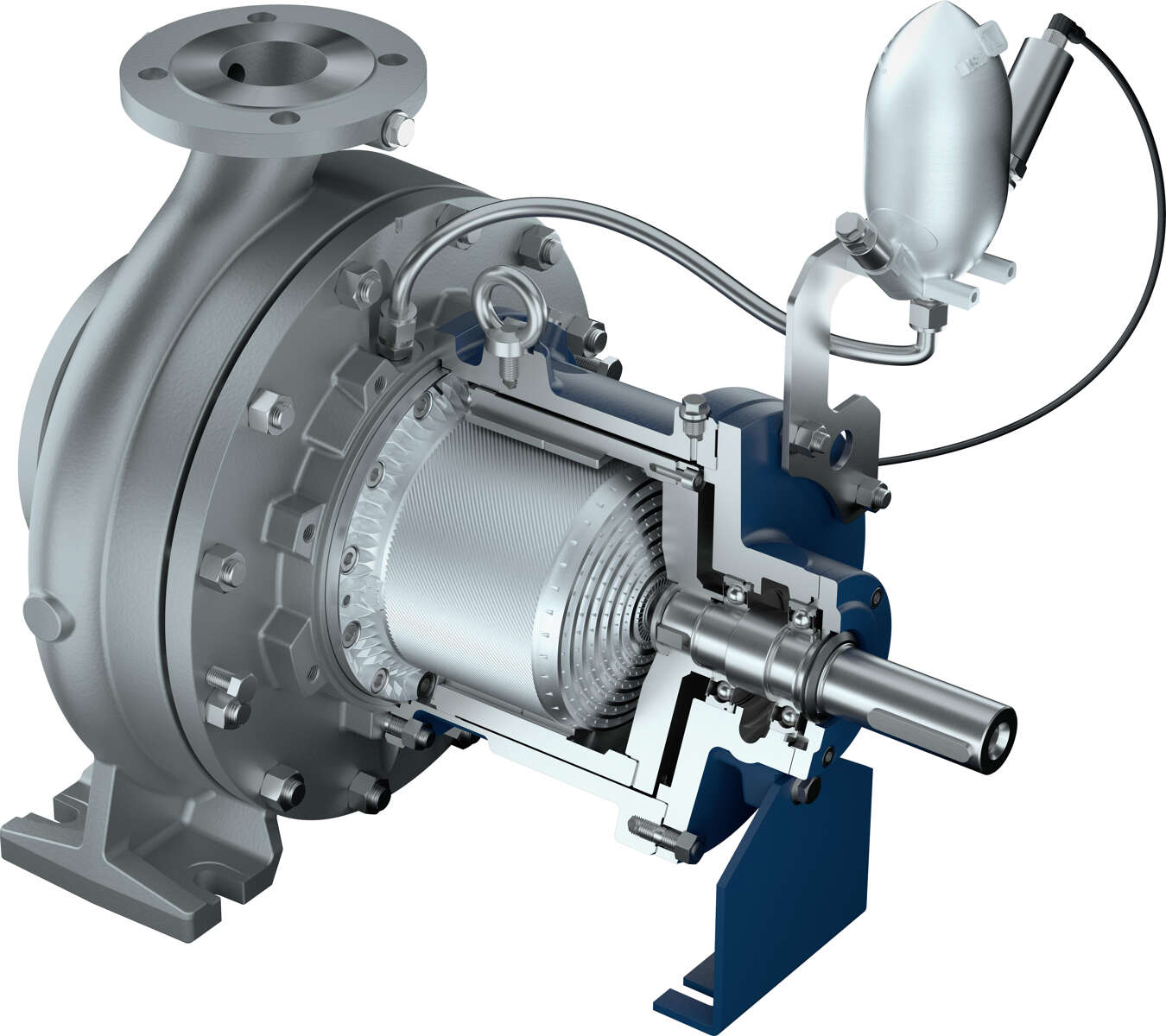
High-tech containment shroud for mag-drive pumps
formnext 2024, Stand 12.0 B01M
At formnext 2024 (19 – 22 November 2024, Stand 12.0 B01M), KSB SE & Co. KGaA will be presenting a new containment shroud for mag-drive pumps manufactured using a 3D printing process.
Named MagnoProtect, the component offers the same safety as a double-walled containment shroud – without the latter’s disadvantages of heating up strongly and having high eddy current losses.
While providing comparable safety, the overall efficiencies of the new mag-drive designs clearly exceed those of canned motor pumps. Designed with a structure of channels, the new containment shroud offers a second, redundant, static safety barrier preventing leakage of the fluid handled. The design of the containment shroud is characterised by high mechanical strength and good wear properties. Its design is optimised to minimise heat loss and eddy currents.
Converting a standardised chemical pump with mechanical seal to a magnetic drive is easier and more cost-efficient than retrofitting it with a canned motor. The geometry and dimensions of the new containment shroud are integrated in the modular system of Magnochem, allowing metallic or ceramic containment shrouds to be replaced easily. This enables operators to upgrade older pump sets that are still in service without difficulty.
Over the past 10 years the pump manufacturer KSB has built comprehensive expertise in additive manufacturing using metal-based powder bed fusion (PBF) at its site in Pegnitz, Germany, where it operates four systems for this type of additive manufacturing. In the Additive Manufacturing Center specialists work with materials such as stainless steel, nickel-base alloys and other iron-based metal powders.
Press release: High-tech containment shroud for mag-drive pumps
Press photo: High-tech containment shroud for mag-drive pumps