
Invisible heroes of mobility transition: How pumps and valves enable sustainable mobility
Rechargeable batteries are decisive for the transition to an electromobility with low CO₂ emissions. What is not widely known: Pumps and valves play a key role in producing batteries for electric cars.
Pumps and valves play a crucial rule in manufacturing batteries.
Producing electric car batteries requires a complex production chain distributed over the entire globe – pumps and valves are involved in almost every step of the production chain.

The production chain of lithium-ion batteries: The numbers refer to examples of process steps in which pumps and valves play a crucial role. They will be explained below in more detail.
The production chain starts with mining raw materials such as lithium, cobalt, manganese, nickel and graphite. These are the active materials (Battery Active Materials, BAM), whose electrochemical properties allow energy to be stored. The most important of these raw materials is lithium, which is isolated and cleaned in the lithium refining step. In parallel, cathode materials are manufactured that can absorb and release lithium ions, which is required to charge and discharge the battery. At the same time, an electrolyte is produced, which is a liquid that allows lithium ions to move. The next step is that of manufacturing cathodes. In the step of assembling and filling the battery cells, cells are made out of the electrode and electrolyte materials. They can be connected in series or in parallel to reach the required voltage. Once the life cycle of the battery has come to an end, the majority of raw materials can be recycled and re-used.
How do pumps and valves contribute to battery production? The numbers in the above infographic indicate steps in which pumps and valves play a crucial role. Let’s have a look at them in more detail.
2. Lithium refining: Hermetically sealed chemical pumps for hot and aggressive solutions
Lithium is the most important of the active materials. Lithium refineries separate it from other substances such as calcium or magnesium to make it usable for battery production. To do so, they heat up the mined and concentrated substance and mix it with sulphuric acid to extract the lithium. If the concentrate was extracted from a brine, they add soda to precipitate out lithium compounds in the form of white flakes. A different procedure is used by the company Vulcan, pumping hot brine from a depth of 3000 to 5000 metres below the Rhine Rift Valley in Germany: They use electrolysis to separate the salt in the brine into lithium and chlorine. The end products of these processes are lithium carbonate, lithium hydroxide or metallic lithium. What all these procedures have in common is that they place extremely high demands on pumps and valves because they work with corrosive, abrasive and often hot solutions. In general, plastic-lined valves and pumps are needed that are resistant to chemicals. An example of a suitable pump is KSB’s Magnochem standardised chemical pump. It uses a magnetic coupling for transmitting the torque to the shaft through the casing without any contact. As this eliminates the need for sealing elements at which leakage could occur, the pump is particularly suited for handling toxic and corrosive fluids. The pump set can handle temperatures of up to 400 °C.
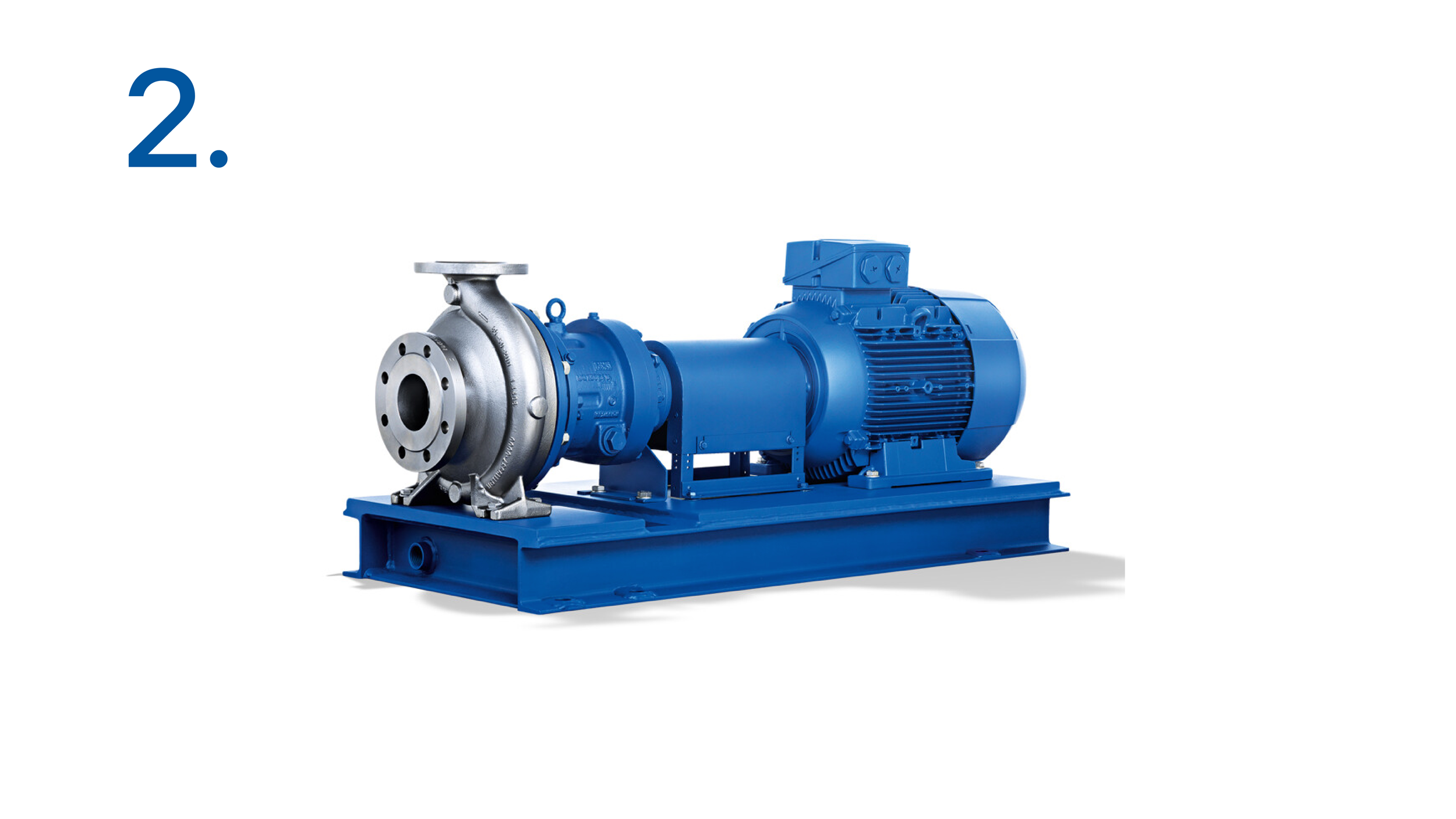
4. Electrolyte production: Valves take care of accurate dosing of solvents and salts.
Lithium batteries are filled with a liquid that enables the movement of lithium ions between the two poles of the battery, i.e. the cathode and the anode. This liquid, which is called the electrolyte, is usually a solvent containing a lithium salt, such as lithium hexafluorophosphate (LiPF6). In chemical companies producing electrolytes, pumps and valves take care of transport from the storage containers to the mixing tanks. Precision is key as the contents have to be accurately dosed to ensure even and effective battery performance. Also, leakage has to be safely prevented and the devices have to be resistant to aggressive substances. Because if LiPF6 escapes, it can react with moisture and form highly toxic and aggressive hydrofluoric acid (HF). In addition, the organic solvents are flammable. Suitable pumps are the MegaCPK and the hermetically sealed Magnochem. An example of an appropriate valve is the SISTO-20 diaphragm valve lined with polytetrafluorethylene (PTFE). PTFE is resistant to strong acids, bases, solvents and oxidising agents. It also has a very low friction coefficient. This means the valves are easy to actuate, which also makes accurate dosing easier.
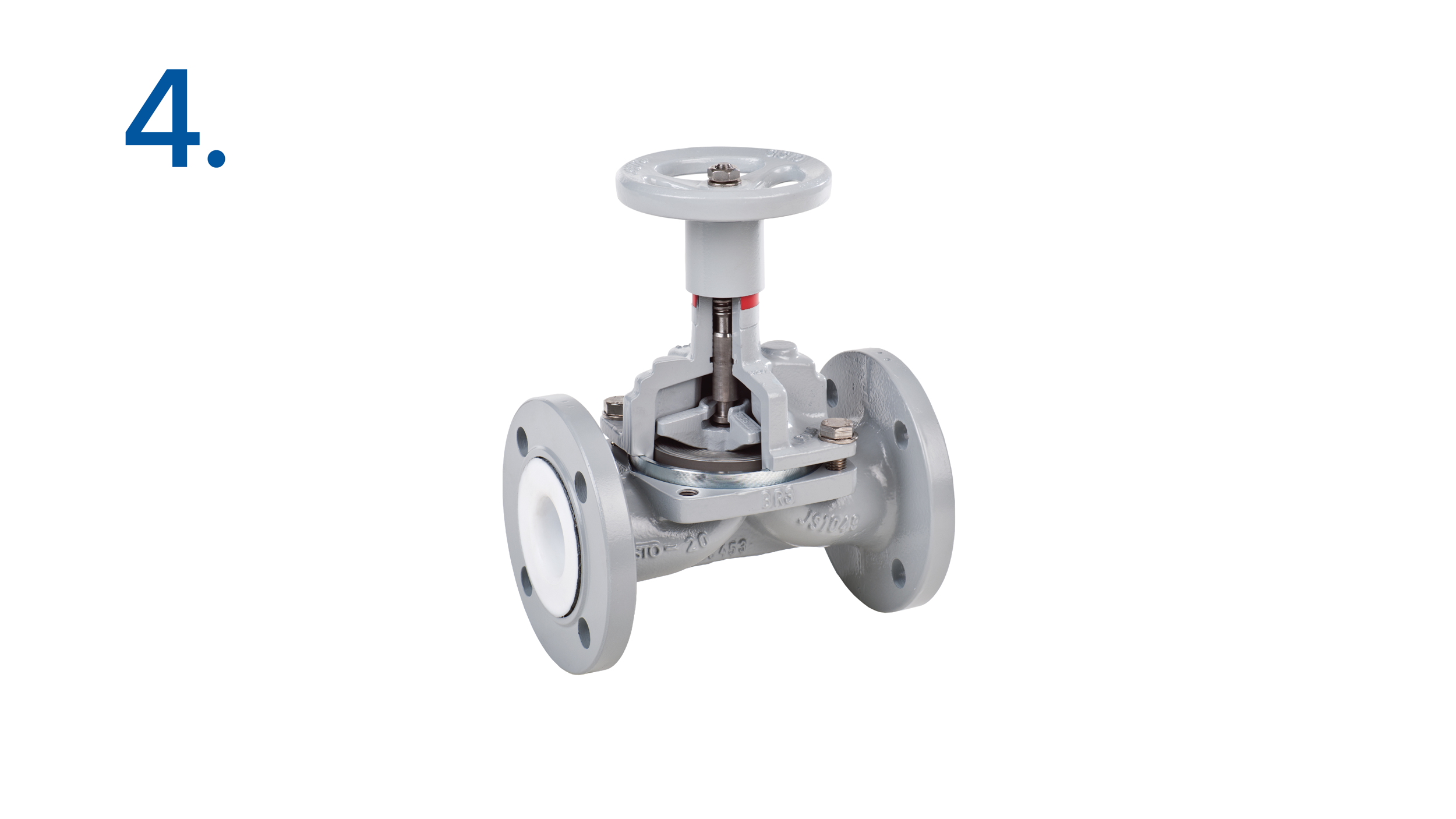