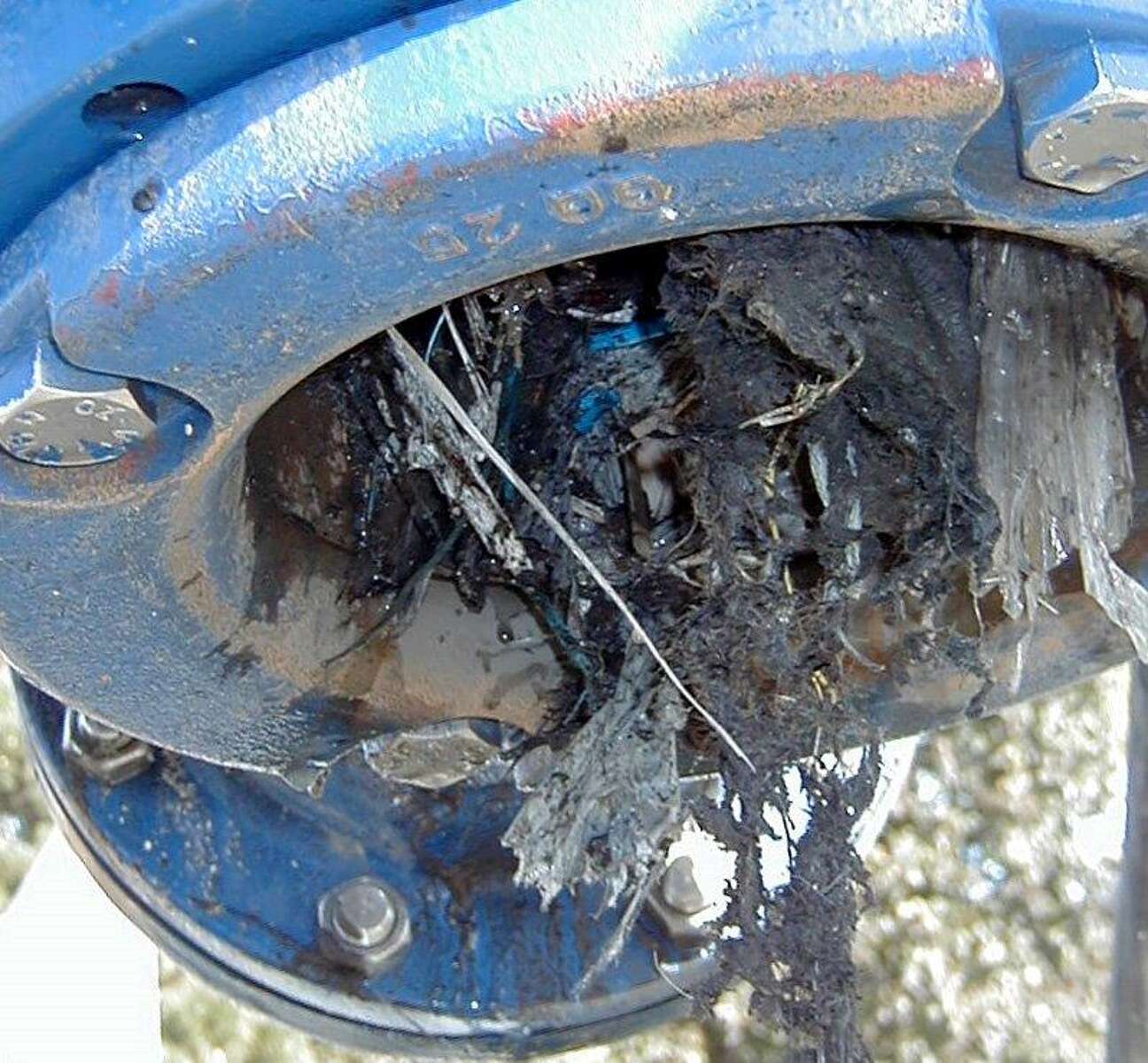
6 Wastewater Pump Symptoms You Don’t Want to Ignore - and why you might be seeing them now more than ever
latex gloves and other materials residents are using to combat the corona virus, wastewater operators are seeing a sharp increase in wastewater clogs. As demand for cleaning wipes has skyrocketed, wastewater operators must grapple with the results of improper disposal.
Addressing even partial clogs in a timely manner is imperative to the well-being of your pump and system. When clogs are not quickly cleared, the foreign matter can contaminate the seal chamber fluid leaving the pump vulnerable to failure.
As the saying goes, an ounce of prevention is worth a pound of cure. Check out the following 6 signs that you may have a clog forming, and don’t delay in clearing out even small clogs!
- Reduced flow or discharge pressure: a partially clogged or fully clogged impeller or pump will result in lower than normal flow rates and discharge pressure.
- Rising temperatures: when a pump impeller is clogged this puts addition stresses on the motor as more energy is required to rotate the impeller. This will result in higher stator and bearing temperatures which can be detected on the thermistors & RTD’s.
- Higher amperage and constant overload trips: as the motor works harder to rotate the equipment, these additional forces will increase the motor amperage which may result in repeatedly tripping the overloads.
- Cavitation sounds: A partially clogged suction inlet or pump results in a lower NPSHA (Available Net Positive Suction Head.) Cavitation occurs when the NPSHA drops below the NPSHR (Required Net Positive Suction Head.) This often sounds like gravel circulating through the pump casing, and can be almost as damaging to your equipment as actual gravel.
- Vibration: an impeller tangled in foreign matter will throw off the entire assembly balance and cause vibrations which can be both felt and heard.
- Seal failures: Process fluid is what lubricates the lower mechanical seal. Once process fluid is restricted due to a full or partial clog, the lower mechanical seal can begin to run dry resulting in worn, scored or damaged seal faces. Foreign matter tangled on the lower mechanical seal spring can also prevent process fluid from adequately lubricating the seal. The compromised seal then allows process fluid to leak into and contaminate the seal chamber oil.
When clogs are not quickly cleared, the foreign matter can contaminate the seal chamber fluid and begin to wear down the upper mechanical seal. Luckily most pumps are equipped with a moisture sensor within the stator housing which will shut the pump down once moisture is detected. However, if the sensor malfunctions and the pump continues to run, electrical failure is almost a certainty.
If you recognize any of these signs in your pumps, don’t wait to take action. Quickly eliminating the forming clog can save your pump. Give Mike Kruis, our Service Manager, a call at (647) 218-3351 if you could use the expertise of the KSB SupremeServ team on your side in the battle against the clog! He can quickly put you in touch with the nearest KSB Service Centre.