Gas separation describes the process of gas separating from the fluid handled due to changes in pressure.
The solubility of air in water depends on the water's temperature and pressure (see Gas content of fluid handled). As solubility decreases in line with decreasing pressure and increasing temperature, air comes out of solution in the pumps' suction lines or in siphoning lines (see siphoning lines (see Formation of air pockets). See Fig. 1 Gas separation
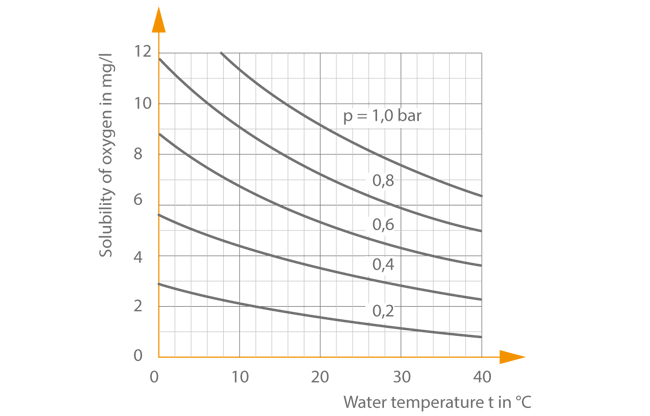
The gases which have come out of solution accumulate at the apex of the line and have to be removed to prevent separation of the water column.
Relative to the suction conditions, the average volume (QSL) removed per hour in the case of suction lines is:
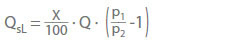
X Volume percent of air dissolved in water at the absolute pressure of 1 bar
Q Flow rate of pump or in siphoning line in m3/h
p1 Absolute water pressure in bar at the beginning of the evacuation process.
p2 Absolute water pressure in bar at the end of the evacuation process
(for pumps operating on suction lift, the absolute suction pressure at flow rate (Q)
should be entered in the equation)
The following applies to siphoning lines: See Fig. 1 Siphoning line

e Height difference of both water levels in m
es Height difference between apex and inlet side water level in m
v Flow velocity in m/s
Σζ Sum of resistance coefficients (see Pressure loss)
pb Atmospheric pressure in bar
If the apex lies close to the collecting tank, the following equation applies:

The volume of gas which comes out of solution is removed by an automatic evacuation system (see Venting). Gassy liquids such as waste water and sewage also liberate gas in the low pressure zones of the impeller which impairs the pumping performance.
Open impellers with large clearance gap widths or free-flow impellers (see Torque flow pump) have achieved the best results in separating and removing the gas from the pump casing.
Applications in the food, paper and pulp industries require gas to be pumped alongside the fluid handled. A pump should therefore be designed in such a way that gas separation and fluid transport can take place simultaneously. See Fig. 2 Gas separation
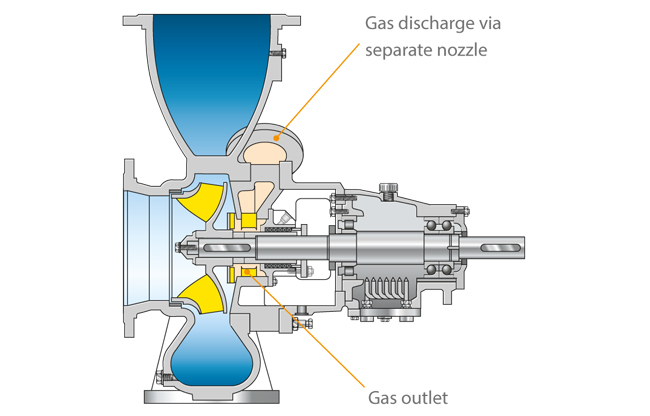
The pump is provided with a device which separates the gas collected at the impeller inlet and presses it to the impeller outlet. From there it is discharged via a separate pipe. This device enables the efficient pumping of fluids with a gas content of up to 60 %. See Fig. 3 Gas separation
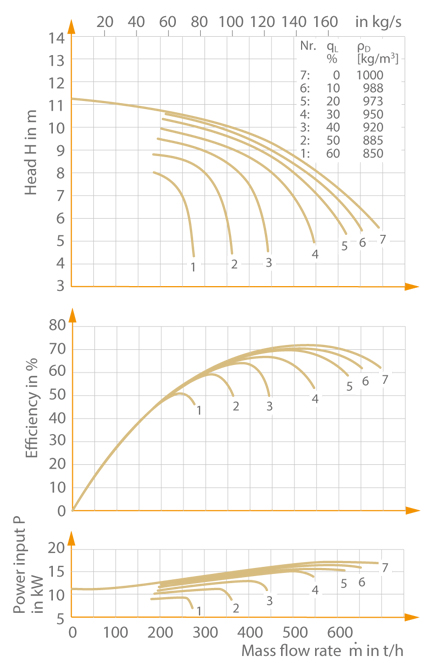