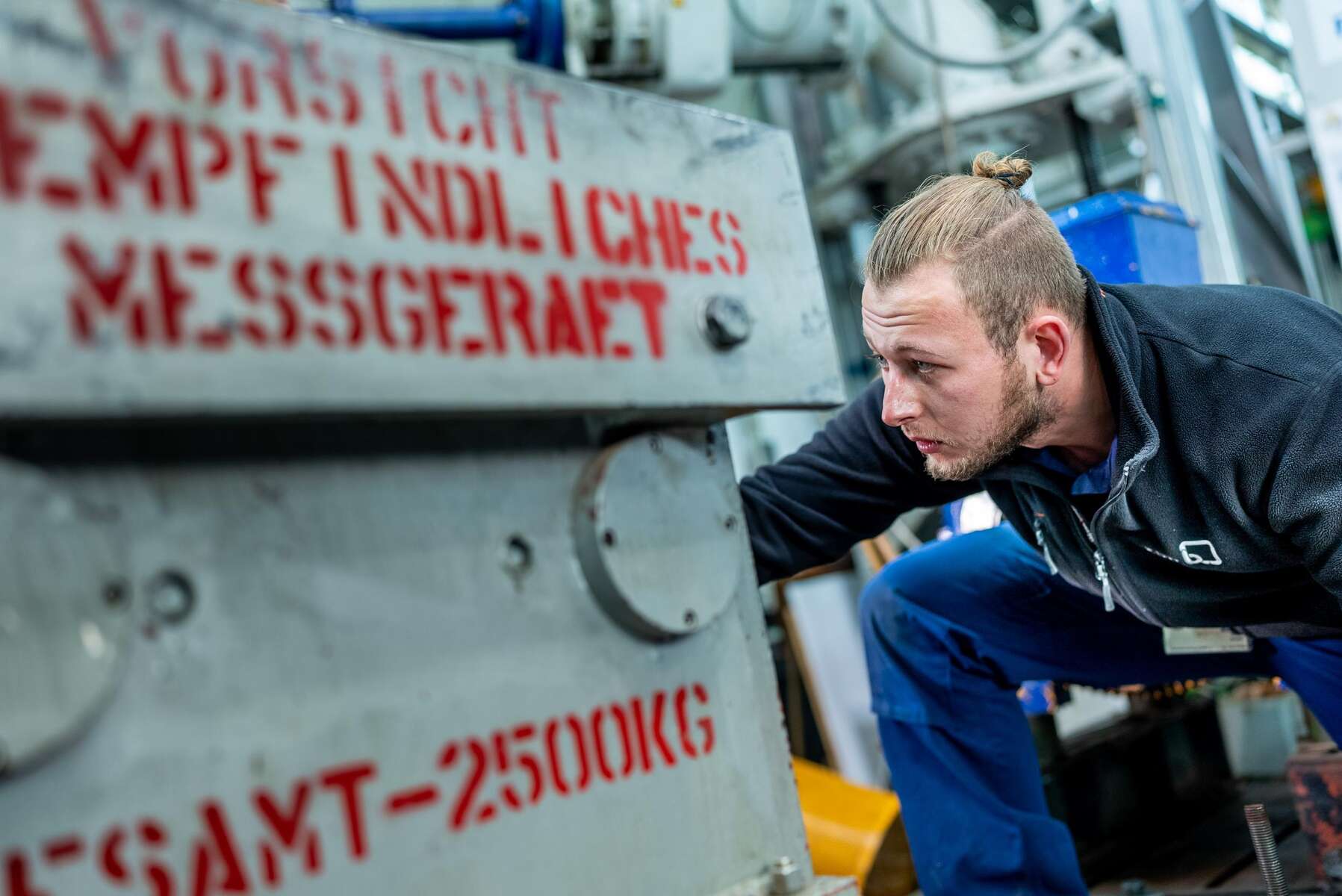
Put to the test
Test facilities ensure worldwide KSB quality
A technical solution’s quality can only be demonstrated by pushing it to its limits. KSB therefore puts all products through their paces via challenging test scenarios before launching them to market and shipping them to customers. With customers around the globe placing their trust in KSB’s reliable quality, the company ensures that testing is carried out to the same high standards at all test facilities worldwide. Some 28,000 pump tests are carried out every year at 50 test facilities KSB-wide.
2. Brazil: South America’s most versatile test stand
KSB’s Brazilian factory in Várzea Paulista is home to one of the largest and most versatile testing facilities in Latin America. It features nine test stands which can be configured to test almost every type of KSB pump as well as pumps repaired by our KSB SupremeServ. A further test stand for submersible motor pumps is located at the Jundiaí plant.
"The department responsible for test stands plays a fundamental role in the company, as it can guarantee the quality and functionality of KSB products and thus provide added value for our customers. Services in the field of testing are increasingly requested and purchased by our customers. Key account customers see performance testing as an important and essential requirement,” explains Thiago Munhoz, an employee at the test facility in Várzea Paulista. "During the pandemic, our department faced major challenges. A lot of testing normally done in person with the customer had to be performed via video conferencing during this period," he continues.
4. Germany: competence centre for test facility technology
In Germany, KSB's largest test facility for dry-installed water transport pumps is situated at our Halle location, and the largest test facility for boiler feed pumps is located in Frankenthal. Both of these test facilities offer variable-speed tests with and without the customer’s motor and with all necessary auxiliary units.
Frankenthal is also home to the Testing Engineering department's central test facility with more than 60 test stands able to test products from all production locations. "Throughout KSB, we have the unique ability to implement time-intensive and application-specific tests such as hot water and hot oil tests, or low-temperature tests down to minus 20 °C," explains Andreas Karsch, Head of Testing Engineering.
“We want to get the most out of our pumps,” says Karsch. "We are essentially the competence centre for KSB's test facility technology. We design and build test stands, create central KSB standards – for online acceptance tests for example – and develop KSB’s in-house software for data acquisition on all KSB test stands worldwide." Continuous, cutting-edge development of testing options and thus of KSB products is ensured thanks to the work of more than 30 staff and numerous students who always bring fresh ideas, as well as cooperations with multiple universities. "This is what we stand for. And our know-how is available to the entire KSB Group," underlines Karsch.
6. USA: Highest expertise for all types of sludge
GIW Industries in Grovetown became part of the KSB Group in 1988. The company manufactures slurry pumps that are primarily used in mining. GIW pumps transport sludge whose abrasive solids could quickly cause wear. "GIW's hydraulics laboratory is globally unique in its capacity to handle pump performance testing and slurry testing. On the one hand, it is able to verify the performance of pumps with impeller diameters of up to 2.87 metres. On the other, it has the expertise to test slurries in pipelines of any size,” reports George McCall, who heads the hydraulics laboratory at GIW.
The test facilities are primarily intended for testing the pumps typically manufactured by GIW: end-suction, single-stage centrifugal pumps for slurries. However, they can also be configured to test any pump.