Das Gleitlager ist ein im Kreiselpumpenbau häufig verwendetes Element, bei dem ein bewegtes in einem feststehenden Teil gleitet. Es wird zwischen dem Radial-Gleitlager für Radialkräfte (Querkräfte) und Axial-Gleitlager für Axialkräfte (Längskräfte) unterschieden. siehe Abb. 1 Gleitlager
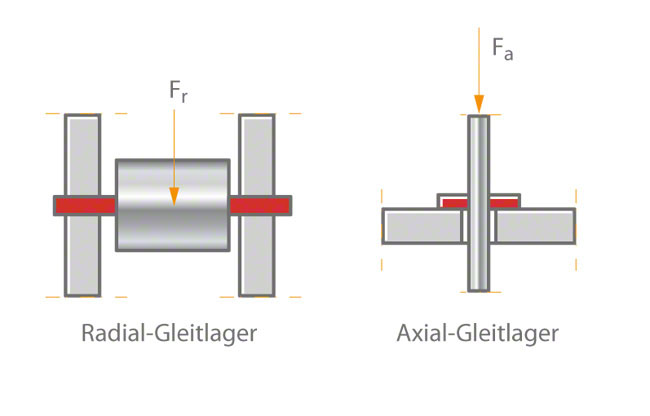
Radial-Gleitlager
Beim Radial-Gleitlager ist der bewegte Teil der Zapfen der Achse oder Welle; der feststehende Teil die Lagerschale.
Lagerschale und verschiedene Varianten
- a zylindrische Lagerschale siehe Abb. 2a Gleitlager
- b Zweiflächenlagerschale mit Zitronenspiel siehe Abb. 2b Gleitlager
- c Zweiflächenlagerschale mit radialer Versetzung siehe Abb. 2c Gleitlager
- d Dreiflächenlagerschale siehe Abb. 2d Gleitlager
- e Drei- und Mehrflächenlagerschale mit Schmiernuten oder -taschen siehe Abb. 2e Gleitlager
- f Gummilager siehe Abb. 2f Gleitlager
- g Mehrflächenlager mit kippbaren Radialsegmenten siehe Abb. 2g Gleitlager
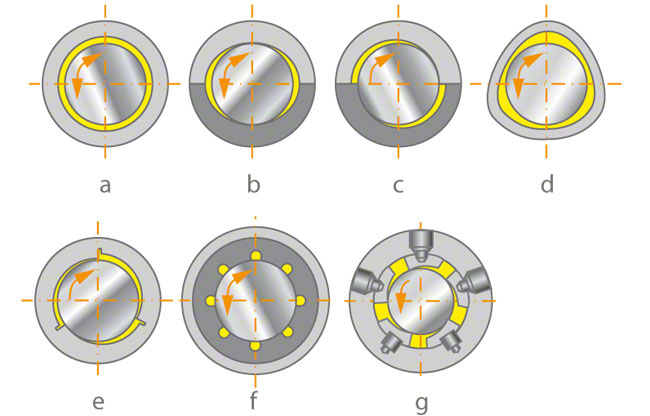
Die hier angedeutete Vielfalt der möglichen Lagerformvarianten hängt mit der Beherrschung des dynamischen Betriebsverhaltens von Kreiselpumpenrotoren zusammen. Das Schwingungsverhalten gleitgelagerter Rotoren wird im Wesentlichen von der Masse des Rotors, der Massenverteilung, der Biegefestigkeit der Welle sowie von den Federungs- und Dämpfungseigenschaften der Lagerung unter gegebenem Lastfall bestimmt. Durch eine geeignete Gestaltung der Rotorlagerung können beide Arten von Querschwingungen (zwangs- und selbsterregte Schwingung) des Rotors entweder ganz verhindert oder auf einen für den mechanischen Lauf der Maschine zulässigen Wert begrenzt und damit die dynamischen Lagerkennwerte optimiert werden. Die Wahl der Lagerform stellt einen wesentlichen Bestandteil dieser Optimierung dar, weil unterschiedliche Lagerformarten auch unterschiedliche Eigenschaften aufweisen.
Durch geeignete Fertigungsmaße der bewegten und feststehenden Funktionsteile und deren gegenseitige Einstellung entsteht ein Lagerspiel, das meist mit einem flüssigen oder konsistenten (fettartigen) Schmierstoff zur Vermeidung von gleitender Reibung versorgt wird. Durch dieses Lagerspiel kann sich in dem vorhandenen Raum bei genügender Umfangsgeschwindigkeit des Lagerzapfens ein tragender Schmierkeil aus dem Schmierstoff formen. Der Schmierkeil trennt die aufeinander gleitenden Teile, sodass das Lager mit Vollschmierung arbeitet. Dieser Vorgang ist typisch für die hydrodynamischen Gleitlager.
Vor- und Nachteile der hydrodynamischen Gleitlager
Vorteile:
- einfache Fertigung, um Schmiermittel im Betrieb dem Lager drucklos oder mit nur geringem Vordruck zuzuführen
- kein oder nur geringer Energieaufwand ist für die Ölversorgungsanlage aufzubringen
Nachteile:
- beim An- und Auslauf der Maschine ist keine reine Flüssigkeitsreibung vorhanden, was einen Verschleiß an den Laufflächen zur Folge hat (Mischreibung) siehe Abb. 4 Gleitlager
Eine andere Bauart ist das hydrostatische Gleitlager. Hier wird der flüssige Schmierstoff unter hohem Druck den einzelnen Druckkammern der Lauffläche zugeführt.
Lagerkraftaufnahme aufgrund von Druckunterschieden:
- hoher statischer Druck in den Kammern an der belasteten Laufflächenseite (kleines Betriebslagerspiel mit geringer Abnahme des Druckes in der Schmierschicht)
- geringer statischer Druck in den Kammern an der entlasteten Laufflächenseite (großes Betriebslagerspiel mit großer Abnahme des Druckes in der Schmierschicht)
Vor- und Nachteile der hydrostatischen Gleitlager:
- Vorteil: immer reine Flüssigkeitsreibung auch beim An- und Auslaufen vorhanden, wodurch keine Verschleißgefahr besteht
- Vorteil: gegenüber hydrodynamischen Lagern bei gleicher Tragkraft geringere Abmessungen und geringere Reibleistung
- Nachteil: aufgrund mehrerer Fertigungsvorgänge sind sie teurer in der Fertigung als hydrodynamische Gleitlager
- Nachteil: sie sind teurer im Betrieb, da eine Druckerhöhungsanlage für die Schmierflüssigkeit erforderlich ist und auch die Investitions- und Energiekosten erhöht werden
Die hydrodynamische und -statische Bauart lassen sich kombinieren. So kann durch eine hydrostatische Zusatzschmierung mit hohem Schmiermitteldruck bei Gleitlagern im hydrodynamischen Betrieb die Anfahr- und Auslaufreibung in nicht nach außen durchzogenen Längsnuten vermindert und der Verschleiß vermieden werden. Im normalen Betrieb werden die Zuleitungen geschlossen, damit der hydrodynamische Druck im Schmierspalt erhalten bleibt.
Reibungszustände eines Gleitlagers
siehe Abb. 3 Gleitlager
a. Trockenreibung:
ohne Trennschicht des Schmiermittels zwischen bewegtem und feststehendem Körper
b. Mischreibung:
teilweise Trocken- und Flüssigkeitsreibung
c. Flüssigkeitsreibung:
mit einer Trennschicht des Schmiermittels (Optimalzustand)
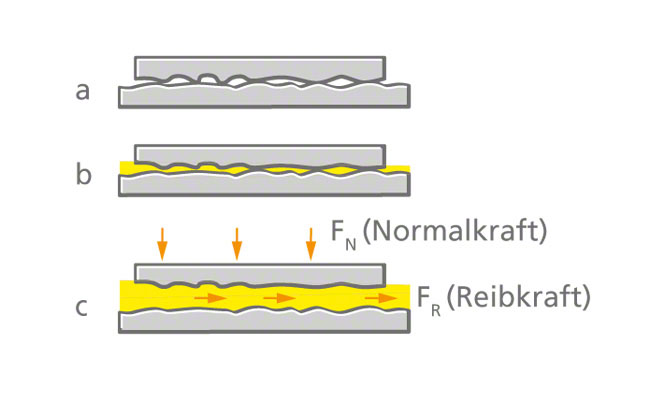
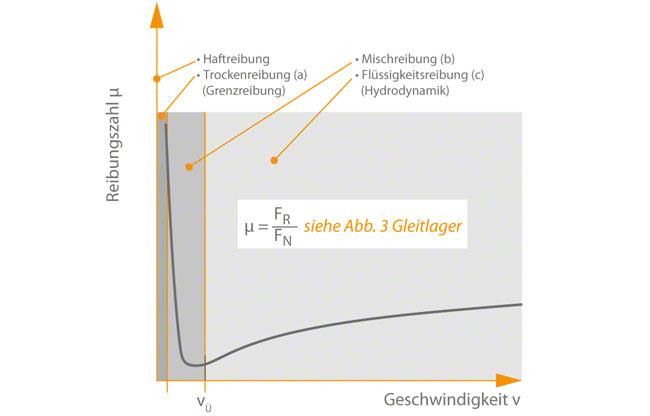
Dieses Reibungsverhalten wurde von STRIBECK durch Versuche geklärt, siehe Abb. 4 Gleitlager. Beim Auslauf der Maschine ergibt sich für das Gleitlager die Umkehrung des Anlaufvorganges. Ein Gleitlager sollte meist im Bereich der Flüssigkeitsreibung seinen normalen Betriebspunkt haben. Soweit im Dauerbetrieb eine Mischreibung herrscht, ist mit Verschleiß an den Gleitflächen zu rechnen. Die Wahl der Materialpaarung spielt bzgl. des Verschleißes und der Wärmeabfuhr bei den Laufflächen eine wesentliche Rolle.
Viele Pumpen sind mit fördermediumgeschmierten Wellenführungslagern ausgerüstet. In diesen Fällen muss die Materialwahl besonders sorgfältig vorgenommen werden, da hier oft spezielle Eigenschaften des Schmiermittels zu berücksichtigen sind. So gibt es für reines Wasser als Schmiermittel mehrere Lagerwerkstoffe mit guten tribologischen Eigenschaften. Dazu gehören bspw. metallische Legierungen, Elastomere, Hartgummi, elektrographitierte Kohle mit und ohne Kunstharztränkung sowie Hartkohle mit Kunstharz- oder Antimontränkung. Ist ein Fördermedium als Lagerschmierstoff verschmutzt oder enthält es feste Beimengungen wie bspw. Sand, so ist der Einsatz von Hartmetallen oder keramischen Werkstoffen (z. B. Siliziumkarbid) als Lagerwerkstoff zu empfehlen. So bilden die Lagerbuchsen und Wellenschutzhülsen gleichen Werkstoffes ein wartungsfreies Gleitlager. Um die Zug- und Bruchempfindlichkeit zu minimieren, werden vermehrt faserverstärkte Keramiklager eingesetzt. siehe Abb. 6 Gleitlager
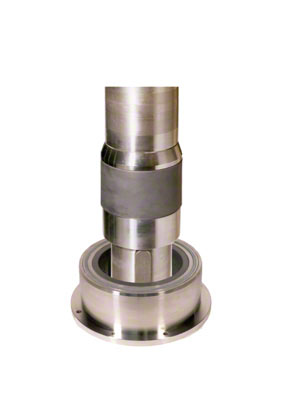
Die Reibungsleistung setzt sich in Wärme um, die teilweise vom Lagergehäuse an die umgebende Luft oder von der Welle abgeführt wird. Dabei darf das Gleitlager die höchste Lagerbetriebstemperatur nicht überschreiten. Im Bedarfsfall muss ein Kühlsystem für das Lager oder Schmierstoff (meist Wasserkühlung) vorgesehen werden.
Die Auslegung von hydrodynamischen Gleitlagern stellt die Lösung einer komplexen Aufgabe dar, bei der Geometrie und Größe des Lagers, Lagerlast, Viskosität des Schmierstoffes, Gleitgeschwindigkeit und Art der Strömung im Lager (siehe Strömungslehre) sowie deren gegenseitige Beeinflussungen eingehen.
Ziel einer Gleitlagerauslegung ist es, möglichst sicher eine reine Flüssigkeitsreibung beim Betrieb entstehen zu lassen. Der Auslegungsablauf beruht teilweise auf theoretischen und experimentellen Unterlagen, die in geeigneter Weise mehrere Kennzahlen in ihren Zusammenhängen wie bspw. für ein Radial-Gleitlager wiedergeben: siehe Abb. 7 Gleitlager
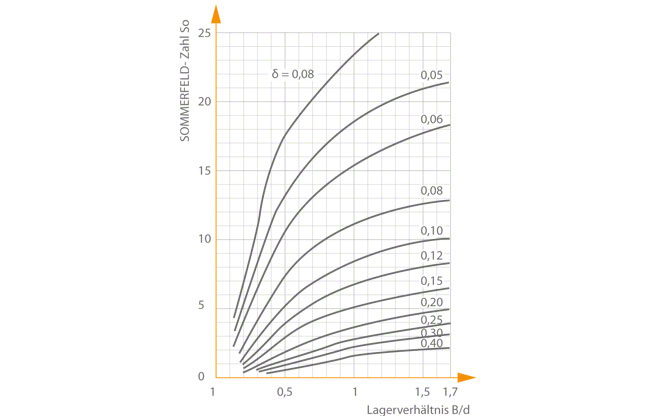
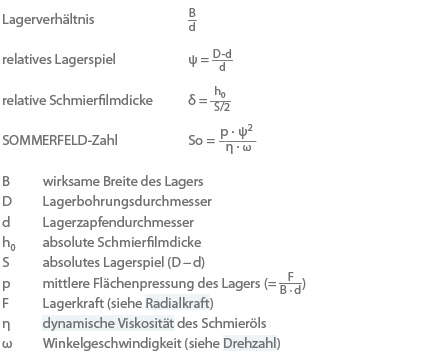
Gleitlager mit nicht rein laminaren Strömungsvorgängen wie bei Lagern mit sehr hohen Gleitgeschwindigkeiten und gleichzeitig sehr niedrigen Viskositäten des Schmierstoffes weisen im Vergleich mit rein laminaren Gleitlagern höhere Tragfähigkeit und höhere Reibungsverluste auf. Neben den schon erwähnten Gleitlagerkennzahlen spielt hier der qualitative Unterschied zwischen einer laminaren und turbulenten Strömung eine ausschlaggebende Rolle. Eine Auslegung eines turbulenten Gleitlagers ist im Vergleich zum laminaren wesentlich schwieriger.
Axial-Gleitlager
Die Axial-Gleitlager bestehen auch aus einem bewegten (Axiallagerteller) und feststehenden Teil.
Feststehender Teil und deren Varianten
siehe Abb. 8 Gleitlager
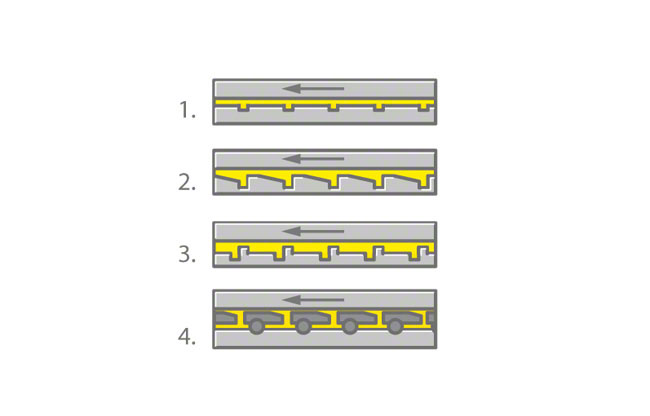
- Axiallagerring
- Axiallagerring mit eingearbeiteten Keilflächen
- Axiallagerring mit gestuftem Stauspalt
- außermittig gestützte, kippbare Segmente oder häufig auch mittig gestützte, kippbare Segmente (z. B. bei Turbinenbetrieb einer Kühlwasserpumpe bei Rückströmung aus dem Rohrleitungssystem)
Nach der Bauart wird zwischen hydrodynamischen, -statischen und für spezielle Anwendungen kombinierten hydrostatisch-hydrodynamischen Axial-Gleitlagern unterschieden. Für beide Grundbauarten muss durch Konstruktionsmaßnahmen die Möglichkeit einer axialen Bewegung der gelagerten Welle gegeben sein. Diese sollte mindestens der Größe der sich aus Belastung, Viskosität des Schmiermittels und der Gleitgeschwindigkeit ergebenden Dicke des Schmierfilmes entsprechen. Die Vor- und Nachteile hydrodynamischer und hydrostatischer Axial-Gleitlager entsprechen denen bei Radial-Gleitlagern. Abb. 9 Gleitlager zeigt ein fördermediumgeschmiertes Kohlelager in einer Umwälzpumpe.
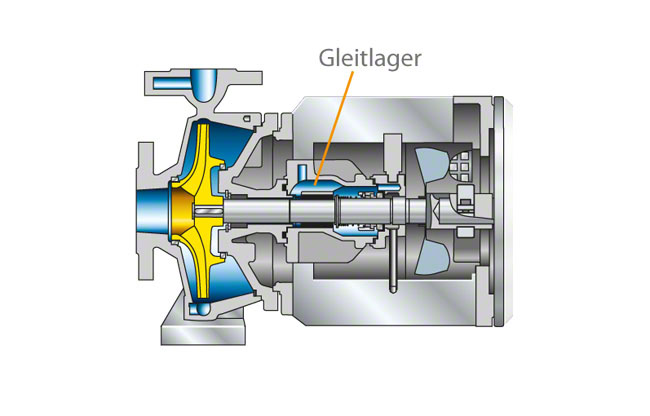