Pump test facility
When developing pumps and testing the finished products (e.g. for the purpose of carrying out an acceptance test as an evidence of compliance with the guaranteed values) it is essential to experiment on a pump test facility in advance and to carry out tests (final testing).
The set-up of the test beds required for this purpose varies depending on the task. They range from straightforward functional test beds right through to complex test facilities which have to meet the highest requirements on precision. A distinction is made in this context between "open" and "closed" test beds.
In the case of an open test bed, the pump is mounted next to a basin with an open water surface (see Atmospheric pressure). The pump takes the fluid handled from here and discharges it back into the basin via several measurement and control devices (see Metrology). See Fig. 1 Pump test facility
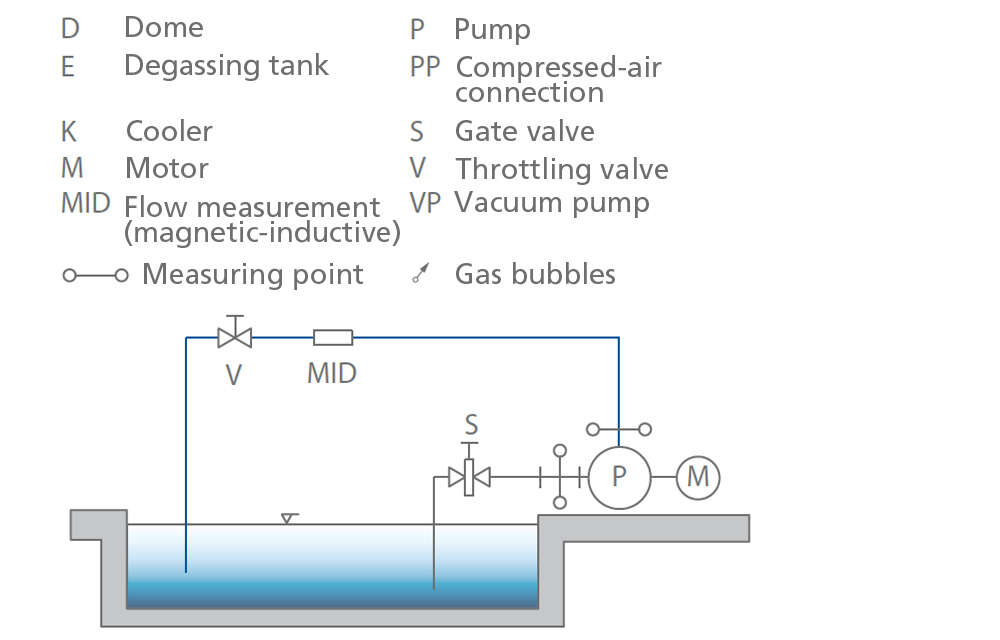
Fig. 1 Pump test facility: “Open” test bed (schematic)
In the case of closed test beds (so-called loops) a great variety of operating conditions can be simulated by means of suitable system pressures (see NPSH available) regardless of the pumps' installation altitude. This is particularly important when investigating cavitation. See Figs. 2, 3 Pump test facility
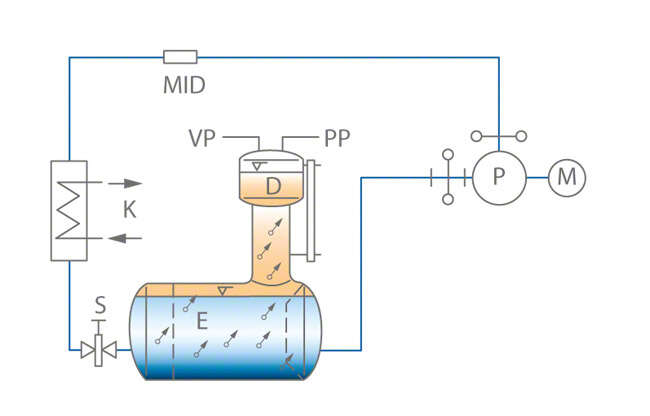
Fig. 2 Pump test facility: Closed-loop test set-up (schematic)
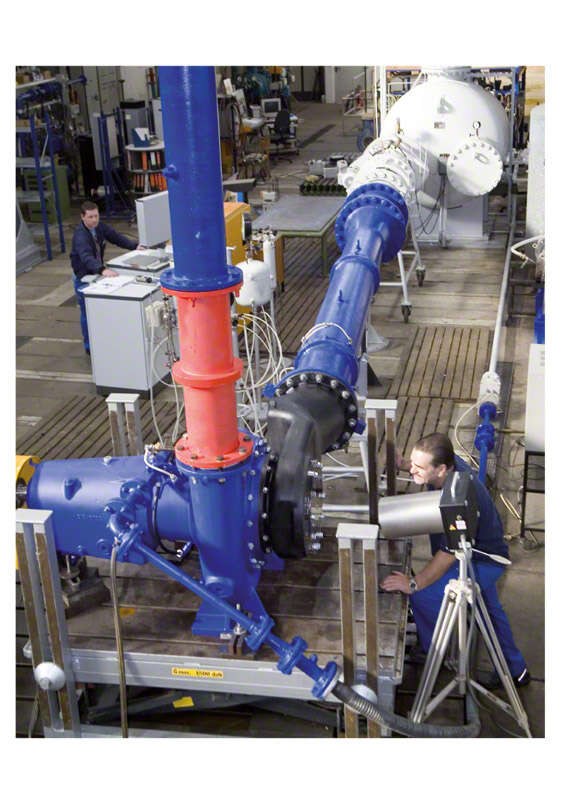
Fig. 3 Pump test facility: View of closed-loop test set-up (cavitation test facility)
In order to measure and assess the operating behaviour of pumps, a number of characteristic quantities must be measured or calculated from the measured values. This ensures that the following quantities can be determined during the performance test: flow rate, head, torque, power input, speed, drive rating, NPSH and, where applicable, temperatures
Despite the fact that centrifugal pumps can be, or indeed, have to be tested in situ in the system (particularly where a high power input is involved), the pump test facilities used within the field of centrifugal pump technology must be continually improved, adapted or planned all over again. In future, the test facility measurements that constitute the final testing of the individual products, for example, are going to be streamlined even further. Thanks to the increased use of electronic data processing systems, the pump testing process is becoming largely automated. As part of this, the measured data can also be fully documented.
Given that pump units are constantly increasing in size, it is not always possible to carry out tests on the pump test facility under original conditions.
As a result, tests can be carried out at reduced speed, as permitted by the relevant standards. Alternatively, there is the option of carrying out a model test. In this case, tests are carried out on a scaled-down model of the centrifugal pump to be tested. However, these tests call for a very high level of precision, as the results are extrapolated to real-life conditions (see Affinity laws).
Criteria for planning a pump test facility
- Role of pump test (problem definition)
- Relevant standards (see Acceptance test codes)
- Measuring instruments used
- Test facility set-ups
- Special measuring devices
Role of the pump test
The role of the pump test is to verify the operating and performance data, to check functional reliability and to identify ways of improving and advancing products (research and development).
Within this context, it has to be possible to measure pressures, flow rates, input and output powers, speeds, noise emissions, strength levels, and vibrations and to assess the behaviour of the pumps under certain conditions (see Operating behaviour).
Measuring instruments used
The measuring instruments used for acceptance tests must meet stringent precision requirements and must undergo official and in-house calibration (repeat calibration cycles recommended in DIN EN ISO 9906). These precision requirements are defined by the test class of the acceptance standard that is used.
Pressure measurements
- In general, the following are sufficient on a pump test facility: electronic pressure transmitters, pressure sensors and spring pressure gauges (class 0.6). Within this context, the maximum permissible error level permitted for the instrument is 0.6 % of the full scale deflection.
- In special cases, such as when recording processes (e.g. non-steady flow), suitable sensors and data loggers are required for high-frequency recordings.
Measuring flow rates
- In the case of low flow rates, reservoir measurements can be performed.
- On the pump test facility, it is more common to use standardised throttles in accordance with ISO 5167 (see Standard orifice plate, Standard nozzle and Standard Venturi nozzle, Venturi tube) as well as instruments for measuring velocity MIF (magnetic-inductive flow metering) or ultrasonic flow metering and instruments for measuring mass in accordance with the CORIOLIS principle.
- In the case of very high flow rates, special procedures must be used such as vane measurements over the cross section.
Power measurements
- For very precise measurements on the test facility, it is advisable to use torque meters between the motor and pump. This is generally done in conjunction with speed measurement.
- Normally, the electrical power consumed by the drive is measured using the two-wattmeter method. The motor is usually calibrated by determining the individual loss.
Drehzahlmessungen
- Speed measurements are often taken on the pump test facility using digital counters which count discrete pulses with every revolution.
- If 60 pulses per revolution are selected together with a count period of 1 second, it is possible to display the speed directly in min–1. At ± 1 min–1 the display accuracy is extremely high.
- Simplified speed measurements can also be taken using manually incremented revolution counters and tachometers in accordance with the eddy current principle (error: 0.5% and lower).
Special measuring devices
- Special requirements sometimes apply when taking noise and vibration measurements, NPSH measurements, and when carrying out model testing in water, rolling element and plain bearing tests, endurance tests and tests involving toxic, hot, explosive fluids handled. These special requirements must be taken into account when planning a pump test facility (see safety regulations).
- In special cases, velocity measurements are taken using laser and ultrasonic technology.
Specific features of test beds
When tests are carried out in an open or closed circuit in accordance with the test bed's capabilities, all the pump output power is converted into heat.
Consequently, a relatively large test water reservoir is required. Cooling equipment may also be required.