Noise in pumps and systems
The noise emitted by pumps and systems is caused by vibrations in the piping and the pump casing. These vibrations interact with the surrounding air and are perceived as airborne sound.
Transient flow and the pressure fluctuations associated with it produce this effect. The fluctuations occur when energy is transferred via the impeller vanes to the fluid handled. The finite number of vanes leads to periodic pressure fluctuations with amplitudes of varying intensity. Since the flow encounters continually increasing static pressure, the boundary layers are at great risk of separating. The flow pattern of the fluid flowing around the vanes as well as flow separation make the flow in a centrifugal pump transient.
For single-stage volute casing pumps comprising a few basic components, these transient flows are the main source of noise apart from that generated by the drive of the centrifugal pump.
Multistage pumps with balancing devices also produce substantial turbulence noise (see Fluid mechanics) resulting from the characteristically high delivery heads of the individual stages, as can higher pressures when they are relieved in balancing devices, for example.
The aforementioned sources of noise relate to pumps and systems operated in the absence of cavitation. When cavitation occurs in a pump or valve the level of noise produced is considerably more pronounced. Cavitation noise typically sounds like a high-pitched crackling and transitions to an intense rattling sound when the effect intensifies (i.e. lower NPSH).
Cavitation noise contributes to the overall noise emitted by pumps and systems and necessitates further outlay for any noise control measures that are required. It can also be used, however, for detecting and - by using suitable measuring equipment and analysis methods - acquiring information about the intensity and erosive potential of cavitation conditions.
The trend toward higher rotational speeds exacerbates the problem of noise in centrifugal pumps, which leads to smaller, more powerful machines (increased power density). Adding to this is the fact that better use is being made of materials to reduce wall thickness. Doing this, however, also makes the pumps more conducive to vibrations.
The influences of individual components on the overall noise emitted by a pump set are complex and hinge on many factors. See Fig. 1 Noise in pumps and systems
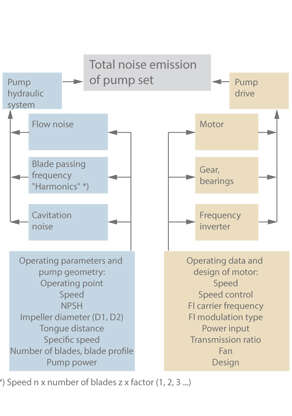
Fig. 1 Noise in pumps and systems: Factors influencing total noise emissions of the pump set
Characteristic sound power levels can be assessed in accordance with VDI 3749, which provides emission values for different technical sound sources.
The influential effect of foundations (see Pump foundation), buildings (with extended periods of heavy reverberation), piping, and adjacent machines and systems is particularly difficult to estimate.
Guidelines and technical codes exist for measuring noise (see Noise measurement).
Statistical analyses have revealed that, depending on the type of pump and in non-cavitating operation, 10-9 to 10-6 of a centrifugal pump's power input is converted to sound power, which may take the form of solid-borne, air-borne and liquid-borne sound. See Fig. 2 Noise in pumps and systems
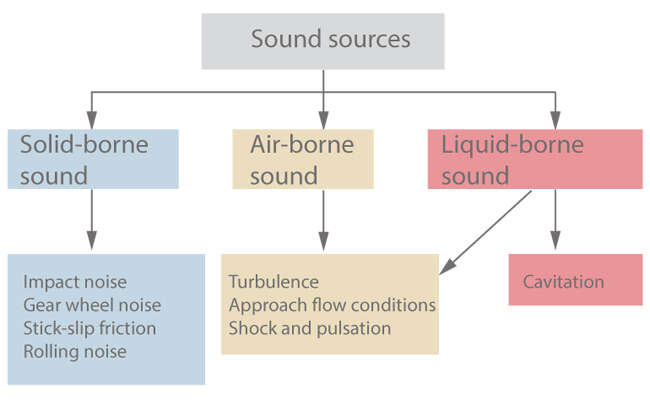
Fig. 2 Noise in pumps and systems: Centrifugal pump sound sources
Noise control
The most critical active sound-absorbing measure for noise control is the correct selection of the pump itself, which must be designed for the task in question and have the correct size.
The sound of a centrifugal pump varies in intensity along its H/Q curve depending on the operating point. To conserve energy and minimise noise, pumps should generally be run at the operating point that provides optimum pump efficiency. Noise is usually lowest when the pumps are operated at a speed near BEP.
Passive sound-absorbing measures are a necessity when centrifugal pumps are used in applications with stringent noise restrictions, and include expansion joints in the piping installation of the pump set on rubber-metal or spring mounts, in sound enclosures and insulated rooms in which pump sets are operated with special sound-proofing or sound-dampening panels.