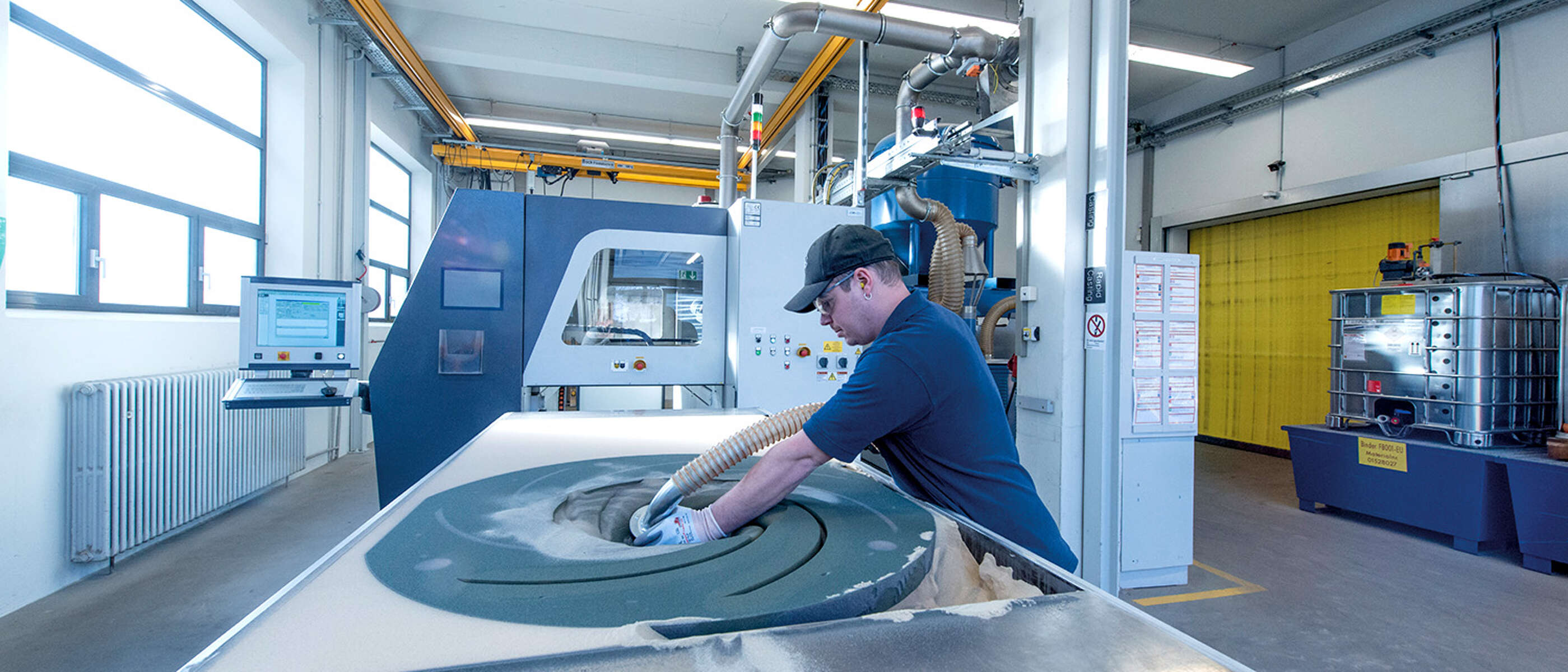
Better than new thanks to reverse engineering
It can be hard to find spare parts for decades-old pumps or valves and sometimes you need a component straight away. In situations like these, the experts from KSB’s reverse engineering team can deliver the solutions you need, promptly and pragmatically.
It can be hard to find spare parts for decades-old pumps or valves and sometimes you need a component straight away. In situations like these, the experts from KSB’s reverse engineering team can deliver the solutions you need, promptly and pragmatically.
New and tougher versions of old and damaged parts
The KSB experts dismantling the pump could hardly believe their eyes. The double-entry impeller was in such poor condition that it was on the verge of complete failure. The impeller surfaces were heavily corroded and its vanes were severely eroded as a result of cavitation. To get the system up and running again, the entire impeller would need to be replaced.
The KSB engineers removed the impeller and got to work. They started by performing a full digital scan to capture as many details as possible. The data collected was used to create a computer-generated virtual 3D model. Missing surfaces were reconstructed by KSB’s highly experienced hydraulics experts. As the system‘s NPSHa value could not be improved, the metal was upgraded from cast iron to stainless steel to provide superior resistance to cavitation and thus a longer service life. Finally, the impeller was manufactured in KSB’s own foundry and was delivered and installed in just four weeks.
Severe damage is clearly visible on the old impeller (left). The new impeller (right) prior to installation in the pump casing.
Tailored production: When reverse engineering can help
The above example is just one of many in which KSB achieved the desired results quickly through reverse engineering. The ability to produce custom components for any kind of rotating equipment is useful in a whole range of situations, including the following:
- A spare part is needed urgently to avoid unplanned downtime and loss of production as a result of protracted delivery times
- A necessary spare part is no longer available, meaning that costly component replacements or even the conversion of an entire system will be required
- Spare parts that are sub-optimal from a materials, hydraulic or design perspective lead to disproportionately high maintenance costs
- Keeping spare parts in stock would involve substantial investments
The benefits of tailored production are obvious:
- Fast manufacturing and delivery in an emergency
- Increased system availability and a longer mean time between repairs (MTBR)
- Lower maintenance and storage costs
- Independence from OEM spare part policies
What components can be manufactured using reverse engineering?
As a leading supplier of pumps and valves, we engineer or optimise almost anything: from entire assemblies to spare parts – including those from other manufacturers. Our portfolio includes centrifugal, reciprocating piston and vacuum pumps, compressors, motors, gearboxes, mixers, fans and valves. We also manufacture cast and machined parts such as casings, impellers, diffusers, shafts, shaft protecting sleeves, casing wear rings, covers, bearing brackets, fan impellers, propellers, end shields, wedge discs, bonnets, seat rings, valve plugs, valve discs, stems, pumps and valves manufactured as replacements and many more.
Materials that meet ASTM specifications
We can process more than 300 alloys in our production facilities. Our foundries are designed for maximum flexibility to support our customers’ changing needs. We are equipped to cast ferrous, non-ferrous, nickel-base and cobalt-base alloys.
- Cast iron and nodular cast iron
- Abrasion-resistant cast iron
- Aluminium alloys
- Copper-base alloys
- Nickel-base alloys
- Austenitic and superaustenitic steel
- Carbon steel and low-alloy steel
- Duplex and super duplex stainless steel
- Martensitic and precipitation-hardening steel
Vacuum pump rotor waiting to be measured and reproduced
How reverse engineering works, step by step
Every task at KSB starts with in-depth customer consultancy. The goal is to recreate – and, ideally, optimise – the parts or pumps with their original fit, type and function. We identify obsolete components and update components or entire pumps to meet state-of-the-art requirements. Upon request, we standardise components to maximise part interchangeability. And we use computational fluid dynamics (CFD) to optimise the pump‘s hydraulic system, resulting in an extended service life and lower energy costs.
1. Precise measurement and digitisation
The geometry of the component to be produced is accurately measured and digitised using precision 3D measuring instruments. All critical dimensions are taken by hand.
2. Creation of a virtual 3D model
The KSB experts then rationalise the data collected into a 3D model. And if necessary, they make metallurgical, hydraulic or design improvements at the same time. Our experts reconstruct any areas that are worn.
3. Moulding and casting or 3D metal printing
Components can be produced using different approaches – as a casting or using the 3D metal printing method. For casting, first the mould is created based on the digital 3D model using a sand printer or conventional patterns. The raw casting is then cast in one of the company‘s own foundries.
Alternatively, we use 3D metal printing : The component is additively manufactured using the laser powder bed fusion process with a state-of-the-art 3D printer. In this process, metallic powder is selectively melted layer by layer using a laser beam. One of the advantages of 3D printing is that it is extremely fast. It also allows the production of complex geometric shapes that would be impossible to create using conventional methods.
4. Final machining
Depending on the part type, final process steps such as machining, balancing and testing are performed before delivery.
Fresh out of the 3D printer at our Pegnitz factory: Metal powder was applied and melted layer by layer using a laser until the components were complete.
Two more reverse engineering success stories
Replacement of an old valve from another manufacturer
The customer needed five new 3-way gate valves with a nominal diameter of DN 300 and nominal pressure of PN 10. The only problem was that the manufacturer of the original valves had gone out of business. KSB experts measured the valves, reproduced them exactly and delivered them promptly. The customer was delighted to be able to continue running the system without the need for structural modifications.
Successful reverse engineering by KSB: An old valve on the left and a new one on the right
A brand new impeller from the 3D printer in just two days
In the course of a planned power plant overhaul, the operator discovered that an auxiliary pump was missing an impeller, which would need to be procured as soon as possible. This constituted an emergency since extending the plant downtime due to a problem with a “minor” component would cost an inordinate amount of money. A sample was sent to KSB, where it was handled as an emergency part in a manual process that prioritises the shortest possible throughput time. The sample was measured and the 3D model was created. The raw part was printed overnight in the 3D metal printer using material 1.4404 (316L). Machining, balancing and all required testing were then completed, before the finished impeller arrived at the power plant by taxi – just 48 hours after the sample was received at the KSB factory. It was possible to install the pump during the scheduled downtime.
Proud colleagues: The printed impeller arrived at the power plant a mere 48 hours after the sample was received at KSB.