruckpumpen werden die äußeren geometrischen Formen zugunsten von zylindrischer (siehe Topfgehäusepumpe), kegeliger oder kugeliger (siehe Umwälzpumpe) Pumpengehäuse angepasst. siehe Abb. 5, 6 Pumpengehäuse

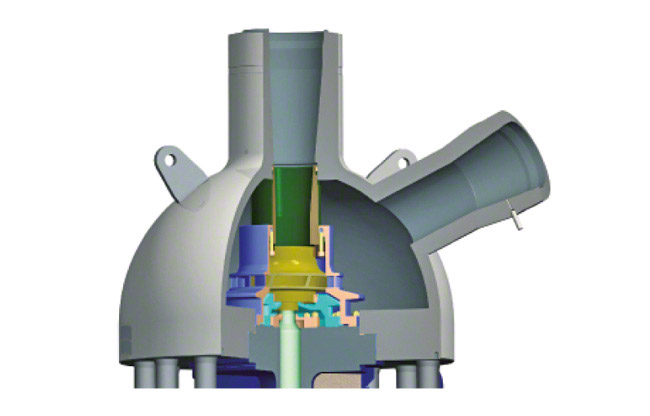
Diese Konfigurationen ermöglichen trotz des hohen Innendrucks eine niedrige Spannungsbelastung des Pumpengehäuses und geeignete Herstellmethoden für dickwandige (geschmiedete) Bauteile.
Nicht mit der Topf- oder Mantelgehäusepumpe zu verwechseln ist die vertikale Topfpumpe, die aus Gründen des Saugverhaltens häufig als Kondensat- oder Raffineriepumpe eingesetzt wird. Ihr Topf umschließt die Pumpensaugseite.
Daneben bietet die aus Montagegründen geforderte Gehäuseteilung in Form der Querteilung (quer zur Welle) oder Längsteilung (in Wellenebene geteilt) weitere konstruktive Unterscheidungsmerkmale.
siehe Abb. 7, 8 Pumpengehäuse
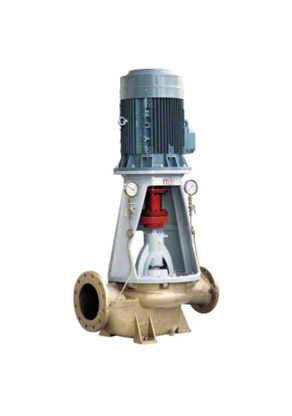
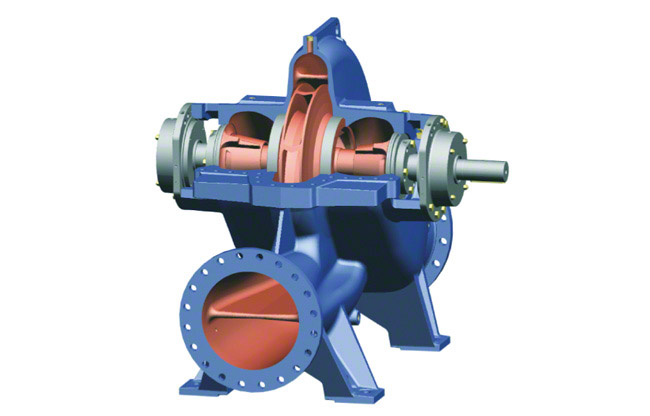
Ein weiteres für die Form des Pumpengehäuses entscheidendes Kriterium ist die Lage der Pumpenstutzen. So ist bspw. der axiale Eintrittsstutzen bei einstufigen Spiralgehäusepumpen ein besonderes Merkmal dieser Pumpenbauart im Gegensatz zur Inlinepumpe mit einander gegenüberliegenden Stutzen oder zur Raffineriepumpe mit der Stutzenstellung "top-top"(beide Stutzen oben). siehe Abb. 9, 10 Pumpengehäuse
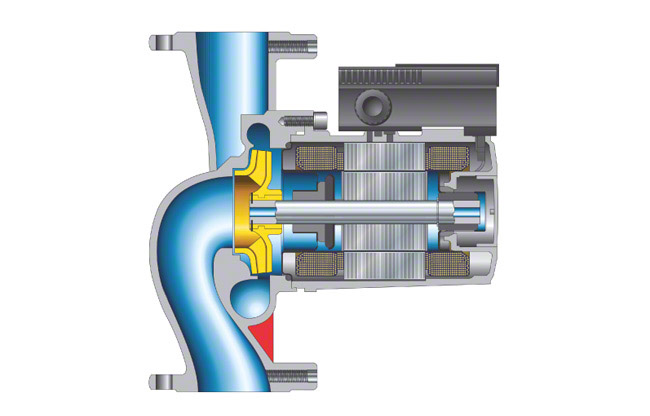
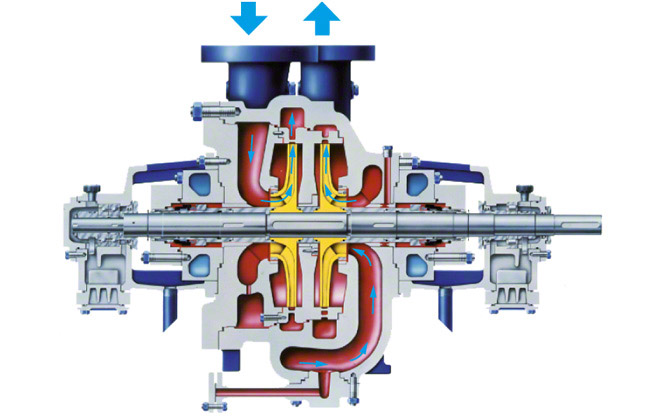
Selbst die Aufnahme der Lagerung von fliegend gelagerten Pumpenwellen in einem Lagerträger oder die Verwendung eines Lagerbocks wie bei der Spiralgehäusepumpe dient als konstruktives Klassifizierungsmerkmal eines Pumpengehäuses.
Bei Gliederpumpen mit Querteilung des Pumpengehäuses werden die Gehäuseteile nach ihrer Funktion benannt: Saug-, Stufen- (mögliche mehrfache Anordnung hintereinander) und Druckgehäuse. Im zusammengebauten Zustand werden diese durch Zuganker druckfest miteinander verbunden.
Die Abdichtung der einzelnen Gehäuseteile gegen den Innendruck geschieht meist durch Flachdichtungen, O-Ringe oder direkte metallische Abdichtungen wie beim Aufeinanderpressen der planparallelen Stufengehäusepassflächen bei den Höchstdruckpumpen. Liegt die Gehäuseteilfuge in der Wellenebene wie bei der Längsteilung, so besteht das Pumpengehäuse bei Kreiselpumpen mit horizontaler Welle aus einem Gehäuseunterteil, das die beiden Stutzen für die Rohranschlüsse und die Pumpenfüße enthält sowie einem einfach gebauten Pumpenoberteil. siehe Abb. 11 Pumpengehäuse
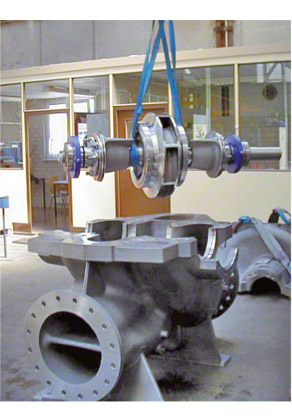
In der Teilfuge enthalten beide Pumpenteile einen Flansch der sich um das gesamte Pumpengehäuse einschließlich der beiden Stopfbuchsgehäuse erstreckt und mit zahlreichen Schrauben das Gehäuse druckfest sowie flüssigkeitsdicht verschließt. Bei ein- und mehrstufigen Pumpen mit vertikaler Welle wird der Pumpenläufer häufig in einem vom Fördermedium geschmierten Lager geführt, sodass die zweite Wellendichtung nicht erforderlich ist. siehe Abb. 14 Pumpengehäuse
Mehrstufige Pumpen mit vom Fördermedium geschmierten Lagern können äußerst kompakt gebaut werden und haben zudem eine ausgezeichnete Laufruhe, die durch einen (aufgrund des kurzen Lagerabstandes) sehr steifen Pumpenläufer bedingt ist. Darüber hinaus ergibt die Wahl von ausschließlich vom Fördermedium geschmierten Lagern eine materialsparende Gesamtkonfiguration der Pumpe und macht nur eine Niederdruckgleitringdichtung notwendig. siehe Abb. 14 Pumpengehäuse
Außer den genannten Gehäuseteilen gehören zu den Pumpengehäusen noch die Wärmesperre und das Kühlgehäuse, das oft durch einen besonderen Kühldeckel verschlossen wird. Sie haben beide die Aufgabe, bei Pumpen mit heißem Fördermedium den Wärmestrom vom Pumpeninnenraum zum Pumpenlager und (soweit vorhanden) zur Wellendichtung bzw. zum Nassläufermotor zu mindern. Umgekehrt hat ein Pumpenheizmantel die Aufgabe, den Inhalt des Pumpengehäuses bei stehender Pumpe durch ständige Wärmezufuhr auf Betriebstemperatur zu halten, um unerwünschte Ablagerungen sowie Kristallbildungen oder gar ein Erstarren des Fördermediums zu verhindern. siehe Abb. 12 Pumpengehäuse
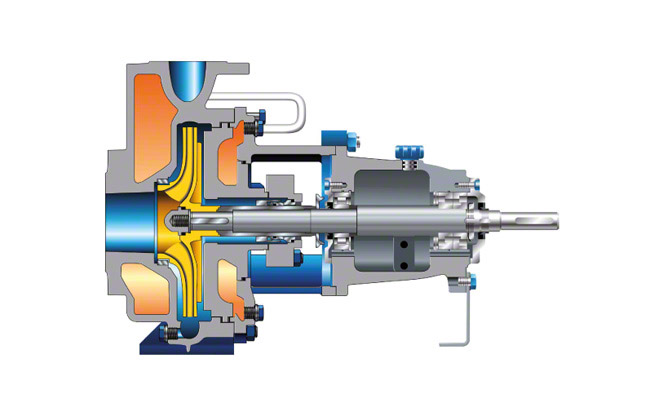
Die Pumpengehäuse werden überwiegend gegossen, können aber auch geschmiedet, geschweißt, gepresst oder gezogen werden. siehe Abb. 3, 4 und 5 Kesselspeisepumpe
Die Maschinensicherheit hängt wesentlich von der Haltbarkeit des Pumpengehäuses ab, sodass viele branchenspezifische Regelwerke die Gehäusewerkstoffe und z. T. auch die Bemessung der Wandstärken vorschreiben. Häufig dabei verwendete metallische Gusswerkstoffe sind Gusseisen, Sphäro- und Stahlguss, ferritische oder austenitische Chromstähle, austenitisches Gusseisen, aber auch Duplexstähle für hochkorrosionsfeste Anwendungen wie z. B. in der Meerwasserentsalzung (siehe Werkstoffe).
siehe Abb. 13 Pumpengehäuse
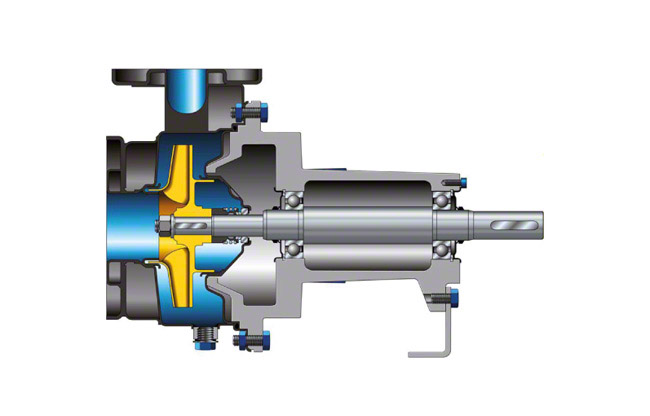
Bei vertikalen einstufigen Pumpen für große Förderströme werden häufig Pumpengehäuse aus Beton gefertigt. Dieses gilt insbesondere für Rohrgehäusepumpen, siehe Abb. 2 Schöpfwerkspumpe, aber auch für sehr große Spiralgehäusepumpen. siehe Abb. 6 Kühlwasserpumpen
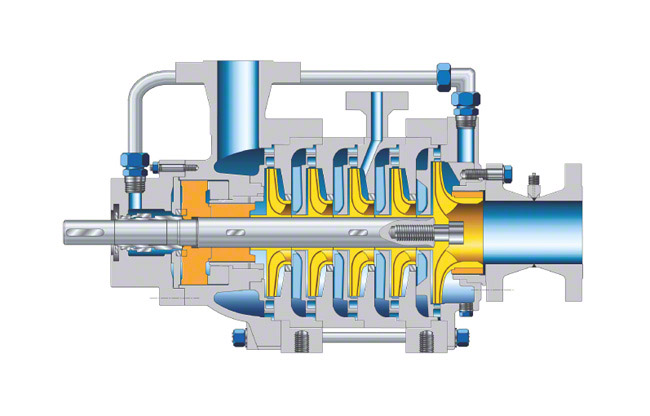
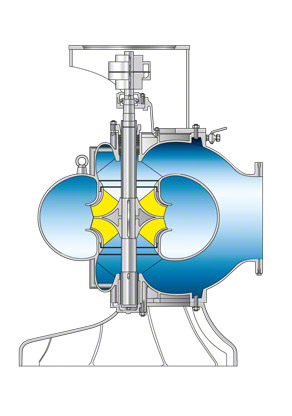