Eductor-jet pumps are used if the water level on the suction side is too low for the suction lift operation of a normal pump. They transport fluids with relatively small flow rates of up to approximately 10 m3/h from narrow deep wells where the water level is up to 40 m below ground level (especially in the USA).
The advantage of this arrangement is that there are no moving components located in the deep well, so that no restrictions govern the installation of the centrifugal pump. The disadvantage is that the pump set has a lower overall efficiency than a borehole pump or submersible borehole pump.
In an eductor-jet pump arrangement, a partial flow referred to as motive flow (QMo) is branched off from the total volume flow in the discharge line of an ordinary centrifugal pump installed above floor. The motive flow is recirculated to the eductor which is installed approximately 1 m beneath the lowest water level (see Water jet pump).
See Fig. 1 Eductor-jet pump
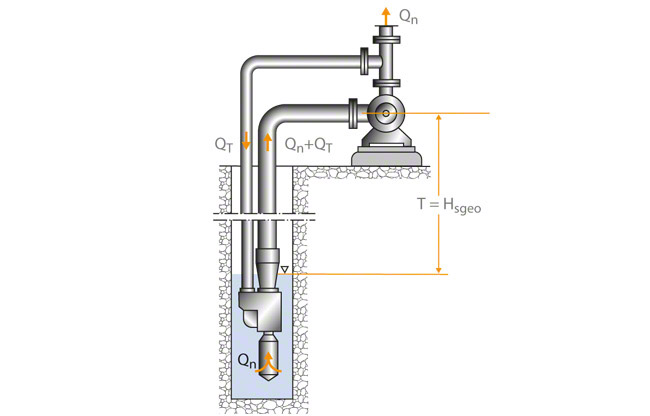
The eductor draws in the primary flow (QPr) and transports the total mixed fluid (QPr + QMo) to the pump suction nozzle. See Fig. 2 Eductor-jet pump
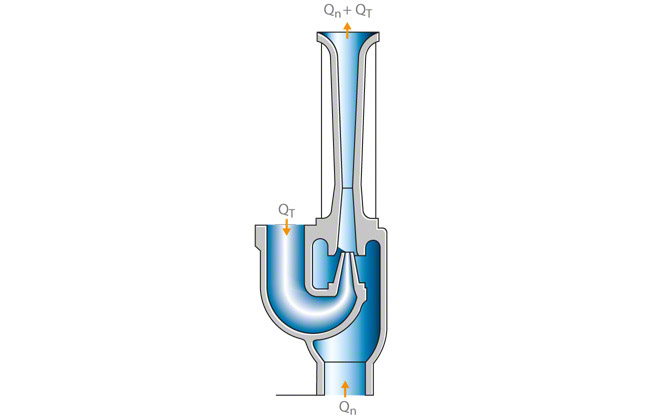
Once the fluid has passed through the pump, the same quantity of motive flow (QMo) is branched off again for recirculation. The primary flow (QPr) is supplied to the consumer installation.
The following equation applies:
HEff = WL + HLRiser - HS = WL + (HTotal + HMo) - HS
HTotal Total head
HEff Effective head of the eductor
HS Permissible suction lift of the pump
HMo Motive head
HLRiser Head loss in the riser pipe
HLMo Head loss in the motive pipe
WL Distance between water level and pump centreline
(Also see the numerical example below.)
If approximate values are known for the distance between water level and pump centreline (WL) and the total head (HTotal), the effective head (HEff) and motive head (HMo) can be roughly determined. Then, the ratio of motive head and effective head (HMo/HEff) can be calculated. The corresponding ratio of motive flow to primary flow (QMo /QPr) can be obtained from the calculation diagram for eductor-jet pumps.
As the primary flow (QPr) is also given, both the motive flow (QT) and the approximate design data of the centrifugal pump can be calculated.
See Fig. 3 Eductor-jet pump
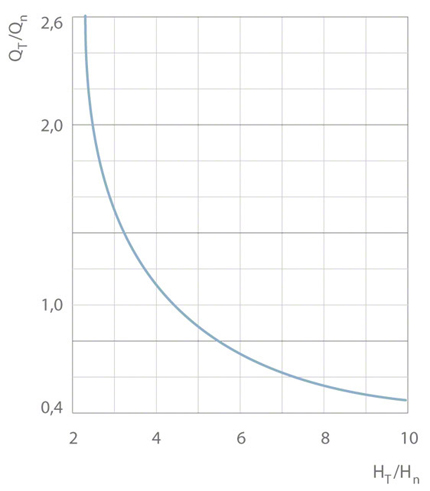
When all data is known, a suitable pump type can be selected and the nominal diameter of the motive pipe and riser pipe can be determined. The data can then be used to calculate the values for the permissible suction lift (HS) as well as the head losses in the riser pipe (HLRiser) and motive pipe HLMo (see Pressure loss). The calculation can be repeated with more accurate values.
Numerical example
- Given:
HTotal = 80 m
HLRiser = 4 m
HS = 8 m
QPr = 5 m3/h
T = 20 m - Follows:
HEff = WL + HLRiser – HS = (20 + 4 – 8) m = 16 m
HMo = HTotal – HLRiser = (80 – 4) m = 76 m
HMo / HEff = 76/16 = 4.75 - Obtained from the diagram:
See Fig. 3 Eductor-jet pump
QMo / QPr = 0.95 - Thus the flow rate of the motive fluid QMo of the eductor and the flow rate Q of the centrifugal pump equal:
QMo = (QMo/QPr) · QPr = 0.95 · 5 m3/h = 4.75 m3/h
Q = QPr + QMo = (5.0 + 4.75) m3/h
Q = 9.75 m3/h
The head (H) of the centrifugal pump equals:
H = HTotal – HEff = (80 – 16) m
H = 64 m
The above values can be used to calculate the inside diameters and head losses of riser pipe and motive pipe. Then, the calculation can be repeated more accurately. In most cases the approximate calculation will be adequate.
For common eductor values the relationship of QMo / QPr and HMo / HEff is plotted in a curve. The exact curve depends on the type of eductor used. See Fig. 3 Eductor-jet pump
When planning to use a centrifugal pump in conjunction with an eductor-jet pump calculating the economic efficiency in detail is recommended, as eductors or water jet pumps have a relatively low efficiency compared with other suitable centrifugal pump types such as compared with other suitable centrifugal pump types such as borehole pumps, submersible motor pumps and submersible borehole pumps.