Life cycle costs (also see LCC) are the total costs incurred throughout the service life of a pump system. They are used to compare the economic efficiency of various technical designs. The LCC equation is determined in accordance with the guidelines of EUROPUMP and the Hydraulic Institute.
The life cycle costs associated with the operation of a pump or pump system are determined by calculating the annual costs of operation plus the interest and depreciation for the non-current assets, like the machinery and buildings, for a variety of alternatives.

In the case of centrifugal pumps, energy (Ce), operating (Co) and maintenance costs (Cm) account for the largest proportion of the life cycle costs.
See Fig. 1 Life cycle costs
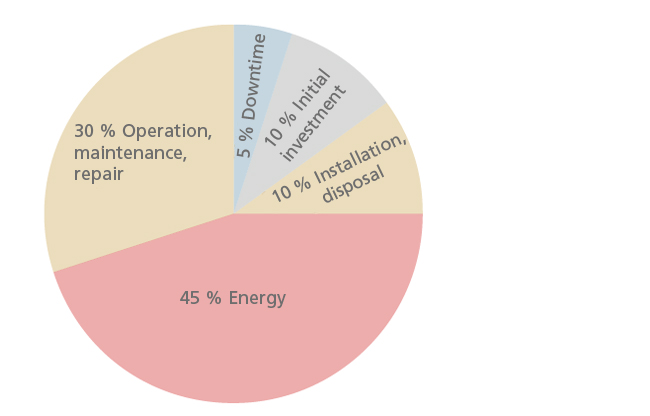
The energy costs are calculated as follows:
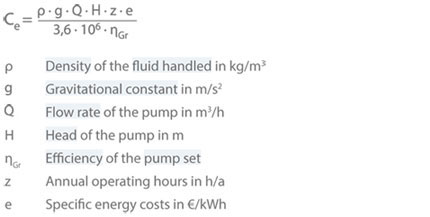
The calculation applies to one specific operating point only. Given that pump operation usually involves a broad flow rate range, a pro rata calculation must be performed for the various flow rates involved. The individual results are then added together, taking the load profile into account.
The costs of operation and maintenance must be determined on a case-by-case basis and are dependent on the level of automation, operating period and maintenance requirement of the system.
LCC analysis − Key financial factors
- Energy price increase (inflation)
- Interest and discount rate
- Expected system life (calculation period)
Calculating the current costs associated with a specific cost element:
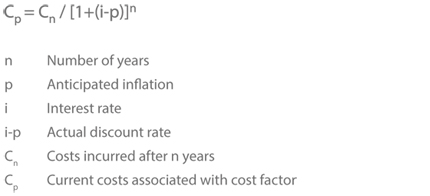
Based on empirical evidence, the following factors can be derived for dimensioning an economically efficient pump system or piping:
See Fig. 2 Life cycle costs
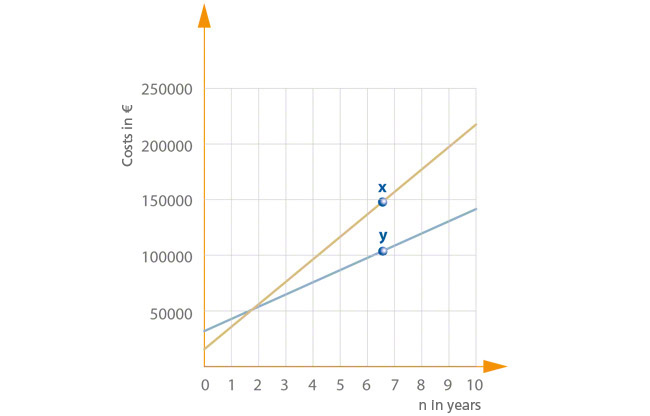
- Having high flow velocities in narrow piping reduces the cost of the system, but increases energy requirements and wear.
- If operating periods are long, the energy costs are the dominant factor. This means that any extra costs for energy-saving measures such as speed adjustment (see Closed-loop control) pay off very quickly.
- If operating periods are short, investments should be low and flow velocities can be high.
- A smaller number of fairly large pumps often produces higher levels of efficiency, resulting in lower energy costs. However, as the number of redundant pumps increases so does the capital expenditure.