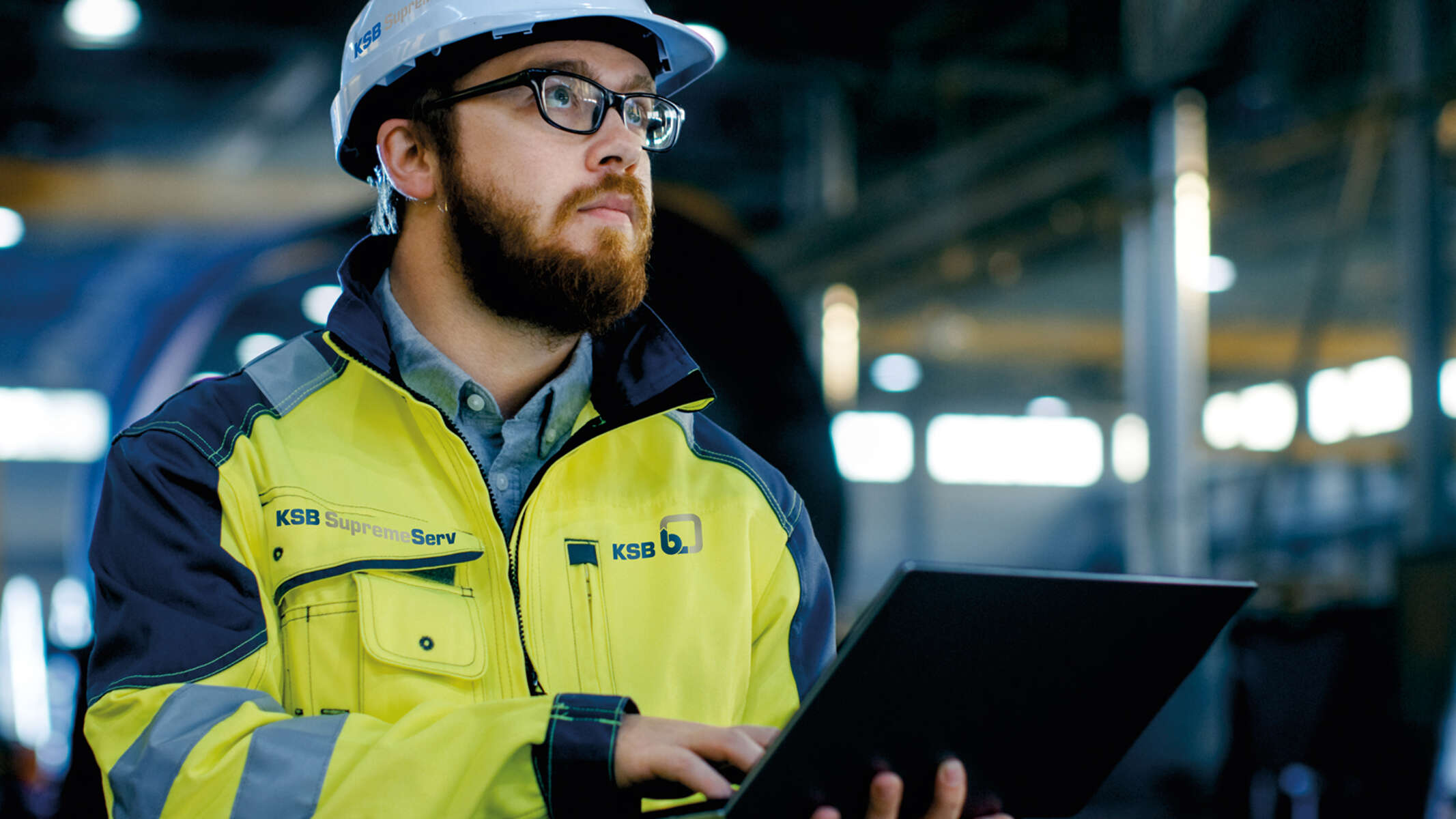
Mantenimiento 4.0: Cómo la digitalización simplificará el mantenimiento.
La cuarta revolución industrial viene con muchas nuevas oportunidades de digitalización y automatización que muchas empresas ya están aprovechando. Y con razón.
La cuarta revolución industrial viene con muchas nuevas oportunidades de digitalización y automatización que muchas empresas ya están aprovechando. Y con razón.
Por qué la gestión del mantenimiento es de gran importancia
La creciente presión de los costes obliga a muchas empresas a buscar nuevas formas de aumentar la eficiencia. Al mismo tiempo, ya se ha explotado la mayor parte del potencial de ahorro y racionalización. Por ello, cada vez son más las empresas que identifican el mantenimiento como un factor real de creación de valor. "Mantenimiento 4.0" es la palabra de moda en este contexto. La prevención de tiempos de inactividad no programados mediante la detección temprana de signos de desgaste y defectos tiene la ventaja de generar enormes ahorros. Aquí es donde la Industria 4.0 ofrece diversas oportunidades que remodelarán radicalmente el mantenimiento en el futuro. Siga leyendo para saber más.
Los sistemas están sujetos a un desgaste continuo, y esto no solo afecta a los componentes móviles: incluso cuando un sistema se utiliza en raras ocasiones o no se utiliza en absoluto, su funcionalidad técnica puede verse significativamente afectada. Los componentes con hierro pueden comenzar a oxidarse, las juntas de plástico o goma pueden volverse porosas o la viscosidad de los aceites utilizados puede disminuir. Descuidar la gestión del mantenimiento puede tener impactos negativos considerables en el nivel de calidad de la producción, así como en los procesos comerciales en general.
En el peor de los casos, un fallo o daño no detectado puede hacer que un sistema completo falle y que todo el proceso de producción se detenga. Tampoco hay que subestimar las consecuencias de un mantenimiento descuidado: el fallo de un solo componente, por ejemplo, un defecto en el material puede causar daños importantes en el futuro. Es por eso por lo que el mantenimiento se está convirtiendo en un factor de éxito crucial para muchas empresas.
La gestión del mantenimiento ha aumentado en importancia
La importancia que se le da al mantenimiento ha crecido en los últimos años. Una de las principales razones detrás de este desarrollo es el aumento constante de la presión competitiva global. Esto ha llevado a que la Efectividad General del Equipo – EGE (OEE), un indicador clave de la productividad de una planta, gane importancia. La máxima disponibilidad y la eficiencia de los recursos son cifras clave en este contexto.
Las actuales estrategias de un mantenimiento optimizado tienen como objetivo principal prolongar la vida útil, acortar los tiempos de inactividad programados y evitar los tiempos de inactividad no programados, en otras palabras: su objetivo es maximizar la disponibilidad de la planta.
La complejidad técnica de las plantas ha aumentado exponencialmente en las últimas décadas, y los sistemas de producción están ahora estrechamente interrelacionados entre sí, tratando de evitar los stocks de seguridad. Un fallo en una parte del proceso puede provocar rápidamente el fallo en cadena de otros procesos, lo que conlleva importantes consecuencias económicas. Esto ha originado un cambio de perspectiva en la gestión, ya que el mantenimiento se acerca cada vez más a la producción y a la planificación de los recursos, y se percibe como un factor decisivo de éxito.
El uso de soluciones digitales puede ser especialmente útil: sobre la base de los datos de estado de la maquinaria, se pueden detectar daños inminentes con antelación e implementar medidas de mantenimiento en una fase temprana. Esta es una oportunidad para reducir los costos de mantenimiento y prevenir los costos de los tiempos de inactividad en la medida que sea posible.
Especialmente en un mundo de procesos de producción cada vez más complejos, el tema "Mantenimiento 4.0" está ganando importancia.
Mantenimiento en el pasado y en el presente
Al igual que la historia industrial con sus diferentes generaciones (Industria 1.0 a Industria 4.0), el mantenimiento también se puede dividir en generaciones. Se puede hacer una distinción general entre las diferentes estrategias de mantenimiento utilizadas:
Mantenimiento 1.0, hasta aproximadamente 1960: mantenimiento reactivo; reparación después de un fallo del sistema; también conocido como "mantenimiento de averías".
Mantenimiento 2.0,hasta aproximadamente 1980: mantenimiento preventivo en función del tiempo. El enfoque cambió hacia la disponibilidad, la vida útil y la reducción de costos.
- Mantenimiento 3.0, hasta aprox. 2015: mantenimiento condicionado mediante medidas manuales. A los aspectos del Mantenimiento 2.0 se sumaron puntos como la calidad constante y/o superior del producto, una mayor seguridad de la planta y del medio ambiente, así como una mayor rentabilidad.
- Mantenimiento 4.0, a partir de 2015 aproximadamente: mantenimiento orientado al estado del sistema mediante supervisión digital permanente, control del estado de la máquina, etc.
Hoy en día, el Mantenimiento 4.0 es un componente clave en la cadena de creación de valor de cualquier fábrica inteligente. El mantenimiento garantiza la estabilidad, la funcionalidad y la integridad de los sistemas 4.0 de alta complejidad. Los sensores y los sistemas ciberfísicos, así como el IoT (Internet of the Things - Internet de las cosas), desempeñan un papel fundamental.
Sensores inteligentes y gemelos digitales
En la era del Mantenimiento 4.0 la maquinaria se ha vuelto "inteligente": marca tendencias y alerta al usuario de posibles fallos propios o averías de los componentes. Esto se logra mediante una tecnología de sensores inteligentes instalada en componentes individuales o sistemas completos, que recopila continuamente datos sobre el estado de la máquina (p.e, temperatura, presión, intensidad o vibración). A partir de los datos recopilados y de la información conocida del objeto, se pueden crear gemelos digitales: imágenes digitales 1:1 del objeto real. Estos gemelos digitales permiten la implementación de un análisis y simulaciones complejas, formando la base de la Industria 4.0.
Los datos recopilados se documentan como parte de los "archivos digitales de historial del sistema". Estos completos archivos digitales se alimentan con datos de todos los componentes instalados en el sistema. Sirven especialmente para documentar continuamente el ciclo de vida de un sistema, proporcionando valiosos conocimientos actualizados que pueden utilizarse para trabajar en el mismo, tomar decisiones, tanto como evidencia de las tareas completadas o como base para la comunicación. Teniendo en cuenta que dichos datos provienen con frecuencia de diferentes fabricantes, se requieren interfaces universales para combinar y consolidar adecuadamente esa información.
Los datos que proporciona el archivo histórico digital no solo ayudan a planificar con mayor precisión el mantenimiento, sino que también permiten consolidar el mantenimiento en diferentes partes del sistema. Además de los trabajos de servicio realizados, el archivo también muestra todas las modificaciones del sistema, lo que es de gran importancia en la gestión de piezas de repuesto. Los dispositivos de monitoreo digital se pueden configurar para enviar automáticamente un mensaje push al operador si se ha producido una alteración del funcionamiento normal. Estos mensajes también se almacenarán en los ficheros del historial, donde se pueden editar o acceder a ellos en cualquier momento. Esto permite al equipo de mantenimiento vigilar su sistema en todo momento y saber exactamente cuándo puede ocurrir un fallo y, por tanto, cuándo es necesario el mantenimiento. Basado en esta información, los expertos pueden pedir las piezas de repuesto a tiempo y coordinar de manera eficiente los trabajos de servicio. Las tareas se pueden realizar con antelación para que el tiempo de inactividad del sistema sea el mínimo posible.
En conclusión, el mantenimiento predictivo será cada vez más relevante para una producción competitiva. Según un estudio* reciente realizado por el Foro Económico Mundial y la consultora Accenture, se puede ahorrar el 12 % de los costes con reparaciones programadas en lugar de no programadas y se puede ahorrar casi el 30 % de los costes de mantenimiento con este enfoque. Además, la proporción de tiempos de inactividad no programados puede reducirse hasta en un 70 %, según dicho estudio. Otro estudio* de Roland Berger muestra que el mantenimiento predictivo solo utiliza el 15 % del tiempo en mantenimiento, comparado con el 40 % usado en el mantenimiento "reactivo".
Las principales ventajas del Mantenimiento 4.0 en un vistazo:
Comprender mejor el proceso por la transparencia del sistema
Mejorar la rentabilidad al reducir los tiempos de inactividad planificados y evitar los tiempos de inactividad no programados
Consolidación y planificación del mantenimiento basado en el análisis permanente de los datos registrados (mantenimiento predictivo)
Aumentar la eficiencia de la maquinaria a medida que se identifica el potencial de mejora.
Los datos digitales permiten al equipo de mantenimiento vigilar su sistema en todo momento, para saber si pueden producirse fallos y cuándo.
Mantenimiento 4.0 en el ejemplo de la monitorización de bombas
Actualmente, existen diversos productos y servicios inteligentes que permiten aumentar el rendimiento y la fiabilidad de una bomba. El principio de funcionamiento inteligente de un grupo de bombas es sencillo: los sensores y las unidades de control conectados a cada bomba adaptan su forma de funcionar de forma descentralizada, automática y autónoma. Una de las soluciones inteligentes de KSB con mayor éxito es KSB Guard, una solución integral en la nube para monitorizar en remoto grupos de bombas y otros equipos rotativos.
KSB Guard, compuesto por un sensor y una aplicación en la nube, le permite mantener un ojo móvil en los datos de estado de su bomba en todo momento. La funcionalidad de KSB Guard es tan sencilla como eficaz: una unidad técnica (unidad de sensores) instalada en la bomba supervisa regularmente sus valores de temperatura y vibración y envía los datos registrados a la pasarela a través de una unidad de transmisión y batería, conectándola a la nube de KSB. Se puede acceder a los datos medidos y a la información adicional sobre la bomba de forma cómoda y sencilla mediante el portal web o la aplicación de KSB Guard.
A través del portal web o de la aplicación, los operadores no solo controlan las condiciones de carga, los valores de vibración y temperatura de sus bombas, sino que también pueden establecer límites individuales para los valores medidos de cada bomba. En caso de que se produzca un cambio en las condiciones del sistema, KSB Guard informará a los operadores a su debido tiempo, ya sea por correo electrónico o por mensaje push. Con su contador de horas de funcionamiento integrado, KSB Guard puede saber cuándo está a punto de expirar la vida útil de un rodamiento. Además, los operadores del sistema siempre pueden acceder al historial completo de mantenimiento de su bomba a través de la aplicación o el portal web. Aquí es donde se pueden almacenar todo tipo de detalles relacionados con una medida de mantenimiento. Al reconocer las tendencias, los operadores pueden iniciar el trabajo de mantenimiento de un conjunto de bombas en una etapa temprana. Esto facilita la planificación de dichos trabajos, evita el mantenimiento no programado y aumenta significativamente la disponibilidad general de las bombas. Un aspecto práctico: KSB apoya a sus clientes con servicios integrales, como el servicio de piezas de repuesto o la ingeniería inversa.
Caso de éxito InfraServ Wiesbaden (ISW), Alemania
ISW ha estado operando el parque industrial Kalle-Albert de 96 hectáreas desde 1997. 24/7 ISW suministra al parque industrial unos 22.000 m3/h de aire comprimido a una presión de 5 bar. Para vigilar de forma fiable y continua las bombas de agua de refrigeración del sistema de aire comprimido, ISW ha elegido la unidad de monitorización KSB Guard. KSB Guard ofrece a la gestión de producción de ISW y a los técnicos de KSB acceso permanente a todos los datos de estado de la bomba a través del portal web.
Menos mal: en octubre de 2019 se informó de una anomalía en una de las bombas. Cuando KSB Guard detectó vibraciones excesivas y emitió una advertencia relevante, InfraServ Wiesbaden fue informado de forma automática e inmediata. Esto ayudó a ISW a prevenir daños inminentes en los rodamientos en una etapa temprana e iniciar la reparación en su propio taller en un momento en que el funcionamiento de la bomba no era esencial. Si una bomba hubiera fallado repentinamente, se habría activado una segunda bomba para mantener el suministro de aire comprimido. Sin embargo, fue gracias a KSB Guard que se evitó un fallo repentino del sistema con tiempos de inactividad no programados y costes de reparación muy elevados.
En el polígono industrial de Kalle-Albert, en Wiesbaden, KSB Guard detectó altas vibraciones en una de las bombas. Los técnicos iniciaron una reparación durante los períodos en los que el funcionamiento de la bomba no era esencial, evitando un fallo repentino del sistema con tiempos de inactividad no planificados y pérdidas resultantes de gran alcance.
Conclusión:
Cómo el Mantenimiento 4.0 ayuda a simplificar radicalmente el mantenimiento
El uso de sensores inteligentes y tecnologías IoT ofrece nuevas oportunidades para aumentar la OEE, gracias al Mantenimiento 4.0. Porque la maquinaria inteligente prácticamente te avisa cuando su funcionamiento se desvía de la normalidad. El uso de estas nuevas tecnologías es especialmente recomendable cuando se emplean máquinas grandes y costosas durante todo el día y donde los tiempos de inactividad imprevistos pueden tener graves consecuencias. Sin embargo, dados los bajos costes de inversión, la digitalización también merece la pena en sistemas menos complejos.
¿Tiene más preguntas? Esperamos tener noticias suyas. Basándose en su amplia experiencia en la digitalización de componentes de sistemas, KSB se complace en ayudarle a preparar su empresa para el Mantenimiento 4.0.
*https://digital.oup-fluidtechnik.de/o-p-fluidtechnik-4-2016/56531515/18
https://www.industry-of-things.de/amp/wartung-40-senkt-kosten-a-541428/
https://www.yumpu.com/de/document/read/62212195/industrieanzeiger-1118 (Seite 46/47)
Artículos relacionados
KSB Guard
Servicio de vigilancia inteligente e integral para bombas y otras máquinas rotativas: disponible las 24 horas del día, los 7 días de la semana, e independiente del fabricante. Con KSB, se beneficiará de un mantenimiento predictivo y una transparencia total de los datos, así como de mayor disponibilidad, más fiabilidad operativa y un funcionamiento eficiente (de las bombas de velocidad fija). Los datos importantes del funcionamiento, como las vibraciones, la temperatura, las horas de servicio y el estado de carga (de las bombas de velocidad fija) se pueden consultar en cualquier momento y en cualquier lugar con KSB Guard. Si se produce alguna desviación del funcionamiento normal, se envía una notificación inmediatamente a través del portal web o la aplicación KSB Guard. Además, los expertos del centro de vigilancia de KSB le ayudarán a analizar la causa.