The plain bearing is an element frequently used in centrifugal pump construction that allows a moving component to slide within a stationary component. A distinction is made between radial plain bearings for radial forces (transverse forces) and axial (or thrust) plain bearings for axial forces (longitudinal forces). See Fig. 1 Plain bearing
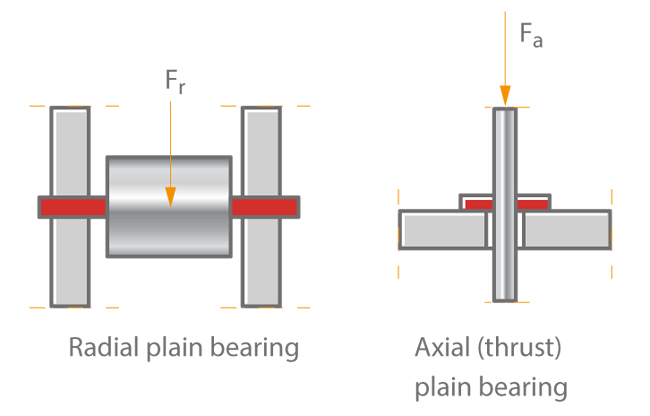
Radial plain bearing
On radial plain bearings, the moving part is the pin or journal of the axle or shaft; the stationary part is the bearing shell.
Bearing shells and other variants
- a Cylindrical bearing shell
see Fig. 2 a Plain bearing - b Two-face, lemon-bore bearing shell
see Fig. 2 b Plain bearing - c Two-face, radially offset bearing shell
see Fig. 2 c Plain bearing - d Three-face bearing shell
See Fig. 2 d Plain bearing - e Three-face and multiple-face bearing shell with lubrication grooves or pockets
see Fig. 2 e Plain bearing - f Rubber bearing
see Fig. 2 f Plain bearing - g Multiple-face bearing with tilting radial pads
see Fig. 2 g Plain bearing
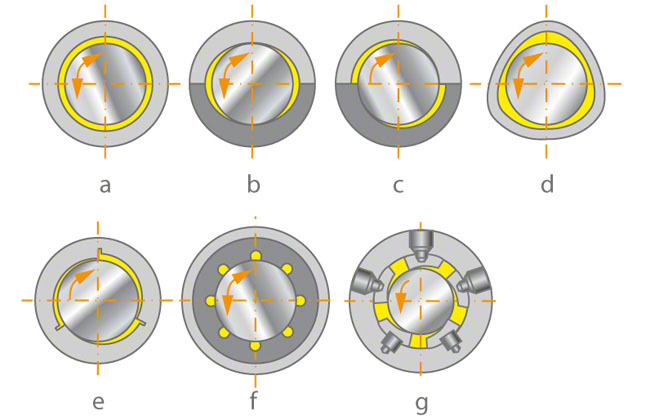
This wide range of bearing designs is required to cater for the dynamic operating behaviour characteristic of centrifugal pump rotors. The vibration characteristics of rotors fitted with plain bearings depend largely on the rotor mass, the mass distribution, the shaft stiffness and the dampening characteristics of the bearings at a given load.
Appropriate rotor bearing design allows both types of lateral rotor vibrations (forced and self-induced) to be eliminated or reduced to an acceptable level for the machine. The dynamic bearing coefficients can be optimised. The choice of bearings is a key element of this optimisation, as each bearing offers different performance characteristics.
A bearing clearance is achieved through the appropriate sizing and mutual adjustment of both the moving and stationary bearing components.
This is filled with a liquid or solid (grease type) lubricant in order to avoid sliding friction. When the bearing journal reaches a sufficient circumferential speed, the bearing clearance allows the lubricant to form a load-bearing wedge. The lubrication wedge separates the sliding faces from one another, meaning that the bearing is operating on full lubrication. This process is typical of hydrodynamic plain bearings.
Advantages and disadvantages of hydrodynamic plain bearings
Advantages:
- Simple manufacture; the lubricant is fed either unpressurised or at very low feed pressure into the bearing during operation
- Very little or no energy is required for the oil supply system
Disadvantages:
- During start-up and run-down, full fluid film lubrication is impossible, resulting in wear on the running surfaces (mixed friction) see Fig. 4 Plain bearing
Another bearing type is the hydrostatic plain bearing. Here, the liquid lubricant is fed into the individual bearing pockets under high pressure.
Forces are absorbed as a result of pressure differences:
- High static pressure in the pockets on the loaded side of the running surface (small clearance during operation, therefore very small decrease in pressure in the lubricant layer)
- Low static pressure in the pockets of the unloaded side of the running surface (large clearance during operation, therefore considerable pressure drop in the lubricant layer)
Advantages and disadvantages of hydrostatic plain bearings:
- Advantage: full fluid film lubrication at all times, including start-up and run-down, therefore no excessive wear risk
- Advantage: smaller dimensions and lower friction losses in comparison with hydrodynamic bearings of equal load-bearing capacity
- Disadvantage: more expensive to manufacture than hydrodynamic plain bearings (several manufacturing operations)
- Disadvantage: more expensive to operate because pressure boosting is required for the lubricant, leading to increased investment and energy costs
Hydrodynamic and hydrostatic types can be combined. In the case of plain bearings which operate hydrodynamically in the steady state, the increased friction during start-up and run-down and the wear associated with it can be reduced by providing auxiliary hydrostatic lubrication at a high pressure via longitudinal grooves which do not extend to the edge of the bearing shell.
The auxiliary lubricant feed is shut off during normal operation to ensure that the hydrodynamic pressure is maintained in the lubricating clearance gap.
Friction conditions in a plain bearing
See Fig. 3 Plain bearing:
a. Dry friction:
without a separating lubricant layer between the stationary and moving components
b. Mixed friction:
a combination of dry and fluid friction
c. Fluid friction:
with a separating lubricant layer (ideal situation)
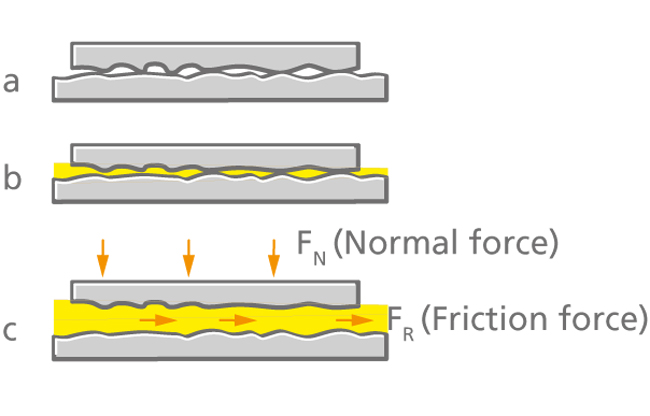
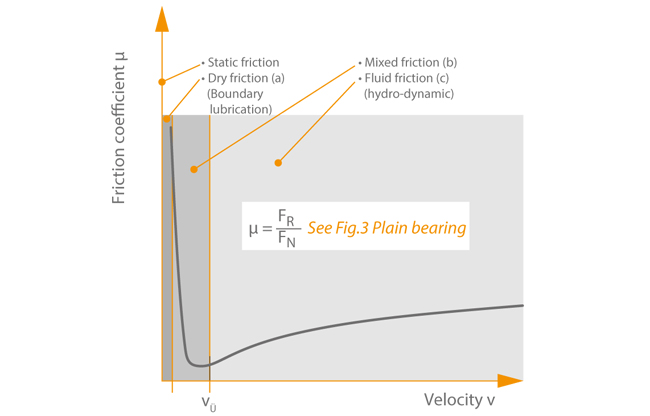
All three friction types can occur in hydrodynamic plain bearings during the three phases of operation: start-up, operation, run-down. Start-up is the operating phase from standstill to full operating speed. As the sliding velocity increases, hydrodynamic plain bearings experience mixed friction, with the amount of dry friction gradually giving way to fluid friction as speed increases further. Finally the transition point is reached when the surfaces separate from one another and full fluid film lubrication with a minimum of friction losses is established.
As the sliding velocity increases further, the thickness of the lubricant film also increases, but friction losses rise again slightly. See Fig. 5 Plain bearing
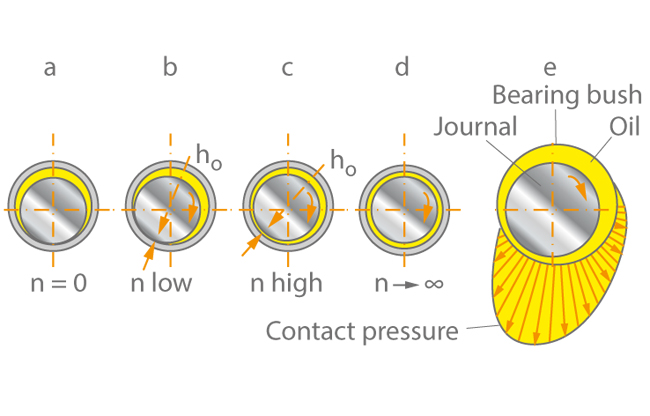
This frictional behaviour was the subject of research by Stribeck. See Fig. 4 Plain bearing
As a machine runs down, the plain bearings undergo the same process as described above for start-up, but in the reverse order (see Start-up process).
A plain bearing should generally have its steady-state operating point during the full fluid film lubrication phase. If mixed friction is present during continuous operation, excessive wear at the bearing faces can be expected. Particular care should be taken to correctly select and match the two materials whose surfaces require lubrication (wear, heat dissipation).
Many pumps are equipped with shaft guide bearings which are lubricated by the fluid handled. In these cases the choice of bearing materials is especially important as each fluid has its own characteristics as a lubricant. If clean water is used as a lubricant, several bearing materials with suitable tribological properties are available. These include metallic alloys, elastomers, hard rubber, electro-graphite with or without resin binders, hard graphite with or without resin binders or antimony impregnation.
If the fluid handled is used as a lubricant and is dirty or contains solids such as sand, the bearing materials should be made from hard metals or ceramic materials (e.g. silicon carbide). Using the same material for bearing bushes and shaft protecting sleeves results in a maintenance-free bearing.
Fibre-reinforced ceramic bearings are being used more and more frequently due to their ability to resist tension and fractures. See Fig. 6 Plain bearing
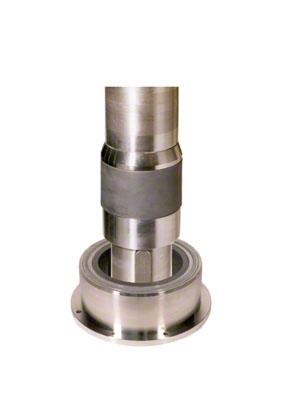
Friction is converted into heat which is partly dissipated to the surrounding air via the bearing housing or the shaft. The plain bearing should therefore not exceed the max. bearing operating temperature. If necessary, a cooling system must be provided for the bearing or lubricant (usually water cooling).
The design of hydrodynamic plain bearings involves the solution of a complex problem which takes into account a number of factors such as bearing geometry and size, bearing load, the lubricant's viscosity the sliding velocity, the nature of the flow in the bearing (see Fluid mechanics) and the interaction between these factors.
The objective of plain bearing design is to ensure that full fluid film lubrication can be reliably achieved during operation. The design process incorporates theoretical principles and experimental data, taking into account multiple interrelated characteristic coefficients (i.e. those relating to radial plain bearings): see Fig. 7 Plain bearing
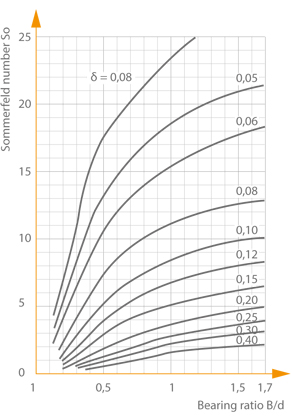
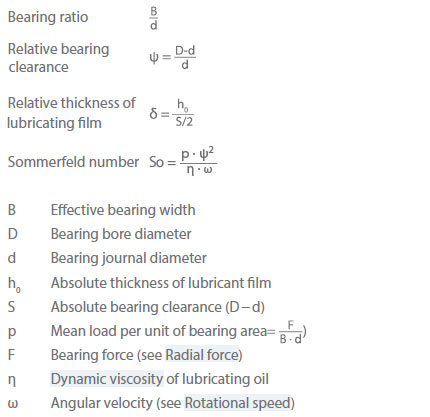
Plain bearings whose lubricant does not exhibit purely laminar flow characteristics (i.e. bearings with very high speeds and simultaneously very low lubricant viscosities tend to have a higher load-bearing capacity, but also higher friction losses. Here, the qualitative difference between a laminar and a turbulent flow plays a decisive role, alongside the characteristic coefficients for plain bearings already mentioned. Designing plain bearings with turbulent lubricant flow is much more complicated than designing bearings with laminar lubricant flow.
Axial (thrust) plain bearing
The moving part of an axial (thrust) plain bearing is the thrust collar or plate.
Stationary part and its variants
See Fig. 8 Plain bearing:
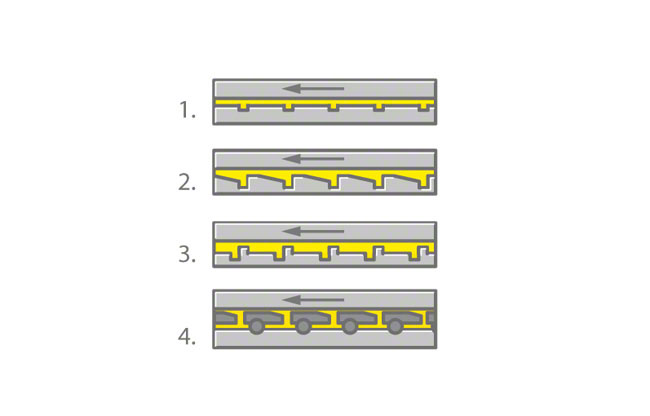
- Thrust bearing ring
- Thrust bearing ring with machined wedge faces
- Thrust bearing ring with stepped damming gap
- Eccentrically supported tilting pads or often centrally supported tilting pads (e.g. where a cooling water pump has to rotate in reverse (turbine mode) because of a backflow from the piping)
Depending on the design axial (thrust) plain bearings are subdivided into hydrodynamic, hydrostatic and combined hydrostatic-hydrodynamic plain bearings for special applications. Both basic design types must allow sufficient axial shaft movement to accommodate the lubricant film thickness, which varies according to load, viscosity of the lubricant, and sliding velocity. The same arguments as for radial plain bearings apply to the advantages and disadvantages of hydrodynamic versus hydrostatic axial (thrust) plain bearings. Fig. 9 Plain bearing illustrates a product-lubricated carbon bearing in a circulating pump.
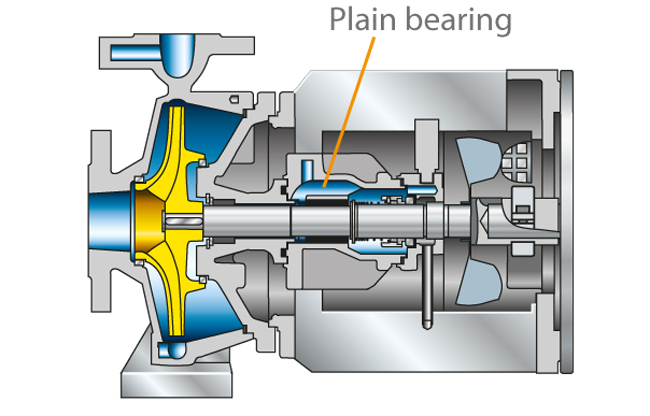