The term NPSH is the abbreviation of "net positive suction head" and is an important factor in evaluating the suction characteristics of a centrifugal pump. It allows a prediction to be made regarding the safety margin required to avoid the effects of cavitation during operation.
In the DIN EN ISO 17769-1 standard the German term "Haltedruckhöhe (retaining pressure head)" is used as a synonym for NPSH. As different reference levels are defined for the two terms, their numerical value can differ by zs (difference in geodetic head between reference levels s and s'). In practice, only the NPSH value is used.
As the fluid flows through the centrifugal pump's impeller the static pressure relative to the pressure upstream of the impeller – will drop, especially at the inlet to the vane passage. The extent of the pressure drop depends on the rotational speed, the fluid density, and viscosity, the impeller’s inlet geometry, the operating point and the velocity profile of the approach flow.
In order to avoid cavitation or to limit it to an acceptable level, the pressure upstream of the impeller must exceed the vapour pressure level of the fluid handled by a specified minimum margin. Assessing the likelihood of occurrence, extent and impact of cavitation in a centrifugal pump requires comparison of two NPSH values: the NPSH required by the pump NPSHR and the NPSH available in the system, NPSHA.
The system's NPSH, i.e. NPSH available (NPSHA) is defined as
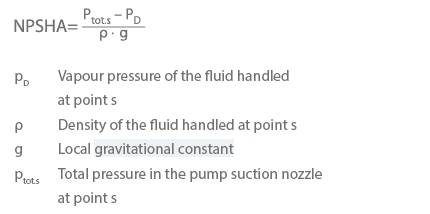
Point s refers to the suction nozzle's centre. If the pump's design does not feature a suction nozzle as is the case with in-line pumps with welded-in pipes (i.e. welded-in pumps) or submersible pumps with bellmouths, a location s which corresponds to the point s in the suction nozzle's centre must be defined and clearly specified when specifying the NPSHA value. See Fig. 1 NPSH
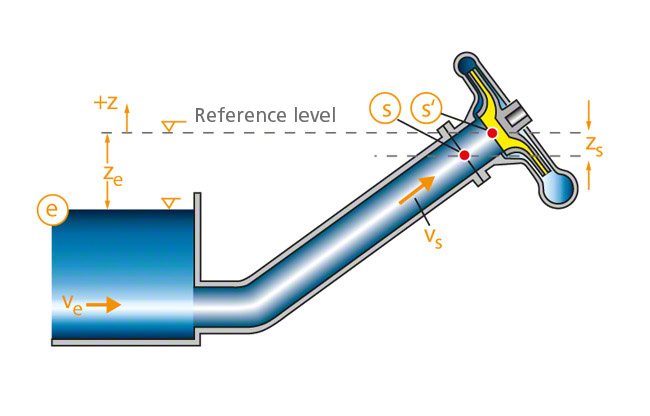
The total pressure at point s can be expressed as:
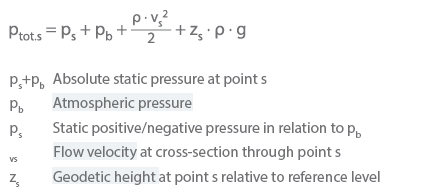
The reference point s' for the NPSH value is the impeller’s centre, i.e. the intersection of the pump shaft axis and a plane situated at right angles to the pump shaft passing through the outer points of the vane leading edge. See Fig. 2 NPSH
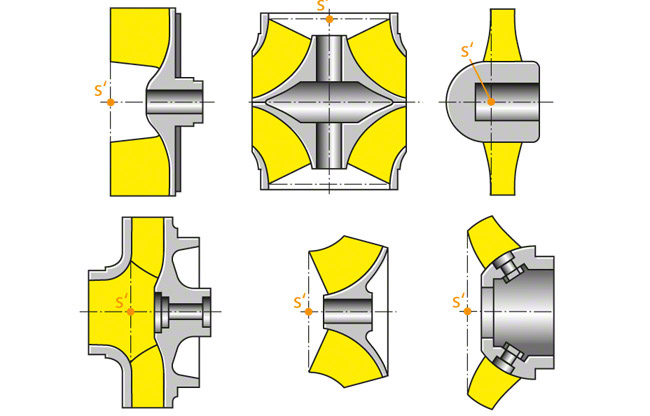
The system's NPSH is thus established as follows:

Inserting the values at the system's inlet cross-section gives:
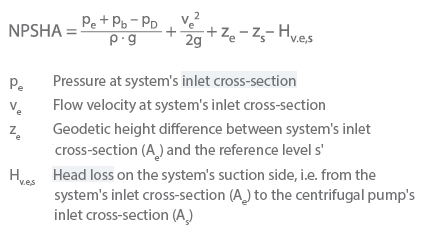
The head loss also includes any entry losses and pressure drops across valves and fittings etc.
NPSH required by the pump (NPSHR)
The definition of the NPSH required by the pump (NPSHR) is similar to that of the system's NPSH, i.e. the symbols in brackets have the same meaning:
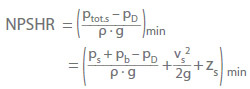
However, a significant difference is that the sum of the parameters defined by the terms in the brackets must not fall below a minimum value (min) specified for a given pump and application.
If this condition is not met, the occurrence of cavitation cannot be ruled out.
When specifying the NPSHR, it is also necessary to provide information on the relevant cavitation criterion. Criteria include:
- Incipient cavitation, NPSHi
- A certainextent of the cavitation zone on the vanes
- Start of head drop as a result of cavitation (NPSH0)
- Cavitation-induced head drop by 3 % (NPSH3)
The first three criteria are less common, and providing evidence for NPSHi requires demanding and expensive testing. For this reason, it is commonly agreed that NPSHR = NPSH3.
The cavitation criteria listed above and their related NPSH values are dependent on the operating point. See Fig. 3 NPSH
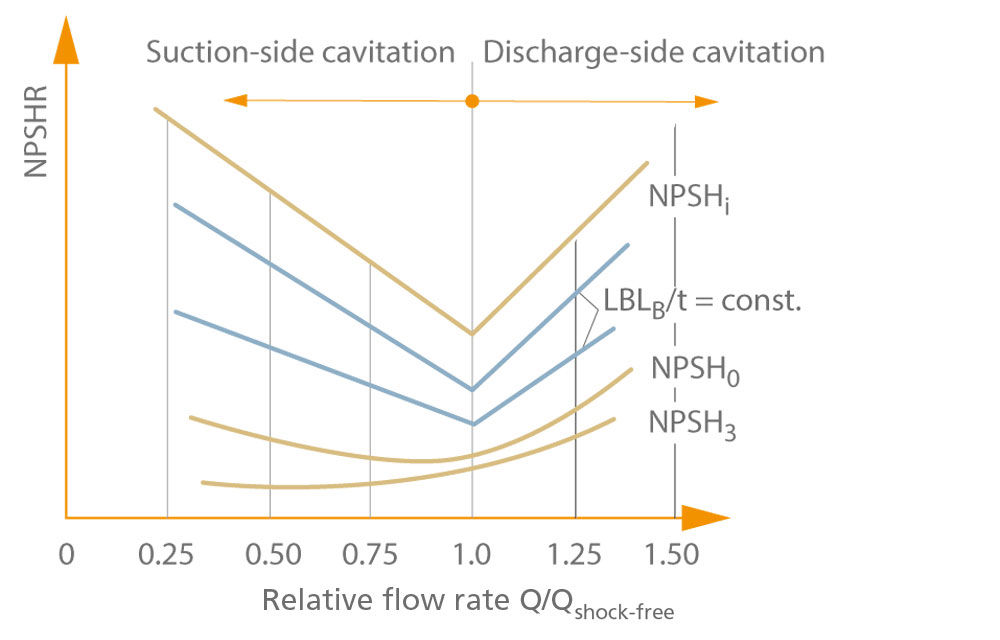
The illustration shows the curves for NPSHR of a specific impeller as a function of the relative flow rate The parameters shown are the cavitation phenomena, e.g. the length (Lcav) of the resulting bubble trail (cavitation zone) in relation to the vane spacing or pitch (t) (see Vane cascade).
If the NPSHA curve is also displayed in the diagram, it is possible to determine the type of cavitation to be expected as a function of flow rate.
The upper curve (NPSHi) indicates incipient cavitation. If NPSHA is higher than NPSHi, cavitation will not develop and the impeller will rotate without the formation of bubbles. The lower the NPSHA value drops, the longer the bubble trail (cavitation zone) will become.
From a minimum level represented in the graph as the intersection of the lines denoting suction-side and discharge-side cavitation, the bubble trail length will increase under low-flow/overload conditions at a constant NPSHA. The flow rate at this minimum level corresponds to the flow direction of shock-free entry which causes the lowest increases in fluid velocity on the pressure side and suction side of the vane. It is therefore referred to as the shock-free flow rate (Qshock-free).
If the flow rate (Q) is lower than the shock-free flow rate (Qshock-free), then cavitation will develop on the vane's suction side; if the flow rate is higher than the shock-free flow rate, then cavitation will develop on the vane's pressure side.
Establishing NPSHR is largely a matter of testing, in particular when:
- Converting the NPSH of the pump from one rotational speed to another
- On similar pumps, converting NPSH from one pump size to another
- Converting NPSH from one fluid to another (in particular if the fluid contains dissolved or undissolved gas) (see Gas content of fluid handled)
A centrifugal pump's operating point can only be operated at continuously if:
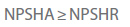
The following relationship exists between the NPSH value and the German concept of "Haltedruckhöhe” (retaining pressure head) which is no longer used:
Retaining pressure head of the system
HHA = NPSHA – zs
Retaining pressure head of the pump
HP = NPSHR – zs
In the case of horizontal pumps, there is no difference in height (zs = 0) between the reference points for NSPH and "retaining pressure head", making the two terms identical. The following coefficients are sometimes used in connection with the NPSH value:
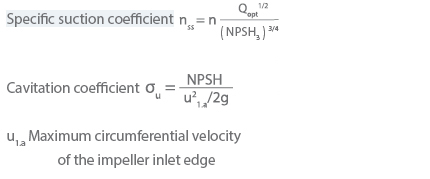
When hydrocarbons or high-temperature water are handled, the NPSH3 value measured is lower than that measured for cold water. This means that the required NPSH value for hydrocarbons or hot water can actually be reduced when performing acceptance tests with cold water:
- Hydrocarbons in accordance with HI
(standards laid down by the Hydraulic Institute, New York) - Hot water See Fig. 4 NPSH
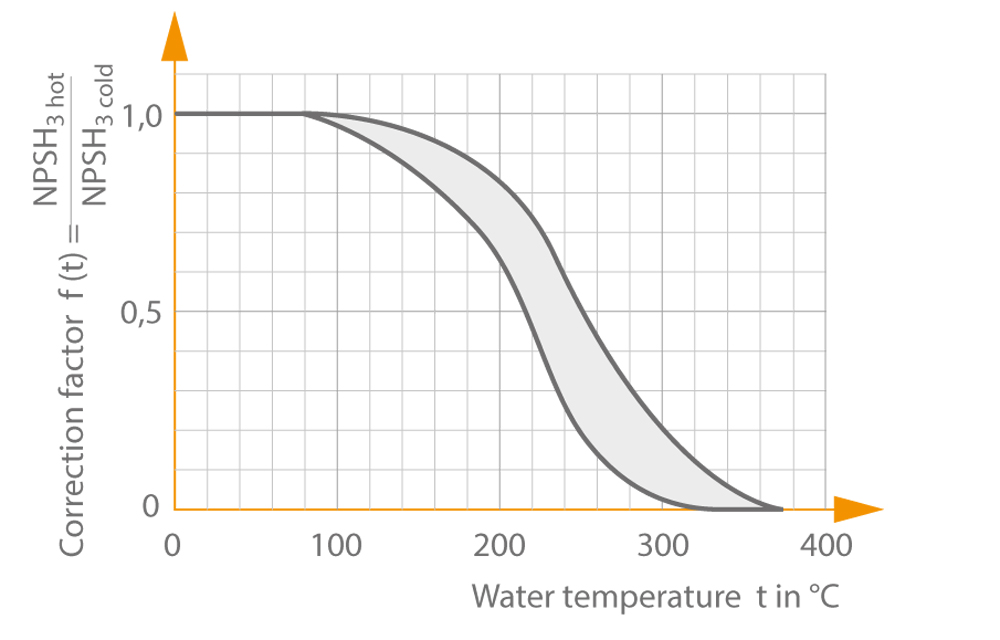