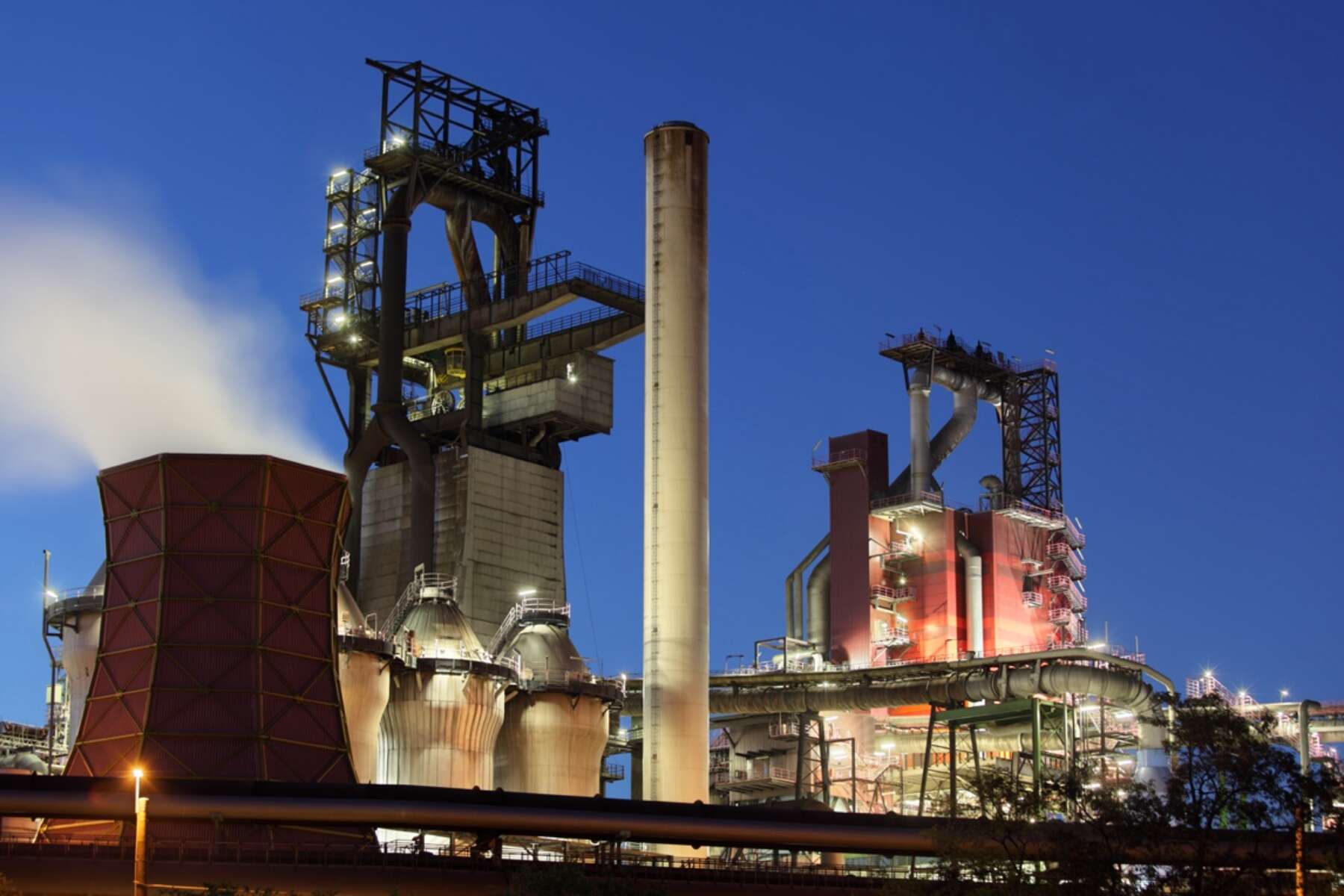
Decarbonisation at a steel producer – with SES System Efficiency Service
Steel production is extremely energy-intensive and therefore also cost-intensive. Understandably, steel producers are keen to identify and exploit potential energy savings in all areas of production. In 2020, a major German steel manufacturer commissioned KSB to analyse its coolant pumps for optimisation opportunities and identify possible courses of action with the help of SES System Efficiency Service.
Steel production is extremely energy-intensive and therefore also cost-intensive. Understandably, steel producers are keen to identify and exploit potential energy savings in all areas of production. In 2020, a major German steel manufacturer commissioned KSB to analyse its coolant pumps for optimisation opportunities and identify possible courses of action with the help of SES System Efficiency Service.
The optimisation
The challenge
Energy savings for cooling water pumps
The SES System Efficiency Service experts were commissioned to analyse the coolant pump system of the rolling mill and to identify options for optimisation.
The SES System Efficiency Service experts were assigned to analyse the cooling water pump system of the rolling mill and to identify options for optimisation.
First, the goals of the analysis were defined:
- Identification of the current pumping behaviour of the pumps
- Assessment of the state of wear
- Checking of vibration levels to DIN ISO 10816 Part 3 and Part 7
- Identification of potential causes of failure
- Propose solutions for more energy-efficient operation of the system while simultaneously increasing system availability
The comprehensive system analysis revealed as below:
- During normal operation the pumps continuously run at low flow – and low efficiency
- Increased pump input power due to visible wear as compared to the as-new condition
- Furthermore, temporary system-induced overload operation of one pump was detected.
The solution
Replacement of the existing oversized pumps with smaller, significantly more energy-efficient models
Based on the analysed data and the boundary conditions (operating hours, load profiles, energy costs, etc.) enquired from the operator, a suggestion for optiminsation including three pumps operating in parallel was developed.
- Replacement of the existing oversized pumps with five Etanorm pumps (drive rating of 132 kW instead of 250 kW)
- Parallel operation of three pumps, two pumps as stand-by pumps
- Piping modifications and replacement of the control valves
Due to the future mode of operation close to the best efficiency point combined with a constant flow rate, this application was deliberately planned without variable speed control.
The result
Pumps optimised for the process flow required, having a payback period of 6 months
This option offers the following advantages:
- Prevention of inefficient low flow operation and operation of the pumps with the best possible efficiency
- Increased service life and fewer unscheduled downtimes
- Prevention of high flow losses at higher flow rates during single-pump operation
- Savings potential of approx. 44.2 % compared to current operation
- Climate protection: Savings of approx. 862 t CO₂ per year
Figures I Data I Facts
Applications: Steel production
Project year: 2020
Scope: Analysis of the pump system for cooling the rolling mill, replacement of five pumps (250 kW, control by throttling)
Existing pumps | Optimised pumps | |
Drive rating [kW] | 5x 250, fixed speed | 5x 132, fixed speed |
Savings | - | 44.2 % |
Energy consumption p.a. [kWh] | 4,115,400 | 2,295,200 |
CO2 emission factor [g/kWh] | 474 | 474 |
Emissions p.a. [t CO2] | 1,949 | 1,087 |
Electricity price [€ / MWh] | 100 | 100 |
Payback period | - | 0.5 years |
Proposed pump models:
5 x Etanorm 125-100-315