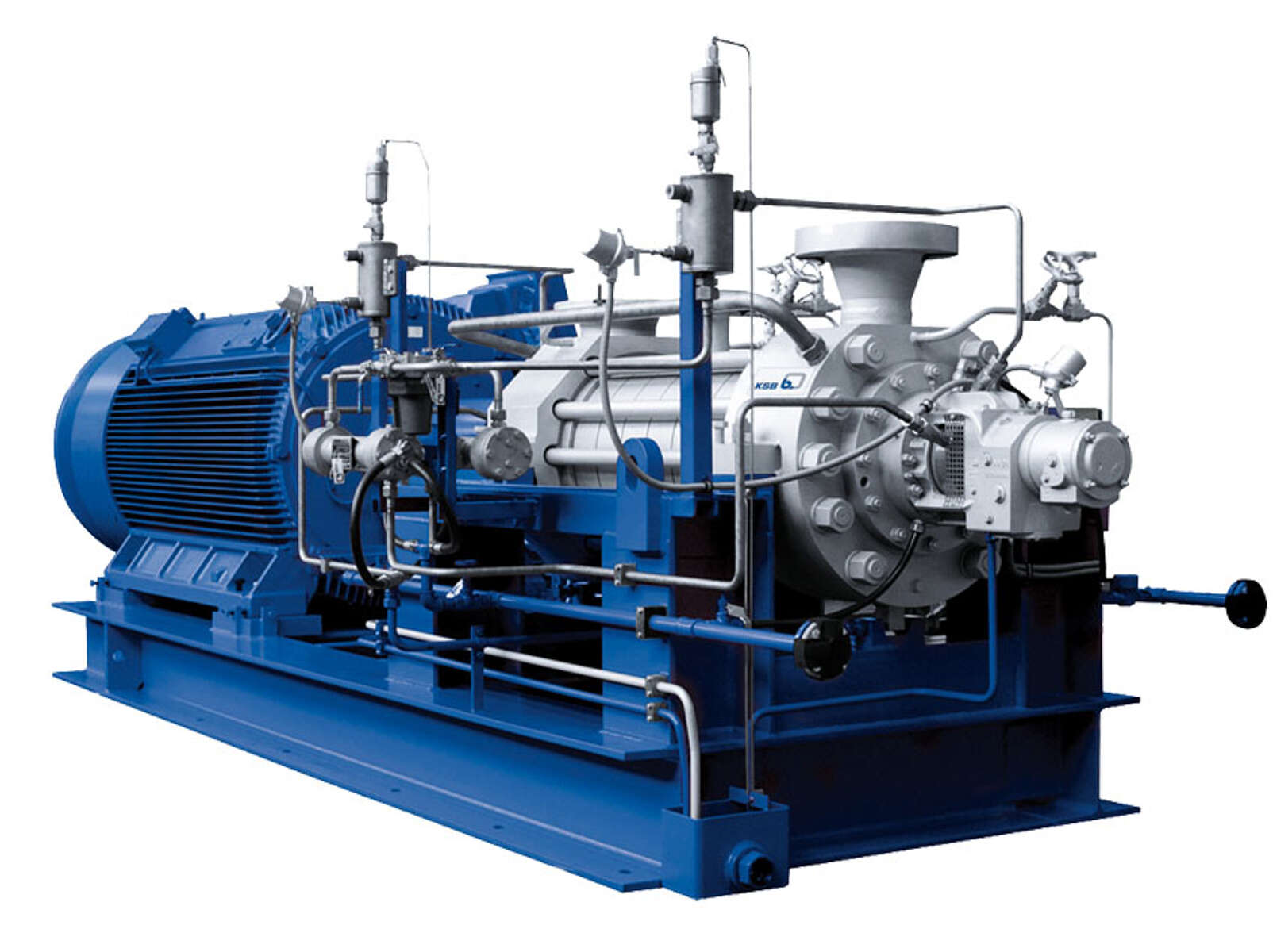
High-Pressure Multi-Stage Pumps: BB3 vs. BB4
High-capacity multi-stage centrifugal pumps are widely used where the delivery of large volumes of high-pressure fluid is needed. This includes providing heated water for SAGD installations in the oilsands, industrial condensate systems, refineries, pipelines and for water desalination by reverse osmosis.
here are a number of basic configurations or layouts for large multi-stage centrifugal pumps. According to the designation system defined in the American Petroleum Institute (API) Standard 610, these are:
BB3 – Axially Split Pumps
In this category of pumps (also known as horizontally split pumps) the casing is made up of lower and upper parts which are bolted together with a number of studs located around the perimeter of the casing (see Figure 1). The shaft and impellers are supported by bearings at the ends of the casing. Typically, the impellers are arranged in two groups, separated by a centre bushing or seal. Impellers in these two groups face opposite directions so that the axial thrust created by the impellers is largely balanced. However, this arrangement means that the internal routing of fluid through the pump is somewhat complicated. Low-pressure fluid enters near one end and then flows through several impeller stages at increasing pressures. The mid-pressure fluid is led through internal passageways to the opposite end of the casing and then through several more impeller stages. High pressure fluid finally emerges near the centre of the machine.
BB3 Axial Split Pump
BB3 pumps are commonly used in oil refinery and pipeline applications, both for water and petroleum products.
BB4 – Radially Split Pumps
Radially split pumps (also known as ring section pumps) are constructed with a number of cylindrical casing sections – one for each stage – which are ‘stacked’ along the length of the shaft and sandwiched between two end pieces. The assembly is held together by a number of high-strength bolts running parallel to the shaft (see Figures 2 and 3). The impellers all face in the same direction so that the flow of fluid through the pump is very simple – in one end, out the other. A single balancing disk compensates for the axial thrust generated by the impellers.
Radial Split Pump
Radial split pumps are used to provide hot, high-pressure water for the recovery of heated bitumen from oilsands through the SAGD process. They are also used widely as boiler-feed pumps, for reverse-osmosis water purification systems and in industrial applications where high temperatures are encountered.
BB5 – Double-Casing Radial Split Pumps
This type of pump – also known as barrel pumps – are basically radially split pumps with an extra cylindrical casing enclosing the ring sections and holding the internal components together. This type of pump was developed largely in response to the perception that ‘ordinary’ radial split pumps could be prone to leakage through the multiple inter-sectional joints. (In practice, KSB – which has over 100 years of experience with this design – has never encountered leakage problems with properly maintained radially-split pumps.)
Features of BB4 Radially Split Pumps
Simplicity and Small Footprint
As noted above, the internal ‘architecture’ of radially split pumps is very simple. Fluid enters at one end through an axial intake nozzle and then passes through the successive stages at increasing pressures. Exit is though a nozzle at the opposite end (see Figure 3). Because of this simplicity, these pumps are relatively compact and easy to position on the plant floor. Plant layout is also simplified, since the intake and output nozzles can be oriented to suit the piping plan.
Radial Split Pump
Rapid Startup
The casings of radially split pumps are much less massive than the casings of axially split pumps of equivalent head and capacity ratings. Moreover, structural elements are arranged in a largely symmetrical manner around the centre of the shaft. Due to these factors, radially split pumps can be started and brought to full capacity with minimal delay, even when the pumped medium is at high temperatures. By comparison, the large mass and complicated shape of the casings of axially split pumps means that these machines must be brought up to temperature slowly to avoid damaging thermal stresses. As a consequence, radially split pumps are much more suited to applications that involve hot media.
Seals
For radially split pumps with an axial intake, only one seal is required at the output/drive end of the shaft. By comparison, axially split pumps require seals at both ends of the shaft, which doubles the possibility of seal failure.
Simplified Maintenance
Well-designed radially split pumps (for example, KSB’s HG family) incorporate features that allow many routing maintenance activities such as seal and bearing replacement be conducted without requiring complete disassembly of the pump casing. In the event that more major repairs are needed, the simple layout of these pumps can reduce the effort required. Consider, for example, a situation where one or more stages of the pump are damaged. Since the casing for each stage is a separate component, repairs can be made by removing and repairing or replacing individual sections and impellers. While this involves a complete disassembly of the pump, most components can remain on-site. For axially split pumps, a major repair to the casing could require that the entire casing be taken to a repair facility.
Efficiency
Thanks to the simpler flow pattern inside radially split pumps, their energy efficiency typically exceeds the energy efficiency of equivalent axially split pumps. (See Figure 4).
Total Efficiency of Multi-stage, Single Entry High Pressure Pumps
Any improvement to energy efficiency is significant since these very large pumps typically consume a significant part of the total energy budget of an industrial facility.
Radially Split Pumps from KSB
KSB was a pioneer in the development of the radially split pump concept and is now a leading supplier of large multi-stage high-pressure pumps based on this design. Here are some examples from KSB’s product portfolio.
HGM Pumps
The development team at KSB Pumps responsible for the HGM pump family looked at every stage of a boiler pump’s life cycle to minimize the cost of installing, operating and maintaining these devices. The result was an extremely compact design, which makes it simple to lay out piping for efficient flows and easy access. Uniquely for pumps in this class the HGM’s bearings are lubricated directly by the water running through the pump. No supply lines, oil pumps and other equipment usually associated with lube oil systems are needed. This reduces both installation and maintenance costs – even to the extent of eliminating the cost of disposing waste oil! The combination of short shafts and closely spaced, medium-lubricated bearings results in very smooth-running, quiet pumps with long service intervals. HGM pumps also feature an axial intake layout and suction impeller, which combine to provide low NPSH (net positive suction head) levels.
HGM Pump
Since the HGM family includes 7 hydraulic configurations, offering flow rates from 10 to 274 cubic metres per hour, and heads up to 1,100 m, it is easy to select a configuration with an optimum duty point matched to the boiler requirements. This helps the pump operate close to its peak efficiency and reduces energy costs. The modular design – combined with KSB Pumps advanced logistics – means that special configurations can be put together quickly and delivered to the customers’ site.
KSB’s HGM pumps are being used in several oilsands project to provide feedwater for the steam flood heaters that generate the high-pressure steam used in the SAGD process. HGM installations can be found in pulp mills, power plants and industrial boilers.
HGB and HGC Pumps
These “big brothers” of the HGM series pumps are used in industrial applications where higher flow rates and head ratings are required. Capacities are up to 1,650 cubic metres per hour, while heads are as high as 4,200 metres! With over 100 impeller/diffuser combinations available, purchasers can find a configuration with a best-efficiency point (BEP) close to the required duty point of the application.
HG Pump
HG series pumps have an outstanding performance record as boiler feed pumps in power plants and as a source of high-pressure water for descaling and tree bark removal applications.
Multitec Pumps
Based on a multistage centrifugal ring-section design, the Multitec family is available in six sizes, with discharge nozzle diameters from 32mm to 150mm. By varying impeller size and the number of stages, KSB engineers can deliver 15 different hydraulic configurations so that designers can select a pump with the optimum rating for their application. (The smallest member of the family has a maximum capacity of 29 cubic metres per hour, while the largest sets can deliver up to 850 m3/hr.) But, scalability isn’t the end of the versatility story. KSB Multitec pumps are available with casings and hydraulic elements made from a variety of materials, including cast iron, bronze, cast steel and high-strength, corrosion-resistant CrNiMo steel alloys. A number of seal configurations are available, with or without cooling, so that the pumps can be used for a wide range of liquids (water, salt water, solvents, lubricants and fuels) and at temperatures up to 200°C.
Multitec Pump
Multitec pumps also offer the designer lots of flexibility when it comes to system layout: vertical or horizontal mounting options are available for most sizes of pumps, as are a variety of nozzle configurations.