Internal efficiency
In accordance with DIN EN 12723:2000 the internal efficiency (ηi) of a centrifugal pump is the ratio between pump power output (PQ) and the pump input power (P) minus mechanical losses (PL.m).
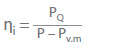
If the pump power output (PQ) is replaced by (P − PL.i − PL.m), then the following equation applies: See Fig. 1 Head

The mechanical power losses mainly comprise the friction losses of pump bearings (e.g. plain bearings and rolling element bearings). The following relationship exists between the internal efficiency (ηi), pump efficiency (η) and the mechanical efficiency (ηm).
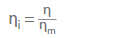
Efficiency scale-ups usually relate to internal efficiencies. These can also be determined on the basis of an analysis of the internal losses (PL.i) of the centrifugal pump (see Head).
The power loss (PL.i) comprises:
- Losses incurred on the flow path of the fluid through the impeller, diffuser and pump casing i.e. internal fluid friction, wall friction, momentum exchange losses and shock losses
- Losses incurred as a result of the operation of balancing devices such as balance discs, , balance drums and balancing holes and back vanes
- Losses incurred as a result of disc friction, friction at the throttling rings and cylindrical surfaces at the impeller outlet
- Losses caused by internal circulation flows, in particular the secondary flows from the impeller discharge side through the clearance gap to the impeller suction side, or from the vane pressure side to the vane suction side through the impeller gap (see Clearance gap loss) and reverse flows resulting from flow separation and low flow operation
All internal losses cause the fluid handled to heat up, resulting in a temperature difference (ΔT). The heat radiation through the pump casing can be ignored in this context.
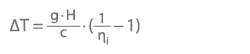
g Acceleration due to gravity in m/s²
H Head in m
c Specific heat capacity in J ∙ (kg · K)-1
ΔT Temperature difference in K or °C
If the fluid is transported through the pump several times in succession as is the case in test facility circuits (see Pump test facility) the useful power output converted into heat in the circuit (e.g. in the throttling element or in the piping) is added to the heat developed inside the pump from one cycle to the next, meaning that cooling may be required.