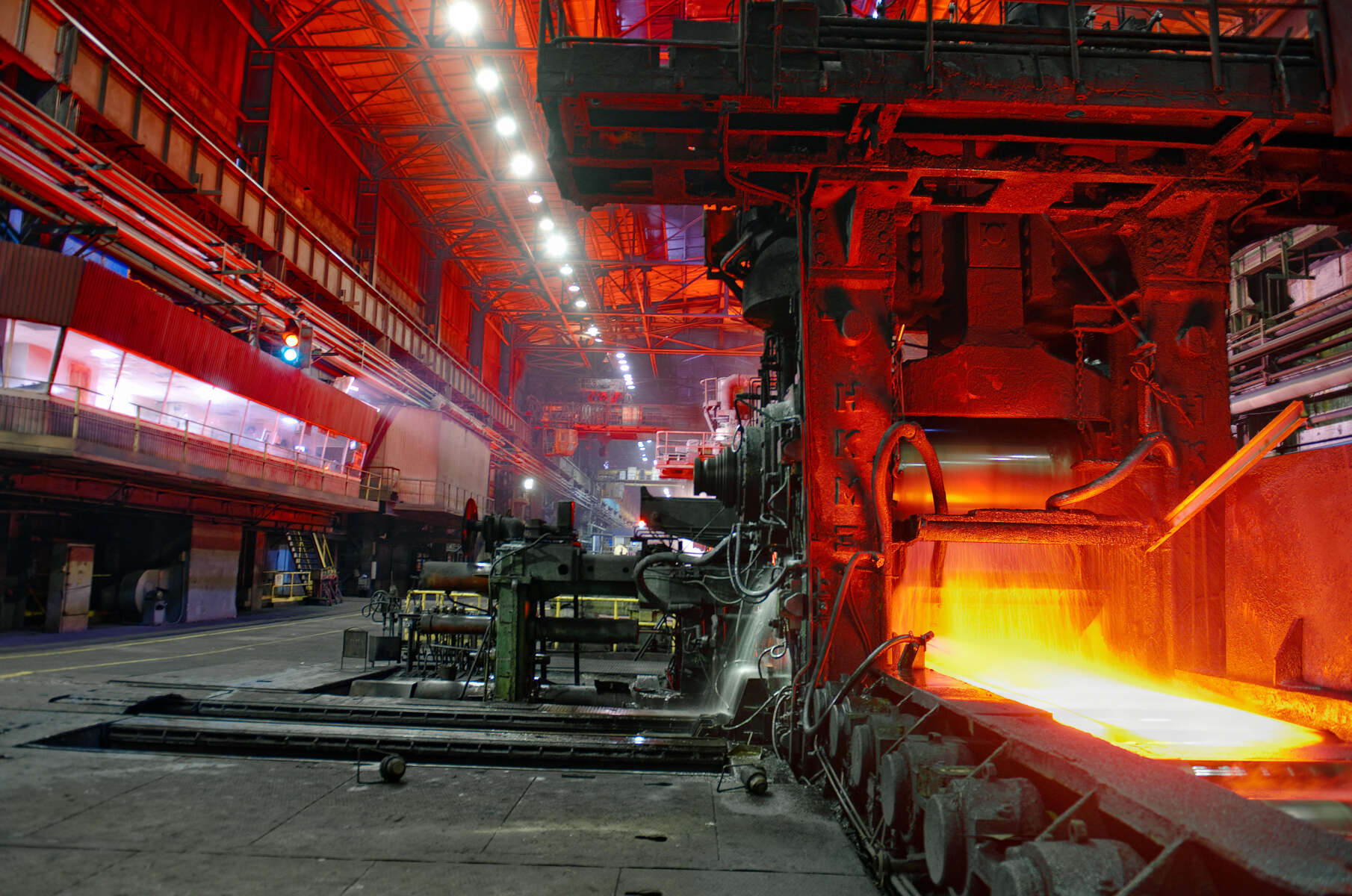
Effizienzoptimierung bei einem Stahlproduzenten – mit dem SES System Effizienz Service®
Jährlich werden in Deutschland rund 40 Millionen Tonnen Stahl produziert. Doch für die Produktion solch großer Stahlmengen wird auch viel Energie benötigt: rund 160 TWh pro Jahr. Ein optimiertes Pumpensystem kann einen erheblichen Teil dazu beitragen, die Energiekosten zu senken. Daher beauftragte ein großer Stahlhersteller KSB damit, sein Pumpensystem auf mögliche Energieeinsparpotenziale hin zu überprüfen und um geeignete Maßnahmen daraus abzuleiten
Jährlich werden in Deutschland rund 40 Millionen Tonnen Stahl produziert. Doch für die Produktion solch großer Stahlmengen wird auch viel Energie benötigt: rund 160 TWh pro Jahr. Ein optimiertes Pumpensystem kann einen erheblichen Teil dazu beitragen, die Energiekosten zu senken. Daher beauftragte ein großer Stahlhersteller KSB damit, sein Pumpensystem auf mögliche Energieeinsparpotenziale hin zu überprüfen und um geeignete Maßnahmen daraus abzuleiten
Die Herausforderung
Das Pumpensystem bei einem Stahlgiganten effizienter gestalten.
Im Durchschnitt werden für die Produktion einer Tonne Flüssigstahl ca. 500 kWh Einschmelzenergie (aus Strom und Erdgas) benötigt. Damit gehört die Stahlindustrie zu den energieintensivsten Branchen überhaupt. Enorme Einsparpotenziale stecken auch in den Pumpensystemen. Denn viele Pumpen in der Stahlindustrie sind dramatisch überdimensioniert, was zu einem unnötig hohen Energieverbrauch führt. Laut Einschätzung des Fraunhofer-Instituts ISI sind schlecht ausgelegte Pumpensysteme in der Industrie für rund 30 Prozent des Stromverbrauchs verantwortlich.
Einem großen Vertreter der Stahlindustrie war dies bekannt und er beauftragte KSB damit, mögliche Energieeinsparpotenziale in seinem Pumpensystem zu identifizieren. Die Experten des SES System Effizienz Service® führten zunächst eine umfassende Analyse des Systems durch. Die beinhaltete u. a. eine Betriebspunktermittlung, eine Analyse der Maschinenzustände, eine Energieeffizienzanalyse (Ermittlung von Druckverlusten, Mengensteigerungen etc.) sowie eine Schadensanalyse (detaillierte Betrachtung des Pumpensystems hinsichtlich Betriebsweise, Prozessparameter, Schwingungsanalyse).
Die Fachleute deckten dabei eine ganze Reihe an Schwachstellen im Pumpensystem auf, die sich negativ auf die Energiebilanz des Unternehmens auswirkten: Angefangen bei signifikanten Abweichungen zu Nennkennlinien bei den Speisewasserpumpen, über extrem hohe Schwingungen in hohen Betriebsbereichen (was zu Ausfällen der Pumpen führen kann) bis hin zu akut festgestellten Lagerschäden.
Die Lösung
Der SES System Effizienz Service® bringt Transparenz in Pumpensysteme und optimiert so die Energie-Effizienz
Glücklicherweise entschied sich das Unternehmen mit KSB für einen Partner, der nicht nur systematische Systemanalysen durchführen kann, sondern der auch – dank seiner weitreichenden Expertise und seines umfassenden Produktportfolios – die passenden Maßnahmen zur Behebung dieser Probleme und zur Steigerung der Effizienz des Pumpensystems parat hat.
KSB formulierte auf Basis der Analysen folgende Ziele für die Anlagenoptimierung:
- Optimieren der Instandhaltungsmaßnahmen (für maximale Betriebssicherheit): u. a. durch eine Verbesserung des Pumpenbetriebsbereiches (Reduzierung, Verschleiß, Lagerschäden) sowie die Vermeidung einer Unterschreitung des NPSHerf-Wertes.
- Reduzieren der Energiekosten: u. a. durch die Reduzierung des Regeldrucks und den Einsatz von FUs sowie durch den Einsatz effizienterer Hydrauliken (optimal auf den Betriebsbereich abgestimmt) sowie hocheffizienter Motoren.
Darüber hinaus gab es noch weitere Ziele wie z. B. ausreichend Reserve, um Mengenspitzen abzudecken sowie eine ausreichende Nullfördermenge, um eine Druckprobe durchzuführen.
Das Ergebnis
Mehr Betriebssicherheit, mehr Effizienz – und eine Amortisation der Kosten nach bereits 1,3 Jahren
Anschließend ging es an die Umsetzung der Optimierungsmaßnahmen. KSB installierte zwei neue drehzahlgeregelte Aggregate und erhöhte gleichzeitig die mögliche Fördermenge der Pumpen. Darüber hinaus nahm KSB auch bei den Pumpenanschlüssen und bei den Einzelleitungen Optimierungen vor und implementierte ein neues System zur Pumpenregelung. Praktisch: Der Umbau war bei laufendem Betrieb möglich, sodass es zu keinen Betriebsausfällen kam.
Allein durch die Analyse und Optimierung einer einzelnen Speisewasserpumpe, die nicht ausgetauscht wurde, ließen sich allein bei dieser Pumpe Energie-Einsparungen in Höhe von über 20 % realisieren. Durch den Ersatz der beiden anderen Speisewasserpumpen (inkl. Motor und Regelungen) ließ sich eine zusätzliche Energie-Einsparung von rund 60 Prozent erzielen, was dem Unternehmen nun jährlich weitere Kosten in Höhe von rund 125.000 Euro spart. Die investierten Kosten amortisieren sich bereits nach 1,3 Jahren. Die Energie-Einsparungen betragen nach 5 Jahren rund 600.000 Euro (300.000 Euro pro Pumpe). Und nicht nur das Unternehmen, auch die Natur profitiert: Der ökologische CO2-Fußabdruck konnte aufgrund des geringeren Energieverbrauchs auch verkleinert werden.
Hätte sich das Unternehmen für eine Modernisierung der gesamten Anlage entschieden und auch die erste Pumpe ausgetauscht, hätte es sogar noch mehr sparen können. Das Unternehmen hätte Energie-Einsparungen in Höhe von 72 Prozent erzielen können, was die Amortisation weiter verringert hätte (1,2 Jahre statt 1,3 Jahre).
Hier gut zu erkennen: in rot die Kosten ohne Modernisierung, in blau die Kosten mit Modernisierung. Die Einsparungen beginnen bereits nach ca. 1,3 Jahren.
Vorher | Nachher | |
Energiekosten pro Jahr | 208.198 € | 83.272 € |
Energiekosten Einsparungen in % | 60 | |
CO2-Emissionen in Tonnen pro Jahr | 986,9 | 394,7 |
Investitionskosten | 60.000* | 256.680 |
Return of Invest in Jahren | ca. 1,3 | |
Einsparungen nach 10 Jahren | 1.075.901 |
*eine neue Pumpe benötigt, Komplettausfall
Zahlen | Daten | Fakten
Anwendungsbereich: Stahlproduktion
Projektjahr: 2021
Umfang: Instandsetzung und regeltechnische Optimierung einer Bestandspumpe sowie Installation von 2 neuen drehzahlgeregelten Speisewasserpumpen
Bestand | Optimiert | |
Antriebsleistung [kW] | 2x 315, starr 1x 355, geregelt | 2x 250, geregelt 1x 355, geregelt |
Energieeinsparung | - | 60% |
Energieverbrauch p.a. [kWh] | 2.082.000 | 833.000 |
CO2 -Emissionsfaktor [g/kWh] | 474 | 474 |
Emissionen p.a. [t CO2 ] | 987 | 395 |
Strompreis [€/MWh] | 100 | 100 |
Amortisationszeit [Jahre] | - | 1,3 |