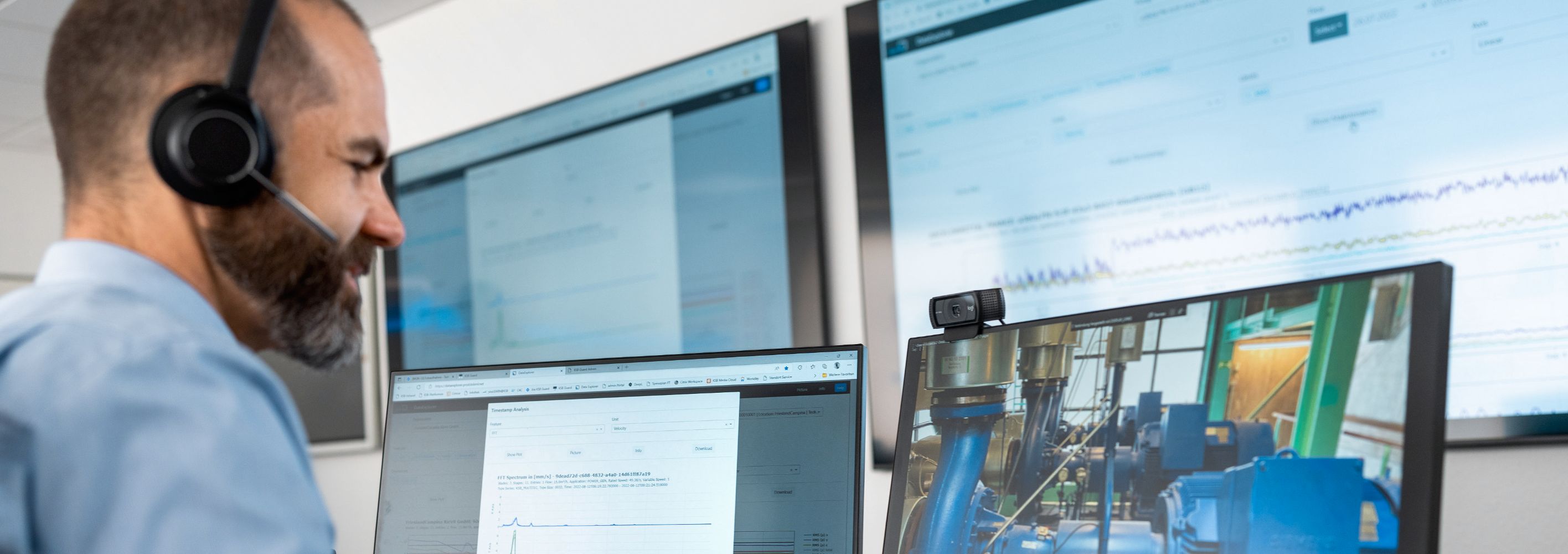
Remote monitoring
Production facility breakdowns cost companies a lot of time and money. KSB SupremeServ Monitoring minimises downtime by detecting damage to machinery at an early stage. The smart digital service thus enables customers to operate pumps and rotating machinery efficiently.
Global competition is exerting unprecedented levels of pressure on manufacturing companies to increase efficiency and reduce costs. Managing systems and plants via predictive maintenance plays a key role in achieving this goal. Predictive maintenance can prevent unplanned downtime and ensure that they operate efficiently. This supports maintenance planning and facilitates making processes more predictable. The approach is particularly relevant for waterworks, sewage treatment plants, industrial plants and companies in the chemical and energy industries.
Easy to get started
Predictive maintenance requires reliable data on the condition of the machines being monitored. KSB SupremeServ Monitoring offers a straightforward starting point for entering the world of predictive maintenance. The service is based on the KSB Guard monitoring unit, whose sensors record vibration and temperature levels of pumps and other rotating machinery. The continuous digital data acquisition performed by KSB Guard provides a comprehensive overview of the pump set’s condition.
Fast analysis
Some companies lack experienced diagnostic experts capable of analysing and correctly interpreting a machine’s data. It is these companies which stand to benefit from KSB SupremeServ Monitoring. “We are already remotely monitoring more than 3,000 pumps in around 40 countries worldwide,” says Lukas Schneider from the KSB SupremeServ Monitoring Center in Frankenthal. “In addition to conventional diagnostic procedures, we also use artificial intelligence.” This role as a remote monitoring service moves KSB one step closer to its customers.
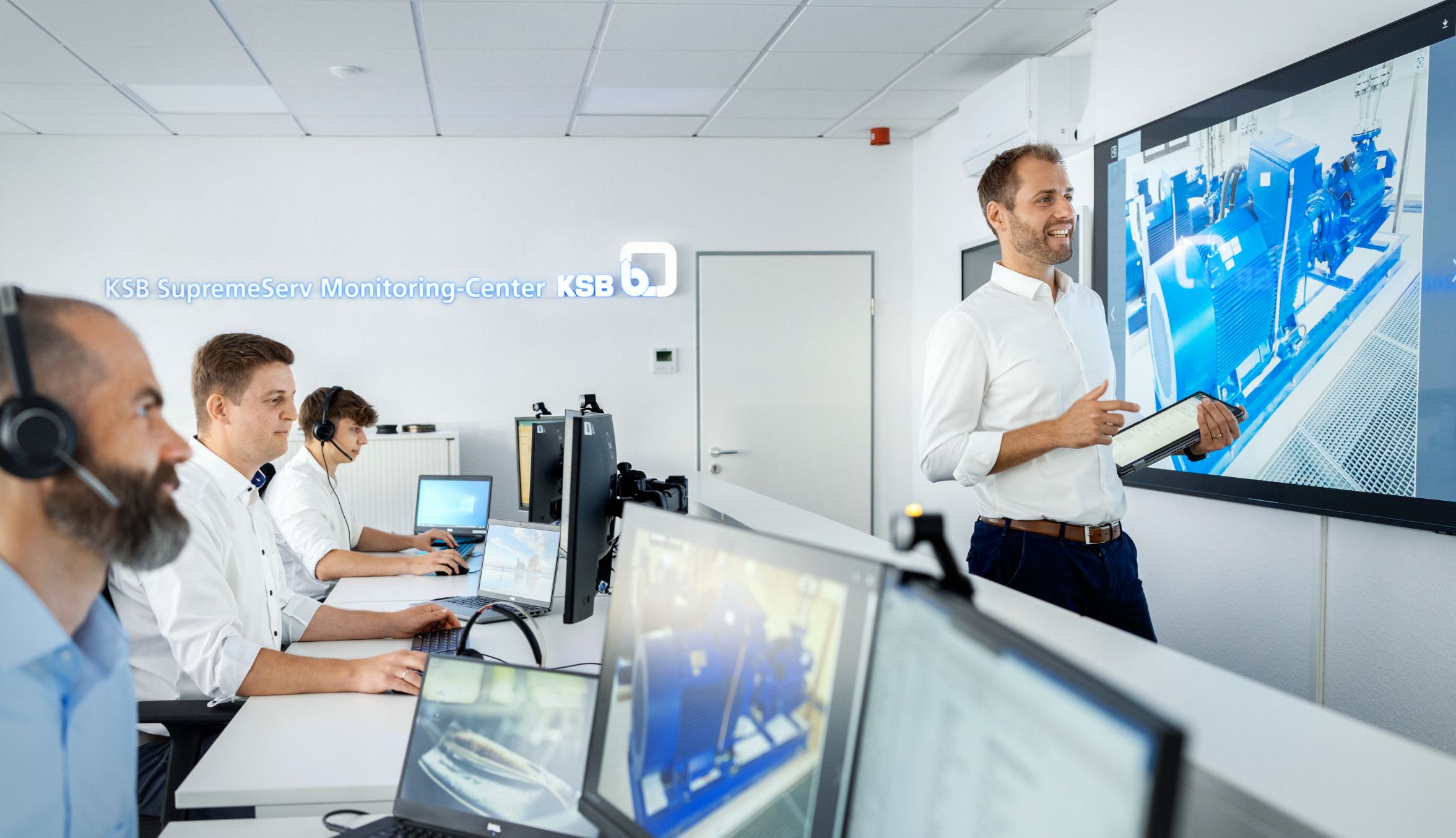
KSB’s diagnostic experts in Frankenthal remotely monitor their customers’ pumps.
Experts at one of the KSB SupremeServ Monitoring Centers in Frankenthal, Germany, and in Pune, India, receive information from the KSB Cloud. All of the data transmitted by pumps and machinery is sent there for expert analysis. The transmitted data is displayed as numerous coloured lines on the screens of the diagnostic experts – similar to the way cardiologists interpret an electrocardiogram. Detailed analysis begins as soon as the team recognises anomalies in the measurement data. Besides high-quality measurement data, this requires a great deal of expertise. KSB also has the advantage of over 150 years of experience in manufacturing pumps, providing valuable insights and information for the analysis. KSB’s customers benefit from the added value of recognising damage at an early stage and being able to initiate targeted action. The result is reliable and safe operation of their production systems.
After analysing the data in detail, KSB’s experienced diagnostic experts document the results and provide information to the customer. This includes the suspected cause of the damage and specific advice on what to do next. In most cases, this is a recommendation for repair or maintenance measures. These are provided quickly and efficiently by KSB SupremeServ’s technicians – an allround carefree package for the customer.
“The KSB SupremeServ monitoring service expands our range of services and supports our customers through the proactive provision of recommendations for efficient pump operation,” outlines Lukas Schneider. “We not only analyse the measurement data, but also offer suitable services or the required spare part.”
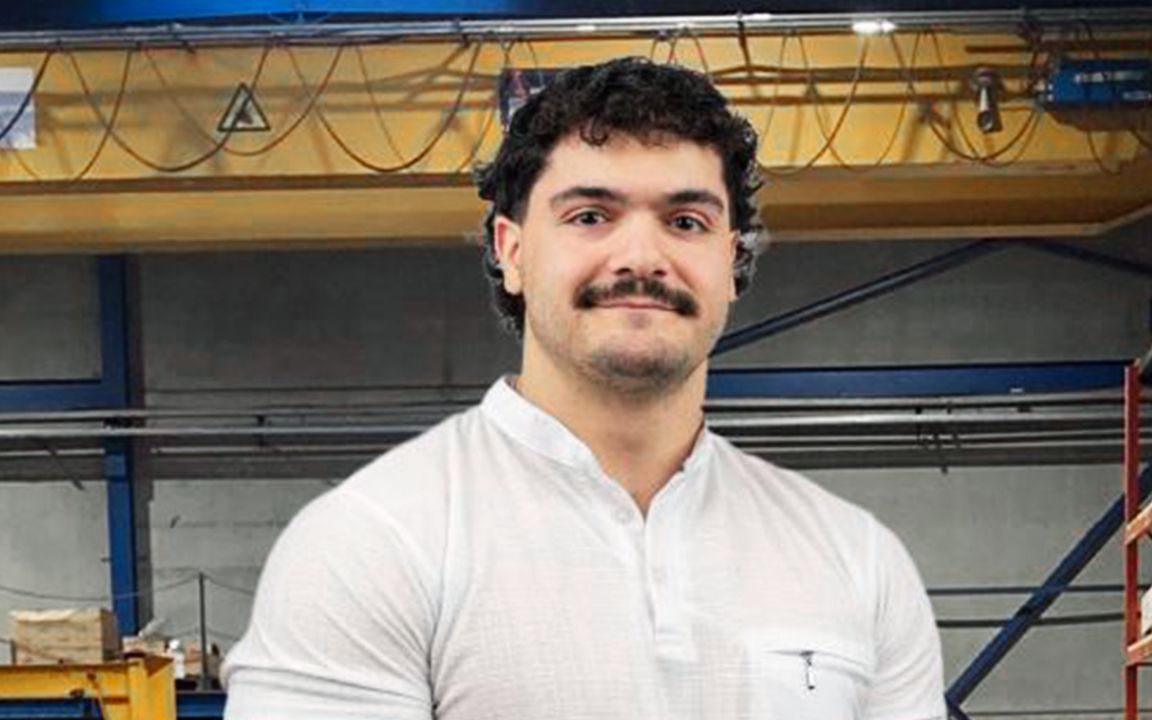
“We extend the service life of our customers’ pumps.”
Wouter De Mesmaeker, Engineer at KSB SupremeServ in Belgium
In use with the customer
An example from Belgium shows what KSB SupremeServ Monitoring looks like in practice. A car manufacturer produces its vehicles there and uses various pumps in its production facilities. The company tested KSB Guard on a pump used in the paint shop for handling thinned, excess paint for recycling.
“The transmitted data revealed that the pump impeller was out of balance,” explains Wouter De Mesmaeker, who works as an engineer at KSB SupremeServ in Belgium. “We then took a closer look at the pump set and found that the pump casing, discharge cover and impeller were heavily soiled with paint residue.” These three heavily contaminated wetted components were causing high vibration levels detectable in the blade passing frequencies – a typical characteristic of centrifugal pump vibrations. In short: The pump could not work reliably and efficiently, and its life expectancy was significantly decreased.
Following this quick diagnosis, the service team put the pump back into operation temporarily so that the production facility could run as usual for a week. The pump set was then overhauled when there was a scheduled break in production operations the following weekend.
As a first step, service specialists from KSB SupremeServ dismantled the pump, cleaned the affected parts and carried out a thorough sandblasting. After extensive testing and measurement work, the team of technicians reassembled the pump set.
However, this remained a temporary solution to the customer’s problem. “We therefore offered a special anti-adhesive coating for the affected pump components,” says Wouter De Mesmaeker. The service experts also recommended customised, high-quality materials for the pump set’s other components. “Our recommendations extended the service intervals and thus the service life of our customer’s pump.”
Just like the example in Belgium, KSB’s customers worldwide can benefit from digital services capable of recognising signs of wear and damage to pumps and rotating machinery at an early stage. This means that necessary maintenance and repair work can be planned and carried out ahead of time to prevent possible consequential damage.
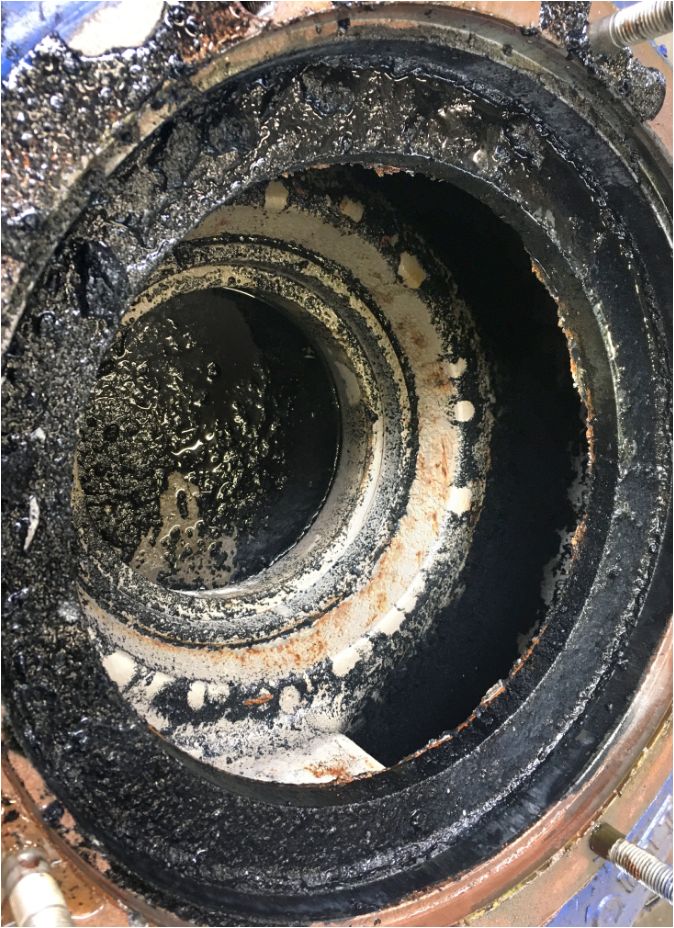
A heavily soiled component was identified as the cause of a pump impeller that was out of balance at one of KSB’s customers in Belgium. Thanks to KSB SupremeServ Monitoring and the swift action of KSB SupremeServ engineers on site, the pump set was soon able to work efficiently again.
Many pumps to save
By combining digitalisation and services, KSB offers its customers not only the right products, but also the right services. “Using KSB SupremeServ Monitoring gains companies an advantage in international competition,” says Lukas Schneider. “This is because we contact our customers with the solution before they even know they have a problem.”
It should be noted that using KSB Guard is particularly worthwhile for older pumps. The system can monitor machines of any age from any manufacturer. Monitoring is particularly recommended for older pumps. Around the world, countless pump sets have been running for decades – and many of them are no longer as efficient and reliable as they should be. As Lukas Schneider knows from experience: “Pumps deteriorate gradually. Our task is to prevent this in good time.”
“We are already monitoring over 3,000 pumps in around 40 countries.”
Lukas Schneider, Head of KSB SupremeServ Monitoring Center
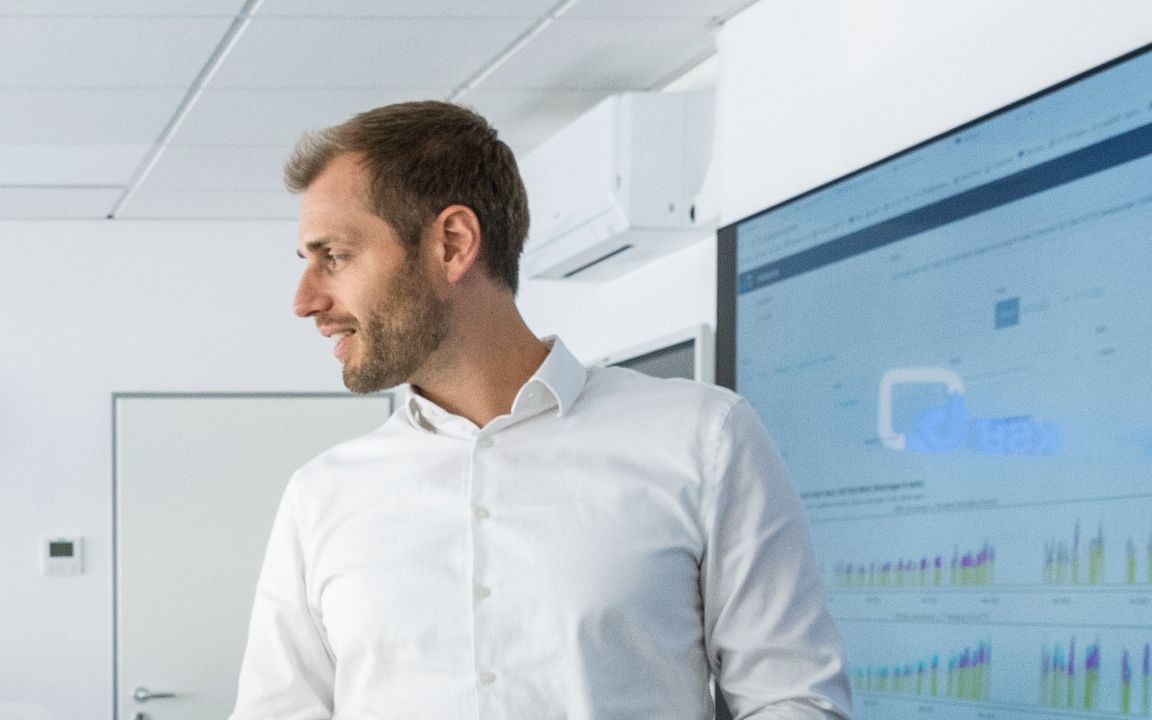
Lukas Schneider gives a tour of the KSB SupremeServ Monitoring Center in Frankenthal.