Die Wellendichtung ist eine Dichtung, die eine Kreiselpumpe an der Durchführung der rotierenden Pumpenwelle aus dem feststehende Pumpengehäuse so abdichtet, dass der Leckverlust oder die von außen eindringende Luft auf ein bestimmtes Maß reduziert und ein etwaiger Verschleiß der Dichtflächen so gering wie möglich wird. Pumpen werden für viele unterschiedliche Anwendungen ganz spezifisch ausgelegt, konstruiert und gefertigt. Dies schließt auch die Medienbeständigkeit, Temperatur und den Pumpendruck ein. Aus einer Vielzahl von verschiedenen Wellendichtungen erfolgt dann die individuell diesen Anforderungen entsprechende Auswahl.
Prinzipiell stehen dafür die zwei folgenden Konstruktionsprinzipien zur Verfügung: Abdichtung mithilfe eines engen Radialspaltes (parallel zur Wellenachse) oder eines engen Axialspaltes (rechtwinklig zur Wellenachse). Bei beiden Dichtungsprinzipien können die Spalte sowohl berührend als auch nicht berührend ausgeführt sein. siehe Abb. 1 Wellendichtung
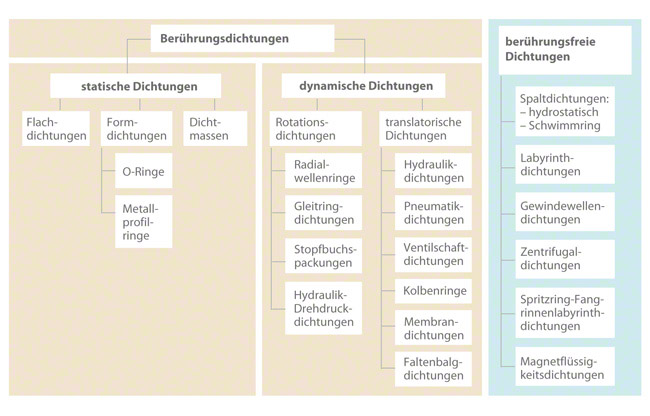
Werden nur nicht berührende Spalten als Dichtelemente eingesetzt, tritt auch immer in erheblichem Umfang Leckage auf. Bei umweltbelastenden Fördermedien eignet sich dieses Abdichtsystem daher weniger.
Generell sind Wellendichtungen leckagebehaftet, und bei einigen Ausführungen ist zur ordnungsgemäßen Funktion die Leckage geradezu notwendig, sodass die Angabe Zero-Leckage (Null-Leckage) deshalb irreführend ist. Allerdings ist die Spannweite der Leckage, je nach gewählter Abdichtung, sehr groß. So hat eine von einer Packung abgedichtete Spiralgehäusepumpe mit einer Umfangsgeschwindigkeit an der Abdichtstelle von 20 m/s und einem abzudichtenden Druck von 15 bar eine Leckage von etwa 5-8 l/h. Unter gleichen Bedingungen beträgt die Leckage bei einer Gleitringdichtung nur ca. 6 cm3/h (0,006 l/h).
Eine besonders hohe Leckage zwischen 4 bis 6.000 l/h hat dagegen z. B. eine Kesselspeisepumpe mit einer Schwimmringdichtung bei einem Abdichtdurchmesser von 200 mm und abzudichtendem Druck von 40 bar sowie einer Drehzahl von 6.000 U/min (~ 63 m/s).
Aufgrund der sehr unterschiedlichen Pumpenbauarten sind nicht alle Dichtungen für jeden Einsatzfall gleich gut geeignet. Ein Einsatz ist abhängig von der Gleitgeschwindigkeit, dem abzudichtenden Druck und der Mediumstemperatur. siehe Abb. 2 Wellendichtung
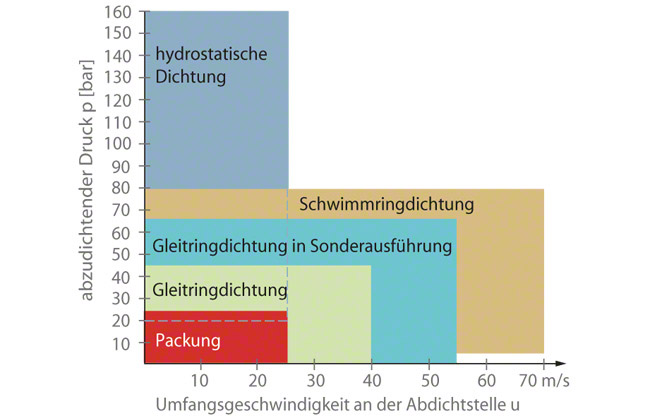
Berührende Wellendichtung
Bei der berührenden Wellendichtung als dynamische Berührungsdichtung bewegen sich die Dichtelemente relativ zueinander. Aus diesem Grund sind lippen- und linienberührte Wellendichtungen nur für kleinste Druckdifferenzen wie zur Abdichtung von Öl an Lagerstellen (z. B. Radial-Wellendichtringe) geeignet und meist nicht nachstellbar. siehe Abb. 3 Wellendichtung
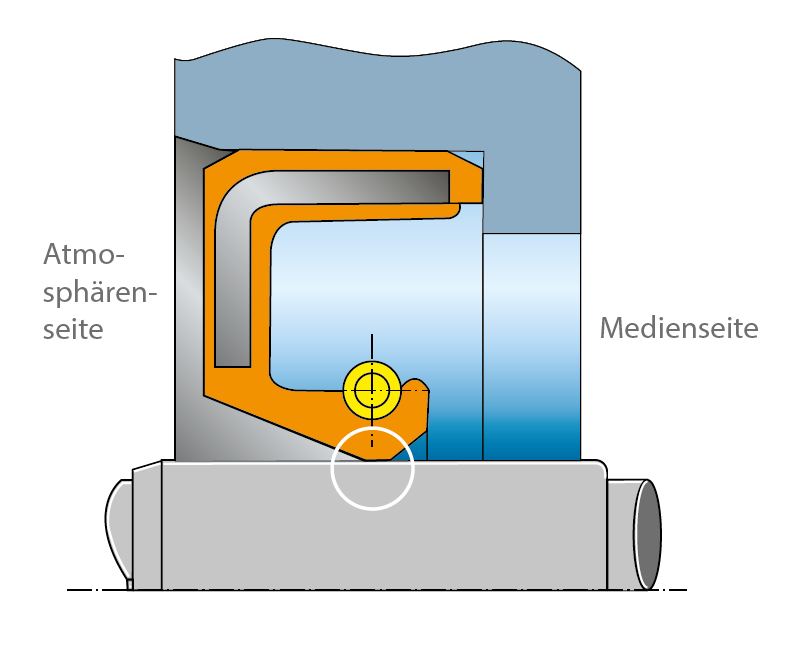
Die berührende Wellendichtung lässt sich in statische und dynamische Dichtungen unterteilen. Zu den dynamischen Dichtungen zählen Stopfbuchspackungen und Gleitringdichtungen. siehe Abb. 1 Wellendichtung
Stopfbuchspackung
Die Einsatzgrenze der Packungsstopfbuchse (Packung) wird wesentlich durch die Möglichkeit des Abführen von Reibungswärme bestimmt. Bei hochbelasteten Packungsstopfbuchsen erfolgt sogar meist eine Vorkühlung des Leckwassers mittels innen gekühlter Wellenschutzhülse und außen liegendem Kühlmantel.
Als Packungswerkstoffe kommen meist geflochtene Schnüre zum Einsatz, die aus asbestfreien Garnen wie Ramie, Aramid, PTFE, Grafitfaser oder auch Baumwolle auf Spezialmaschinen zu endlosen Vierkantzöpfen geflochten werden. Die Packungen sind nachstellbar und für größere Drücke und Umfangsgeschwindigkeiten als Radial-Wellendichtringe geeignet. Je nachdem, ob die Pumpe im Zulauf- oder im Saugbetrieb arbeitet, ob sie sauberes oder verunreinigtes Fördermedium transportiert, kommen unterschiedliche Packungsvarianten zum Einsatz.
Bei Überdruck wird die Stopfbuchse mit drei bis fünf Packungsringen bestückt. Über die Stopfbuchsbrille werden diese Packungsringe axial verpresst. Sie weiten sich dadurch radial auf und der Anpressdruck auf die Wellenschutzhülse steigt an. Damit lässt sich die Spaltweite und auch Leckage an dieser Stelle beeinflussen.
Durch den Radialspalt zwischen Wellenschutzhülse und Packungsringen kann die Leckage dann nach außen gelangen. Diese Leckage wird benötigt, um die durch die drehende Pumpenwelle entstehende Reibungswärme aus dem Spalt zuverlässig abzuführen. Deshalb ist beim Anziehen der Brillenschrauben darauf zu achten, dass ein Kompromiss zwischen einer akzeptablen Leckagemenge und ausreichender Packungskühlung gefunden wird. siehe Abb. 4 Wellendichtung
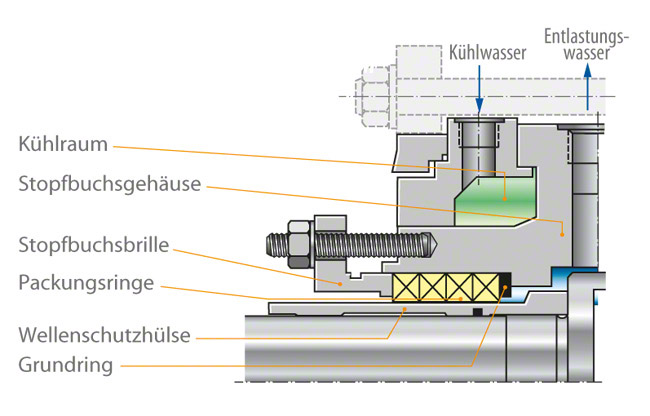
Da im Vergleich zu Gleitringdichtungen Packungen stets eine relativ große Leckage aufweisen, werden diese überwiegend nur bei umweltverträglichen Fördermedien eingesetzt.
Bei Mediumstemperaturen bis zu 120 °C lässt sich die Packung ohne Kühlung betreiben. Für Heißwasser bis zu 180 °C bekommt das Stopfbuchsgehäuse einen Kühlmantel. Bei höheren Temperaturen erfolgt die Kühlung über eine Kombination von innen gekühlter Wellenschutzhülse und außen liegendem Kühlmantel.
Läuft die Pumpe im Saugbetrieb, so sorgen eine Sperrwasserleitung und ein Sperrkammerring hinter dem ersten Packungsring dafür, dass über die Packung keine Luft eingesaugt werden kann. Dieser Sperrwasseranschluss lässt sich vom Druckstutzen der Pumpe her oder über eine interne Bohrung versorgen, wenn die Pumpe sauberes Medium fördert. siehe Abb. 5 Wellendichtung
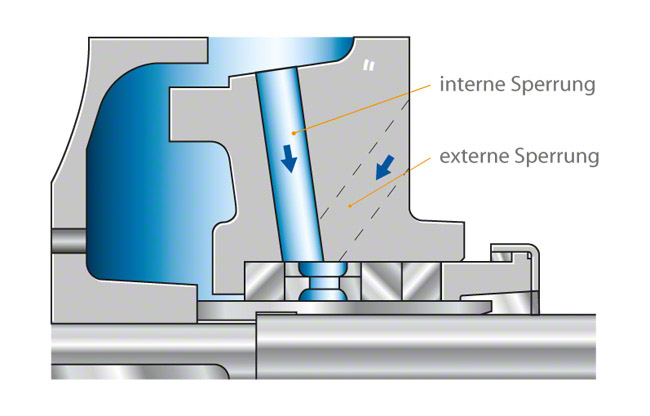
Der gegenüber der Umgebung höhere Pumpenenddruck sorgt dafür, dass keine Luft in die Pumpe eingesaugt wird.
Das Sperrwasser sollte im Normalfall einen Überdruck von ca. 10 % oder mindestens 2 bar gegenüber dem höchsten auftretenden abzudichtenden Druck aufweisen.
Ein Sperrwasseranschluss ist auch im Zulaufbetrieb (Überdruck) notwendig, wenn das Fördermedium verunreinigt ist. In diesem Fall würde der Feststoffanteil mit der Leckage den Weg durch die Packung nach außen suchen. Dabei setzen sich die Feststoffe in der Gleitsohle der Packung fest und zerstören in kurzer Zeit durch einen intensiven Schmirgelvorgang die Wellenschutzhülse. In diesem Fall kommt nur eine Fremdsperrung in Frage. Bei einer solchen Anordnung ist der Sperrkammerring als innerster Ring platziert. siehe Abb. 6 Wellendichtung
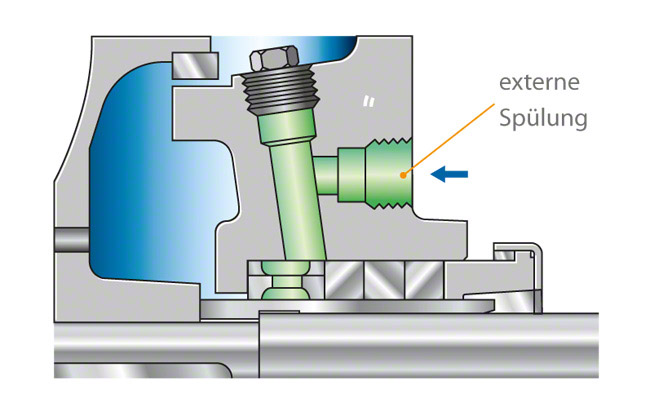
Da der Druck des Sperrmediums höher als der Pumpendruck ist, gelangt ein Teil des Sperrmediums auch in das Pumpeninnere und mischt sich mit dem Fördermedium. Hier ist auf die Verträglichkeit von Sperr- und Fördermedium zu achten. Packungsschnur und Wellenschutzhülse müssen im Revisionsfall stets gemeinsam beurteilt werden. Eine harte, gegen Verschleiß resistente Oberfläche der Wellenschutzhülse wirkt sich auf die Standzeit der Packung in aller Regel positiv aus. Durch Verchromen, Oberflächennitrieren oder Plasmabeschichtungen lassen sich Wellenschutzhülsen im Abriebbereich der Packungsringe sehr gut härten. Die Härte der Oberfläche sollte dabei größer als 800-1.000 HV (Vickershärte) sein. Diese Maßnahme ist besonders wichtig, wenn die Sauberkeit des Fördermediums nicht zu jeder Zeit gewährleistet ist. Da die harte Beschichtung sehr dünn ist, können so behandelte Wellenhülsen im Servicefall nicht nachgearbeitet werden.
Gleitringdichtung
Im Gegensatz zur Packung weisen Gleitringdichtungen einen Dichtspalt auf, der rechtwinklig zur Wellenachse steht. Wellendichtungen dieser Bauart werden auch als axiale oder hydrodynamische Gleitringdichtungen (GLRD) bezeichnet. Sie benötigt gegenüber der Packungsstopfbuchse einen kleineren Raum und bedarf keiner Wartung.
Die Gleitringdichtung bewährt sich sowohl bei niedrigen als auch bei hohen abzudichtenden Drücken und Umfangsgeschwindigkeiten. Somit besteht kaum eine Möglichkeit der Fehlbedienung.
Erhebliche Nachteile entstehen bei abrasiven Medien durch Verschleiß (siehe Abrasion). Durch saubere Sperr- oder (z. B. mittels Zyklon gereinigte) Spülflüssigkeiten können aber abrasive Teile ebenfalls wie bei den Packungen von den gefährdeten Gleitflächen ferngehalten werden. Im Betrieb gleiten zwei Dichtflächen aufeinander, die durch hydraulische und mechanische Kräfte aufeinandergedrückt werden. Zwischen diesen beiden feinst bearbeiteten Gleitflächen befindet sich der Dichtspalt mit einem meist flüssigen Schmierfilm. Die Spaltweite (Abstand zwischen den beiden Gleitflächen) hängt von verschiedenen Einflussfaktoren ab. Dazu zählen u. a. die Rau- und Ebenheit der beiden Gleitflächen sowie die Gleitgeschwindigkeit. Die sehr geringe Leckage bei der Gleitringdichtung gelangt als Dampf- und Tröpfchenleckage beim Austritt in die Atmosphäre. Für die Berechnung der Dichtungsleckage geht man meist von einer Spaltweite von unter 1 µm aus. Diese äußerst geringe Spaltweite ist auch der Grund, weshalb die Leckage der GLRD wesentlich geringer als bei Wellendichtungen mit Radialspalt ist. Ein wichtiges Kennzeichnungsmerkmal unterscheidet Dichtungen als belastet oder entlastet. Dabei wirkt bei der belasteten Dichtung der abzudichtende Druck in voller Größe auf die Gleitfläche.
Bei der entlasteten Ausführung wird durch einen Absatz an der Welle oder Wellenhülse nur ein Teil des Mediumdruckes als Axialkraft wirksam. Als Belastungsfaktor (k) kennzeichnet und definiert man das Verhältnis von hydraulisch belasteter Fläche (AH) zur Gleitfläche (A). siehe Abb. 7 Wellendichtung
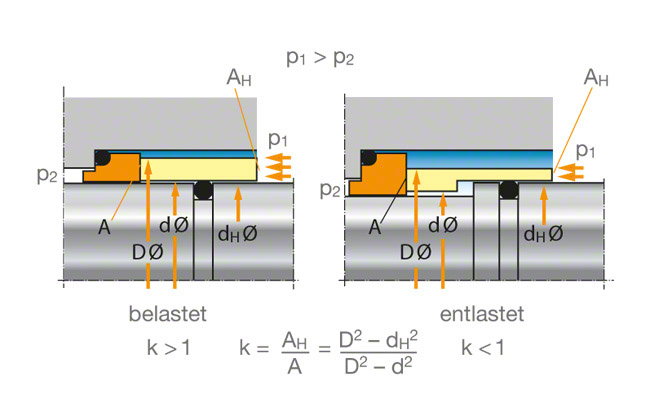
Bei fallendem k-Wert werden die Dichtflächenbelastungen reduziert. Deshalb werden im Hochdruck- und Hochgeschwindigkeitsbereich immer entlastete GLRD eingesetzt.
Ein niedriger k-Wert bewirkt neben einer besseren Schmierfilmausbildung auch eine höhere Leckage. Ein zu geringer k-Wert kann im Extremfall sogar ein Abheben der Gleitflächen bewirken, was mit dem Verlust der Abdichtwirkung einhergeht.
Neben der hydraulischen Schließkraft wirken auch die Federkräfte als zusätzliche Axialkraft auf den Dichtspalt. Die Federn können offen oder gekapselt, mediumsberührt oder trocken angeordnet und mit oder ohne Drehmomentübertragung sein.
Zur Anwendung kommende Federarten
- Zentralfeder, keglig oder zylindrisch gewickelt als Einzelfeder auf die Welle geschoben
- Gruppenfeder, als konzentrisch angeordnetes Federpaket
- Metallfaltenbälge
- Wellfedern
Die erzeugte Reibleistung ist geringer als bei der Packungsstopfbuchse. Je nachdem, wie viel Reibungswärme im Dichtungsgehäuse anfällt, kann diese Verlustleistung entweder über Konvektion vom Dichtungsgehäuse an die Umgebungsluft abgegeben werden oder muss durch Zwangszirkulation über einen extern angeordneten Wärmetauscher abgeführt werden.
Wie auch bei der Packung gibt es bei GLRD eine Vielzahl von Bauformen und Anordnungen, die den unterschiedlichen Betriebsbedingungen entsprechen.
Häufig eingesetzte Bauformen
- Einfach belastete GLRD als typisches Beispiel für eine keglig gewickelte zentrale Einzeldruckfeder: Diese Ausführung zeigt einen ,,dead end"-Einbau, bei dem es keine zusätzliche Produktzirkulation im Bereich der GLRD gibt. siehe Abb. 8 Wellendichtung
- Belastete GLRD werden eingesetzt bis zu abzudichtenden Drücken von max. 15 bar und Gleitgeschwindigkeiten bis max. 15 m/s. Die im Dichtspalt anfallende Reibungswärme kann i. d. R. ausreichend an das Medium übergehen und durch Konvektion vom Dichtungsgehäuse an die umgebende Luft abgegeben werden. Bei kaltem Fördermedium wird die Reibwärme auch vom Medium selbst aufgenommen. Eine Variante ist die Gummibalgdichtung (Balg-GLRD). siehe Abb. 9 Wellendichtung
- Belastete GLRD mit stationär angeordnetem Federpaket: Diese Bauform kommt bei höheren Gleitgeschwindigkeiten zur Anwendung, da aufgrund der Fliehkräfte die Federn sonst die ihnen zugedachte Aufgabe nicht zuverlässig wahrnehmen können (Knickgefahr). siehe Abb. 10 Wellendichtung
Neben dem Unterscheidungsmerkmal bezüglich der Federanordnung gibt es bei der GLRD eine Vielzahl von Ausführungsvarianten für unterschiedliche Betriebsanforderungen.

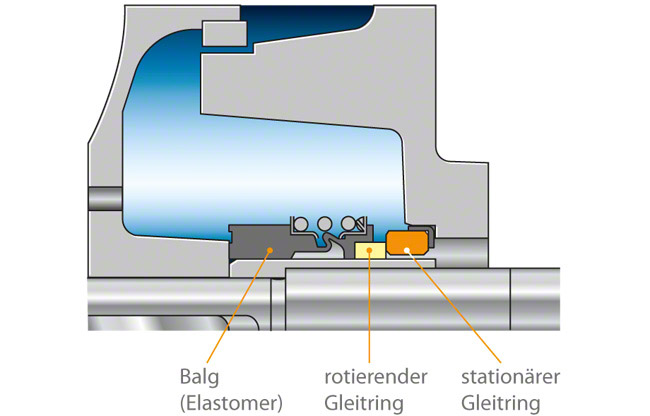
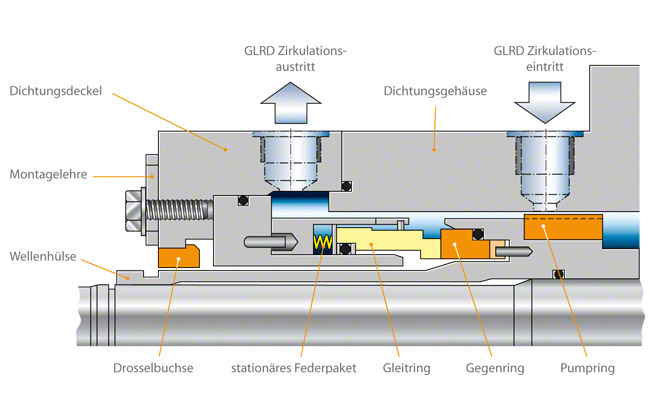
Anordnung von Gleitringdichtungen
- einfach wirkend siehe Abb. 8, 9 und 10 Wellendichtung
- mehrfach wirkend siehe Abb. 11 Wellendichtung
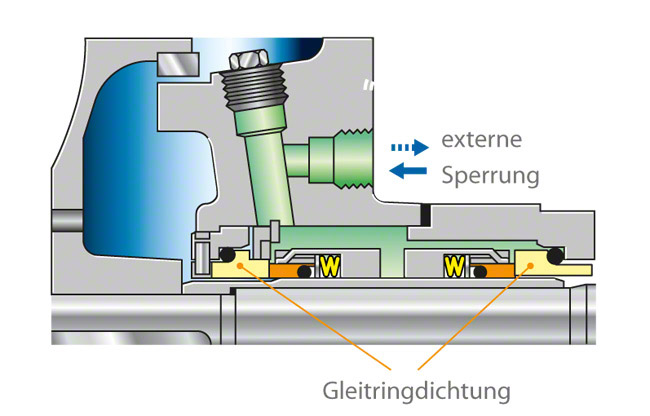
In der "back-to-back"-Ausführung wird in den Raum zwischen den beiden GLRD ein Sperrmedium eingespeist, das im Druck ca. 10 %, mindestens aber 2-3 bar über dem Druckniveau des abzudichtenden Fördermediums der Pumpe liegt. siehe Abb. 11 Wellendichtung
Die Sperrdruckvorlage sorgt dafür, dass keine Produktleckage in die Atmosphäre gelangen kann. Vor deren Einsatz ist aber zu prüfen, ob eine leckagefreie Pumpe wie die Spaltrohrmotor- oder Magnetkupplungspumpe für diesen Einsatzfall nicht besser geeignet ist.
Da die Sperrdruckvorlage die Reibungswärme der beiden GLRD aufnimmt, muss sie als zirkulierende Flüssigkeit auch wieder aus dem Sperrdruckraum abgeführt und rückgekühlt werden.
Den Sperrdruck stellen Sperrdruckaggregate (Thermosiphonbehälter) oder Druckübersetzer sicher. Bei der Tandemdichtung wird der Raum zwischen den Dichtungen von einer drucklosen Quenchflüssigkeit (Quench) durchspült. Neigt die Leckage des Fördermediums bei Luftkontakt z. B. zu Kristallisation, so wird zum Schutz der Dichtung die Ausführung mit zwei Gummibalgdichtungen ausgeführt. Quench und Fördermedium müssen aufeinander abgestimmt sein.
siehe Abb. 12 Wellendichtung
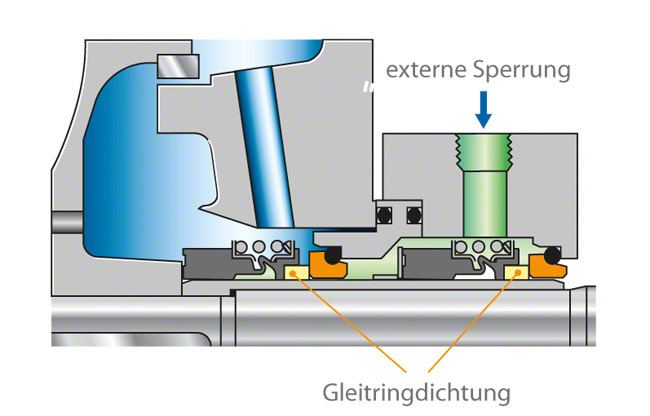
An Stelle der atmosphärenseitigen GLRD kann auch eine einfache Abdichtung wie der Radialdicht- oder Packungsring eingesetzt werden. Sie wird der Hauptdichtung nachgeschaltet, um das Austreten der Leckage (z. B. bei gefährlichen Fluiden) zu unterbinden und Wärme sicher abzuführen.
Tandemdichtungen werden auch zum Aufteilen eines hohen Pumpeninnendrucks auf zwei GLRD eingesetzt. Das Sperrmedium liegt dann im Druckniveau zwischen abzudichtendem Druck und Atmosphärendruck. Die innere Dichtung ist mit der Druckdifferenz zwischen abzudichtendem Druck und Sperrwasserdruck, die äußere zwischen Sperrwasser- und Umgebungsdruck belastet. Das Sperrmedium muss zirkulieren, um die von den Dichtungen erzeugte Reibungswärme abführen zu können. siehe Abb. 13 Wellendichtung
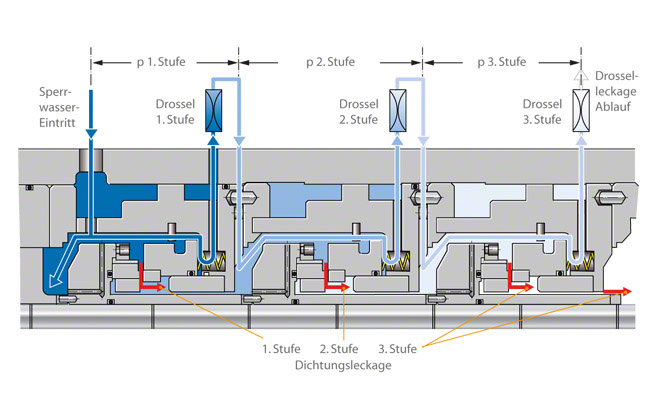
Diese Ausführungen kommen in Kernkraftwerken wie den Siede- und Druckwasserreaktoren in den Hauptkühlmittelpumpen zum Einsatz, wo höchste Drücke abzudichten sind. So werden im Druckwasserreaktor in einer dreistufigen Dichtungsanordnung 160 bar Druck abgedichtet.
Die Druckteilung muss durch eine Hilfseinrichtung erfolgen, bspw. durch eine im Bypass zu den Dichtungen liegende dreistufige Kaskadendrossel. Eine bestimmte Wassermenge fließt dabei über den Bypassstrang. An jeder Drossel wird so der Druck um ca. 33 % verringert. Dieser kleinere Druck ist dann wiederum der Betriebsdruck der nächsten Stufe. Die Drosselleckage sorgt für die Druckteilung und Abfuhr der Reibungswärme aus den Dichtungsstufen.
Bei Kesselspeisepumpen sind große Gleitgeschwindigkeiten, der Wärmeeintrag aus dem Pumpenmedium und die anfallende Reibungswärme zu beherrschen. siehe Abb. 14 Wellendichtung
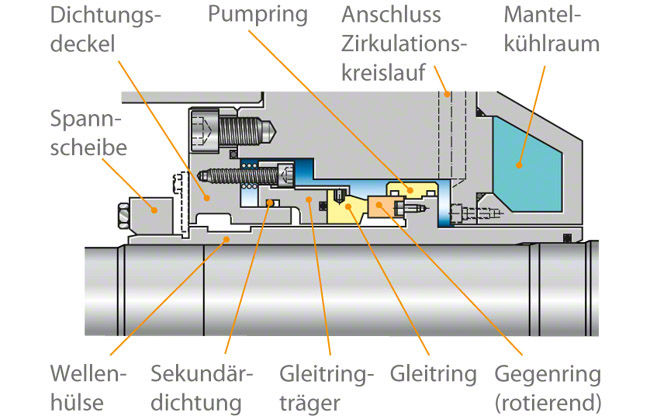
Die Dichtspalttemperatur ist meist höher als die Mediumstemperatur im Dichtungsgehäuse. Letztere kann mittels eines Zirkulationskreislaufes, der durch geeignete pumpeninterne Fördereinrichtungen angetrieben und durch einen externen Kühler gedrückt wird, deutlich unter 100 °C gehalten werden. Als Pumpeinrichtungen dienen Förderschnecken, Bohrungen in der Wellenschutzhülse oder kleine Förderscheiben. siehe Abb. 15 Wellendichtung
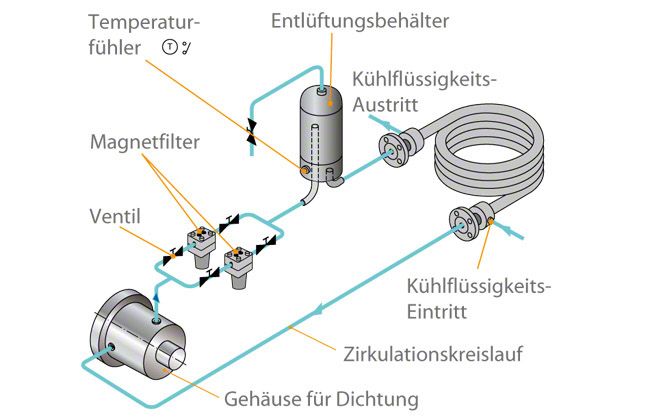
Die installierten Magnetfilter sorgen für größtmögliche Sauberkeit des Zirkulationswassers. Der Entlüftungsbehälter eliminiert bei schnell laufenden Pumpen als wesentliche Komponente die Luftanteile im Zirkulationsmedium zuverlässig. Der für die GLRD schädliche Trockenlauf kann beim Betrieb einer ungefüllten Pumpe, bei starkem Gaseinbruch oder Gasgehalt oder bei Verdampfung des Fördermediums eintreten. Die Gasanteile zentripedieren dabei aufgrund der geringen Dichte immer zu kleinen Durchmessern hin, was bei Dichtungen meist der Dichtspalteintritt ist. Luft an dieser Stelle führt zum Trockenlauf und verhindert auch eine ausreichende Wärmeabfuhr am Dichtspalt, was in kürzester Zeit zu einer thermischen Überlastung der Dichtflächen sowie dem Ausfall der GLRD führt (Wärmespannungsrisse). Auf externe Kühlkreisläufe verzichtet man, wenn die Verlustwärme der Dichtung an die Umgebung durch freie Konvektion und Wärmestrahlung abgeführt werden kann. siehe Abb. 16 Wellendichtung
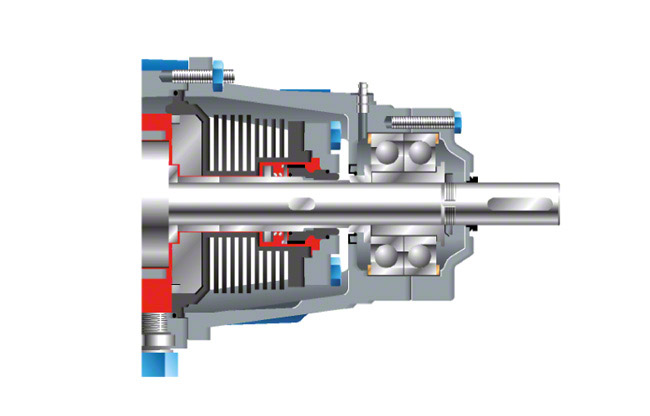
Bei anderen Ausführungen der Kühlung wiederum wird mit einem auf der Pumpenwelle befestigten Ventilatorrad die Konvektion zusätzlich intensiviert (erzwungene Konvektion). Dazu ist in beiden Fällen das Dichtungsgehäuse verrippt ausgeführt. Senkrecht zur Wellenachse (ohne Ventilatorrad) siehe Abb. 16 Wellendichtung, parallel zur Wellenachse (mit Ventilatorrad). siehe Abb. 17 Wellendichtung
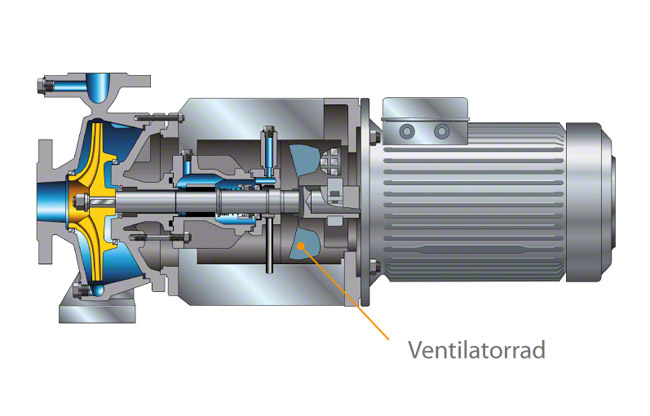
Bei ungekühlten heiß laufenden GLRD liegen die Temperaturen im Dichtspalt generell höher als in allen bisher beschriebenen Fällen. Das bedeutet, dass die Grenze zwischen Flüssigkeit und Dampfphase im Dichtspalt sich zwangsläufig in Richtung Dichtspalteintritt verschiebt. Die Gefahr der Mangelschmierung nimmt dadurch zu.
Nicht berührende Dichtung mit Radialspalt
In diese Kategorie fallen alle Drosselspalten mit oder ohne Labyrinthe, Fördergewinde und die Schwimmringdichtungen ("floating seal"). Die Spaltweite zwischen dem stationären und rotierenden Bauteil wird zur Minimierung der Leckage so eng wie möglich ausgeführt. Es muss sichergestellt sein, dass ein Anstreifen der Teile aneinander ausgeschlossen ist. Bei drehender Welle ist die Leckage etwas geringer als im Stillstand. Das durch den Spalt fließende Medium baut den Druck zum Umgebungsdruck hin ab. Dies erfolgt beim Drosselspalt und der Schwimmringdichtung aufgrund der Flüssigkeitsreibung im Spalt sowie den Strömungsverlusten beim Ein- und Austritt.
Schwimmringdichtung
- Der große Vorteil der Schwimmringdichtung liegt in der Berührungsfreiheit der Bauteile. Demgegenüber steht der erhebliche Aufwand zur Bereitstellung des Sperrkondensates, dessen Aufbereitung und der Regeleinrichtungen.
- Aufgrund der Berührungsfreiheit können diese Dichtungen für hohe Umfangsgeschwindigkeiten und mittlere abzudichtende Drücke (30 bis zu 50 bar) eingesetzt werden. siehe Abb. 18 Wellendichtung
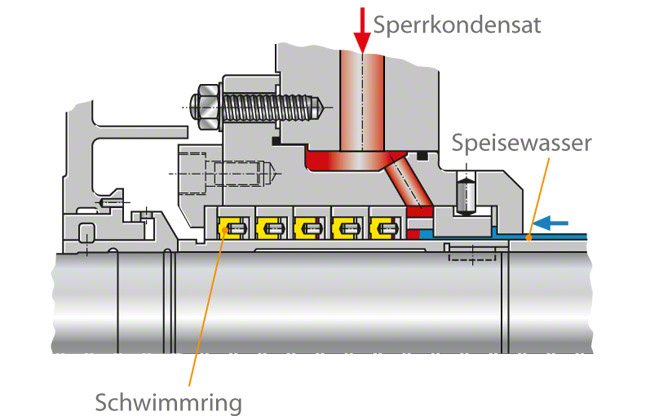
- Hinsichtlich ihrer Zuverlässigkeit ist sie von der chemischen Zusammensetzung des Speisewassers nahezu unabhängig.
- Die Schwimmringdichtung besteht aus mehreren hintereinander geschalteten und radial verschiebbaren, kurzen Drosselringen, die sich aufgrund der Druckverteilung am Ring selbst zentrieren. Ein in die Dichtung eingespritztes kaltes Sperrkondensat sorgt dafür, dass kein Heißwasser aus der Pumpe nach außen austritt (geregeltes System). Solange die Pumpe in Betrieb ist oder unter Druck steht, ist die Sperrwasserversorgung aufrechtzuerhalten.
- Die Schwimmringdichtung wird vereinzelt im Kesselspeisepumpenbereich eingesetzt. Ihre Sperrkondensatmenge lässt sich durch Druck- oder Temperaturdifferenz des Sperrkondensates regeln. siehe Abb. 19 Wellendichtung
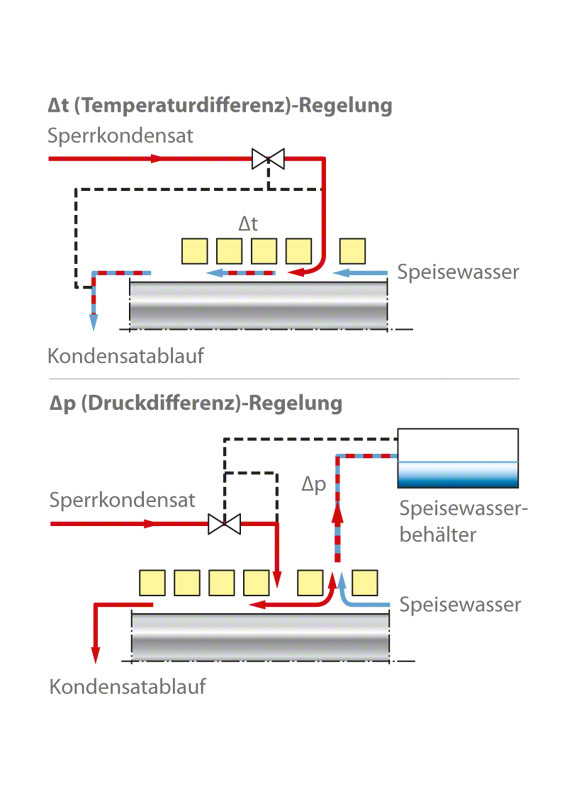
- Bei der Temperaturdifferenzregelung (Δt-Regelung) ist die Differenz zwischen der Temperatur am Sperrkondensatablauf und des Einspritzkondensates vorgegeben. Bei der Kesselspeisepumpe tritt nur ein sehr geringer Speisewasserstrom aus dem Pumpeninneren ein. Hierbei kann das Eindringen von Kaltwasser in das Pumpeninnere ausgeschlossen werden.
- Bei der Druckdifferenzregelung (Δp-Regelung) ist die Differenz zwischen Einspritz- und Zulaufdruck vorgegeben. Es tritt ein geringer Sperrkondensatstrom in die Pumpe ein. Dadurch müssen hohe Ansprüche an Reinheit und Gasfreiheit des Sperrkondensates gestellt werden, um den Hauptkreislauf nicht zu verunreinigen.
Anstelle der Schwimmringdichtung kann aber auch eine Labyrinthdichtung vorgesehen werden.
Labyrinthdichtung
- Die Labyrinthdichtung ist eine feste Drosselbuchse mit ringnutartiger Profilierung. Infolge der fehlenden radialen Verschiebbarkeit muss das Durchmesserspiel größer ausgeführt werden als bei der Schwimmringdichtung. Dies hat eine größere Leckage zur Folge, wodurch auch ein entsprechend größerer Sperrwasserstrom erforderlich wird.
Zentrifugaldichtung
- Eine der Dichtungsdruckdifferenz entgegenwirkende, selbst druckerzeugende Wellendichtung ist die Zentrifugaldichtung mit häufig nachgeschalteter Stillstandsdichtung. Als federbelastete Gleitringdichtung (GLRD) ausgeführt, wird sie schon bei niedrigsten Drehzahlen durch Fliehkräfte geöffnet und damit vor Verschleiß geschützt. siehe Abb. 20 Wellendichtung
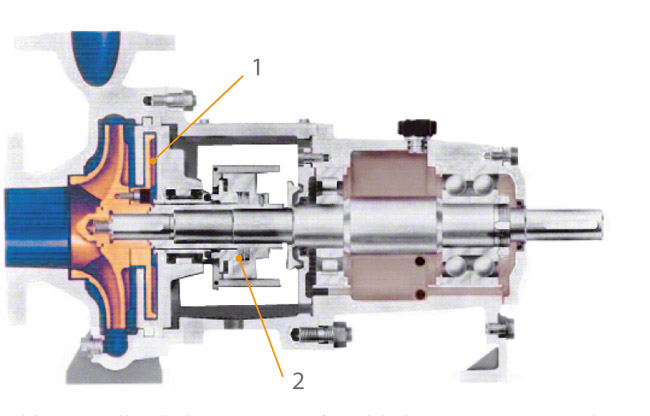
- Die eigentliche Zentrifugaldichtung (als Hilfslaufrad mit Flüssigkeitsring am Außendurchmesser) arbeitet berührungs- und verschleißfrei.
Fördergewinde
- Auch Fördergewinde können bei optimaler Gestaltung (Gewindesteigung des stationären Teils ist gegen die Steigung des rotierenden Teils gerichtet) und laufender Pumpe einen Gegendruck erzeugen, der gegebenenfalls das Gleichgewicht gegen den Innendruck der Pumpe hält. Die so erreichbaren Nullpunktdrücke sind abhängig von der Drehzahl, Gewindelänge, Spaltweite und dem mittleren Spaltdurchmesser.
- Förderhöhen von 10 bis zu 30 m sind dabei realistisch.
- Sobald die Welle jedoch stillsteht, hat das Fördergewinde nur noch eine Drosselwirkung. Diese ist mit einem Labyrinthspalt vergleichbar.
- Soll ein Fördergewinde als Pumpendichtung eingesetzt werden, muss in jedem Fall eine berührende Dichtung als Stillstandsdichtung nachgeschaltet werden. siehe Abb. 21 Wellendichtung
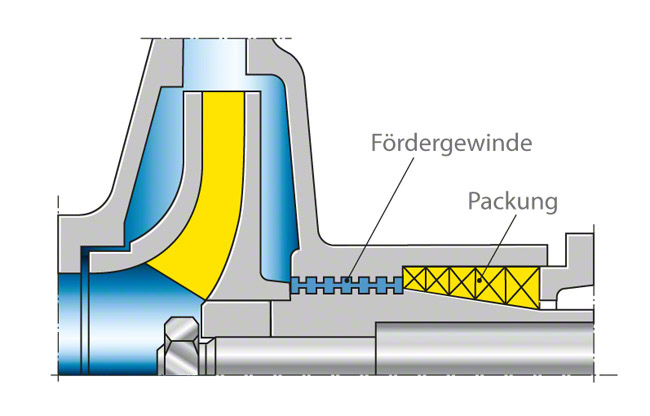
Hydrostatische Dichtung
- Die hydrostatische Dichtung (HSD) ist als berührungsfreie Wellendichtung aufgrund ihres Kon-struktionsprinzips für eine einwandfreie Funktion erst bei Drücken größer als 20 bar berührungsfrei. Der Pumpenantrieb darf somit erst oberhalb dieser Schwelle gestartet werden.
- Da die Dichtung sehr empfindlich gegen Feststoffe ist, muss das Sperrwasser, über das die Dichtung gespeist wird, extrem sauber sein.
- Der Dichtspalt ist dabei selbstregelnd und abhängig von der Dichtspaltgeometrie und dem abzudichtenden Druck, wobei sich die Spaltweite bei etwa 10 µm einstellt.
- Die Spaltsteifigkeit ist bei vollem Betriebsdruck (160 bar) sehr groß. Um den Spalt um 1 µm aus seiner Gleichgewichtslage zu verschieben, müsste eine externe Kraft von ca. 4.000 N einwirken.
- Da die Dichtung mit einem endlichen, wenn auch sehr engen Spalt arbeitet, hat sie erhebliche Leckage (p = 160 bar, n = 1.500 min-1; Abdichtdurchmesser bei 260 mm, Q = 800 l/h). Aufgrund dessen muss dieser Dichtung eine Niederdruckdichtung nachgeschaltet werden, welche die Leckage der HSD gegen die Atmosphäre abdichtet. siehe Abb. 22 Wellendichtung
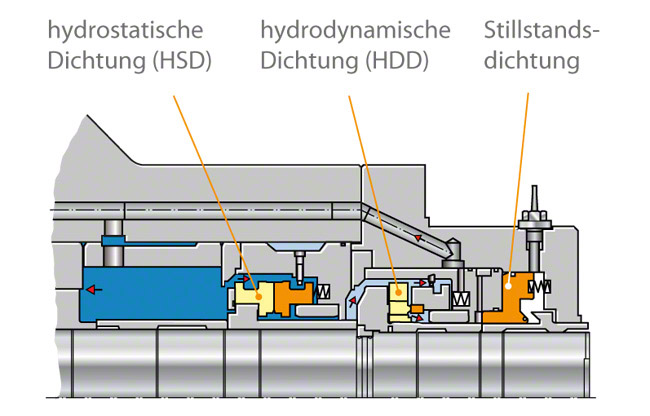
- Als Folge dieser Betriebseinschränkung bei Niederdruck erfolgte der Austausch der hydrostatischen Wellendichtungen in vielen Kernkraftwerken durch hydrodynamische GLRD.
- Anwendung findet sie ausschließlich in Hauptkühlmittelpumpen von Druckwasserreaktoren.
Statische Berührungsdichtung
Zu den statischen Berührungsdichtungen gehören die Runddichtringe (RDR) (auch O-Ringe genannt). Sie sind Formdichtungen und definiert als "Ringe mit Kreisquerschnitt aus elastischen Werkstoffen, die durch eine geringe Verspannung beim Einbau, unterstützt durch den Betriebsdruck, abdichten". Der symmetrische Querschnitt schließt dabei einen falschen Einbau aus.
Die einfache Berechnung und Gestaltung der Anschlussteile hat zu weiter Verbreitung geführt.
O-Ringe kommen bei allen beschriebenen Wellendichtungen vor. Als Dichtelement können sie nur als statische Abdichtung eingesetzt werden oder an Abdichtstellen, bei denen gelegentlich eine geringe axiale Bewegung erforderlich ist. Sie werden in verschiedenen Härtegraden hergestellt. Die Härte wird angegeben in Shore-Härte (A oder D). Diese Härteskala umfasst den Bereich von 0 bis zu 100 Härteeinheiten, wobei 0 der kleinsten und 100 der größten Härte entspricht.
Für Gleitringdichtungen (GLRD) werden für die O-Ringe meist Elastomere mit Shore-A Härten zwischen 70 und 90 ausgewählt. Diese werden als Abdichtungen zwischen Wellenhülsen und Welle sowie als Dichtung zwischen Gleit- oder Gegenring und den Gehäuseanschlussteilen eingesetzt. So stellen sie sicher, dass bei kleinen axialen Bewegungen der Welle das befederte Dichtungsteil entsprechend nachsetzen kann.
Sie werden in ihrer Bedeutung oft unterschätzt, denn jede Wellenabdichtung ist nur so gut wie der O-Ring. Die Runddichtringe müssen auf das Fördermedium abgestimmt sein, den Temperaturbereich abdecken und alterungsbeständig sein. Darüber hinaus muss ein hochwertiges O-Ring-Fett verwendet werden, das den betriebsbedingten Anforderungen gerecht wird. Zum einen ist die Langzeitschmierwirkung zu beachten, zum andern darf sich das Schmiermittel nicht nachteilig auf das Fördermedium auswirken und der O-Ring nicht vom Schmiermittel angegriffen werden.
Elastomere, die im Betriebsmedium weniger als 10 % quellen und mit dem Medium chemisch nicht reagieren, sind als Nebendichtung für eine GLRD geeignet. Dafür gibt es einige Elastomer-Sorten, die jeweils Unterschiede von Temperaturbeständigkeit und Quellverhalten in Referenzöl aufweisen. siehe Abb. 23 Wellendichtung
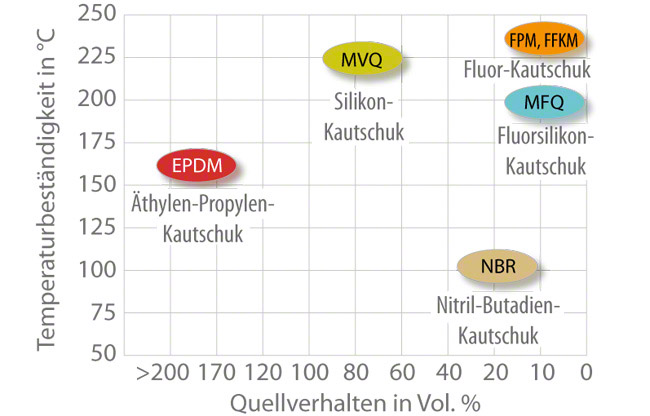
Besonders kritisch sind Anwendungen in Chemie- und Raffineriebetrieben, in denen Pumpen häufig mit verschiedenen Fördermedien beschickt werden.