Closed-loop control (general)
Closed-loop control is a procedure during which a quantity to be controlled (controlled quantity) is continually measured, compared to another quantity (reference quantity), and adjusted accordingly in a closed loop.
Closed-loop control is therefore a process whereby the output variable also influences the control variable via feedback. The actual value of the output is fed back to the controller, and disruptive influences are taken into account and corrected at this time so that the setpoint can be reached despite imprecise models. Open-loop control systems do not have a feedback loop. See Fig. 1 Closed-loop control
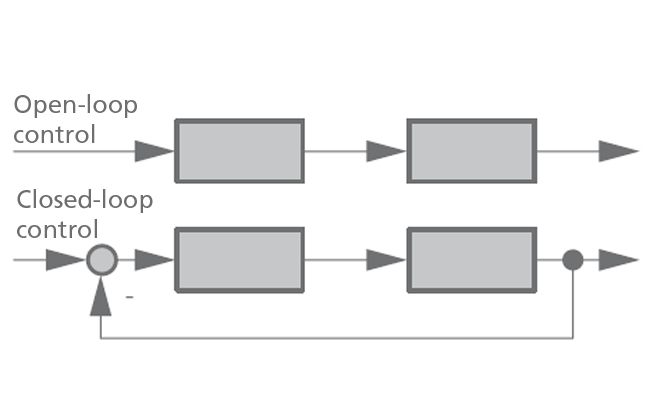
Closed-loop control for centrifugal pumps and pump systems
In conjunction with operating pumps, flow rate closed-loop control refers to methods and the accompanying equipment for varying this rate and adjusting it in accordance with a desired value (setpoint).
The centrifugal pump and pump system are two systems that are connected in series. The performance of a centrifugal pump can be shown graphically on its H/Q curve (characteristic curve) by plotting the head (H) over the flow rate (Q) for a specific type of pump.
Flow through the system causes a head loss, that varies as a square of the flow rate and is defined by the system characteristic curve (with Hsys as the system head). If head H is the same as the head Hsys, this will result in the flow rate at operating point (B).
See Fig. 2 Closed-loop control
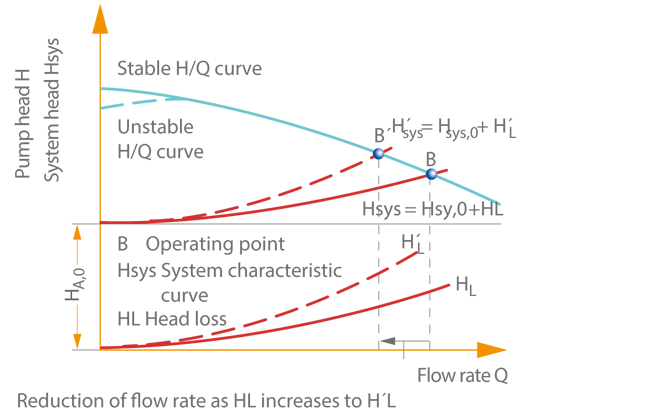
If the system characteristic curve becomes steeper as a result of throttling (H‘sys > Hsys), the flow is decelerated in the Valve, and the flow velocity and flow rate decrease. This occurs until a new balanced state (H‘sys = Hsys) is established, i.e. with a lower flow rate at operating point B‘ following the throttling action. This balancing behaviour is used to systematically control the flow rate.
Methods for systematically controlling the flow rate:
Changing the system characteristic curve
The system curve (system characteristic curve) is changed e.g. by means of a gate valve and other valves fitted in the piping which influence head losses. See Fig. 3 Closed-loop control
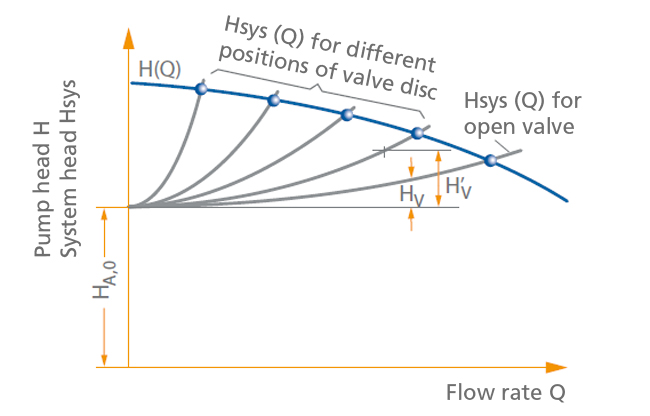
An increase in flow losses (H‘L > HL) and the resulting change in the system characteristic curve lead to an intersecting point with the H/Q curve at a lower flow rate. See Fig. 2 Closed-loop control
Control by throttling (i.e. by generating losses) is associated with high operating costs, since the system (piping) only requires part of the head generated by the pump (at low flow rates) while the other part is converted into non-usable energy.
This control method is used primarily for relatively small centrifugal pumps, such as radial pumps, whose hydraulic performance is more permitting of such operation across their entire characteristic curves (see Operating behaviour and which are not operated at flow rates that greatly
deviate from the optimum flow rate over extended periods. In addition, the power input must decrease with flow rate as for some mixed-flow pumps (see Characteristic curve).
Throttling should always be performed on the discharge side of the pump only, to avoid cavitation in the centrifugal pump (see NPSH).
Throttling is an economically favourable type of closed-loop control in terms of investment outlay. Its overall economic efficiency should be checked, however, whenever higher power ratings and longer operating periods are concerned. This type of operation is required if the shut-off head of a centrifugal pump must be maintained to allow open-loop control (starting/stopping) using pressure-dependent control units. For longterm throttling applications a fixed orifice is frequently fitted in the piping in place of a throttling element or to assist it (see Valve).
Changing the H/Q curve of the centrifugal pump
The H/Q curve of the centrifugal pump can be changed by implementing such measures as:
- Controlling the rotational speed
- Changing the approach flow to the impeller by means of pre-swirl control measures, as for cooling water pumps
- Changing the geometry of the centrifugal pump impeller by adjusting the impeller blade pitch (e.g. propeller pump)
- Trimming the impellers to match a specific duty point (change can only be made once and is irreversible)
- Self-regulation of the centrifugal pump resulting from cavitation See Fig. 6 Condensate pump
- Adjusting the diffuser vanes in the diffuser (used less frequently)
- Partially covering the outlet of radial impellers via regulating rings under low-flow conditions (used less frequently)
Only the pump head required by the system characteristic curve at the target point of the flow rate should be generated by the pump. In terms of operating costs, this type of closed-loop control is an economically efficient way of operating centrifugal pumps.
The H/Q curve (constant speed curve) of a centrifugal pump changes with rotational speed (n) as per the relationships expressed in the affinity laws (Q ~ n, H ~ n2). When rotational speed is changed, all points on the H/Q curve move on parabolas, e.g. operating point B1 moves on the parabola to B2. See Fig. 4 Closed-loop control
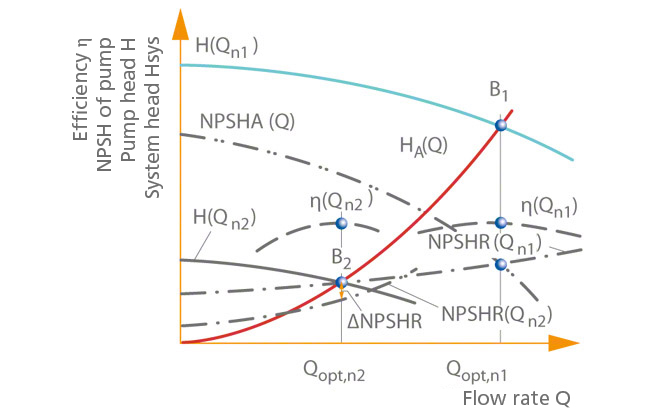
For system characteristic curves that pass through zero (Hsys = 0, Qsys = 0), the best efficiency point can move along the system curve in such a manner that the pump always operates at the optimum flow rate (Qopt).
The higher Hsys,0 is, the greater the risk of the pump operating at a poorer level of efficiency at low-flow conditions when flow rate is decreased, or at overload conditions when flow rate is increased. See Fig. 5 Closed-loop control
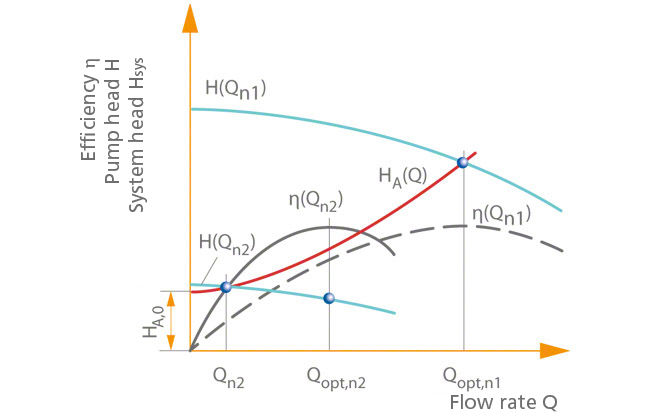
With speed control, only the head that is required is generated, which makes this control method the most energy-efficient and pump-friendly form of closed-loop control.
Rotational speed is most often adjusted by means of a drive such as a steam or gas turbine, a combustion engine (e.g. diesel engine), or an electric motor (field-regulated direct current motor or asynchronous motor with frequency inverter), and less often by a gear unit (e.g. controllable hydraulic torque converter or fluid coupling).
On the inlet side of the centrifugal pump, a safety buffer is always provided for the NPSH available in the system when speed is reduced. See Fig. 4 Closed-loop control
The inflow (see Inlet conditions) to a centrifugal pump impeller is typically free of swirl (see Vortex flow), i.e. for pre-swirl control equipment with controller position α = 90° (see Velocity triangle which represents swirl-free inflow for cooling water pumps. See Fig. 10 Cooling water pump
Co-swirling (in the direction of the impeller rotation) leads to a drop in the H/Q curve and power input of every centrifugal pump. While this barely impacts standard radial impellers, the effects of the change in inflow become more pronounced for mixed-flow and axial pumps as specific speed increases. As a result, pre-swirl control is particularly effective for mixed-flow pumps with high specific speeds when it comes to changing the H/Q curve to save power. Pre-swirl control equipment with inlet guide vanes can be infinitely adjusted. See Fig. 1 and Fig. 10 Cooling water pump
For propeller pumps, infinite adjustment is successfully achieved by means of impeller blade pitch control. See Fig. 6 Closed-loop control
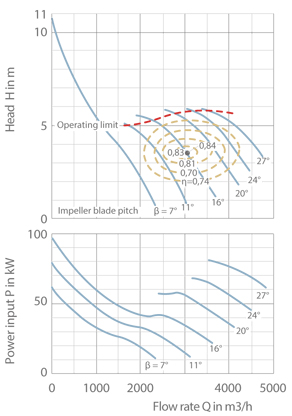
A much simpler but far less efficient approach is the less frequently used practice of adjusting the diffuser vanes on a radial centrifugal pump. See Fig. 7 Closed-loop control

By axially displacing the impeller or covering a part of its outlet section via a regulating ring, it is possible to partially restrict the impeller throughflow for control purposes. See Fig. 8 Closed-loop control
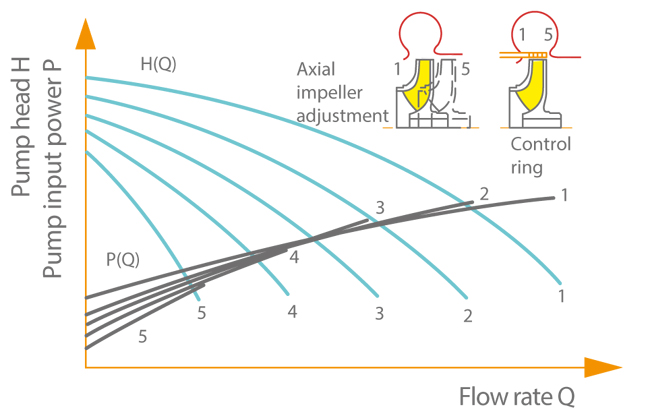
Trimming impellers or reducing the impeller vane diameter can only be regarded as control methods in the broadest sense of the word. While usually used to initially adapt a centrifugal pump to the pump system, these methods cannot be implemented during operation, nor reversed, unlike with genuine control measures. See Fig. 9 Closed-loop control
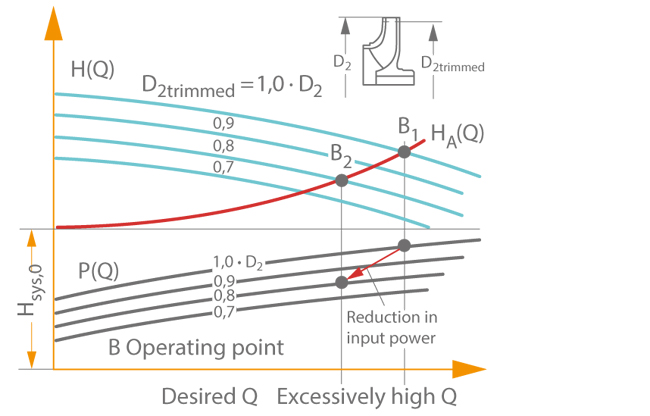
Bypass control
The type of closed-loop control whereby fluid travels through a centrifugal pump and system (piping) at different flow rates is known as bypass control (see Bypass) Such control is only beneficial for pumps whose characteristic power input curve drops as the flow rate increases. This is the case for propeller and peripheral pumps, for example. See Fig. 10 Closed-loop control
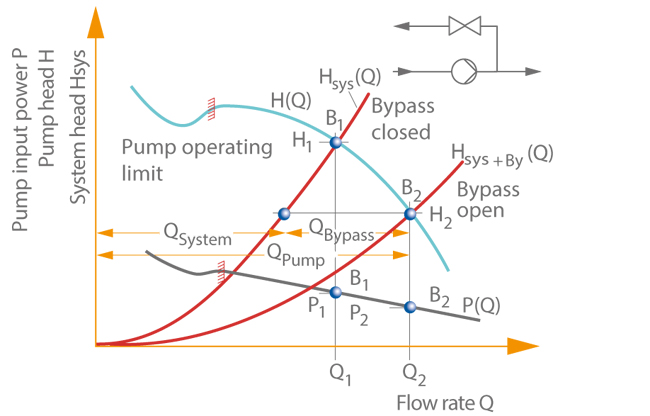
Advantages and drawbacks of closed-loop control types
Power input is very dependent on the characteristic curves of the centrifugal pump and system such that specific examples cannot be generalised.
A qualitative comparison can provide an overview of closed-loop control types with respect to power input. In one example, the flow rate (Q) is reduced by fifty percent. See Fig. 11 Closed-loop control
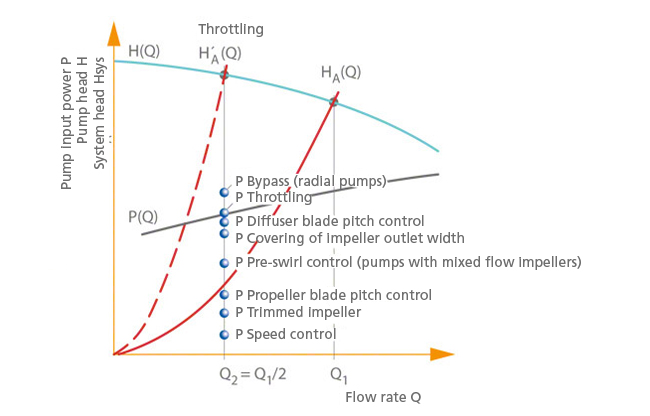
Bypass control requires the greatest power input for radial pumps, unlike with propeller pumps.
Graduating down to smaller power inputs, the most important types of closed-loop control are throttling, pre-swirl control, impeller blade pitch control (propeller blade pitch control), and speed control.
In summary, the diagrams reveal that the greatest amount of energy can be saved using slip-free speed control.
A disadvantage of energy-saving closed-loop control methods is the investment outlay, which is higher than that required for throttling. Efficiency calculations must be performed to decide which closed-loop control method should be used for the application in question.
*HV ≙ HL