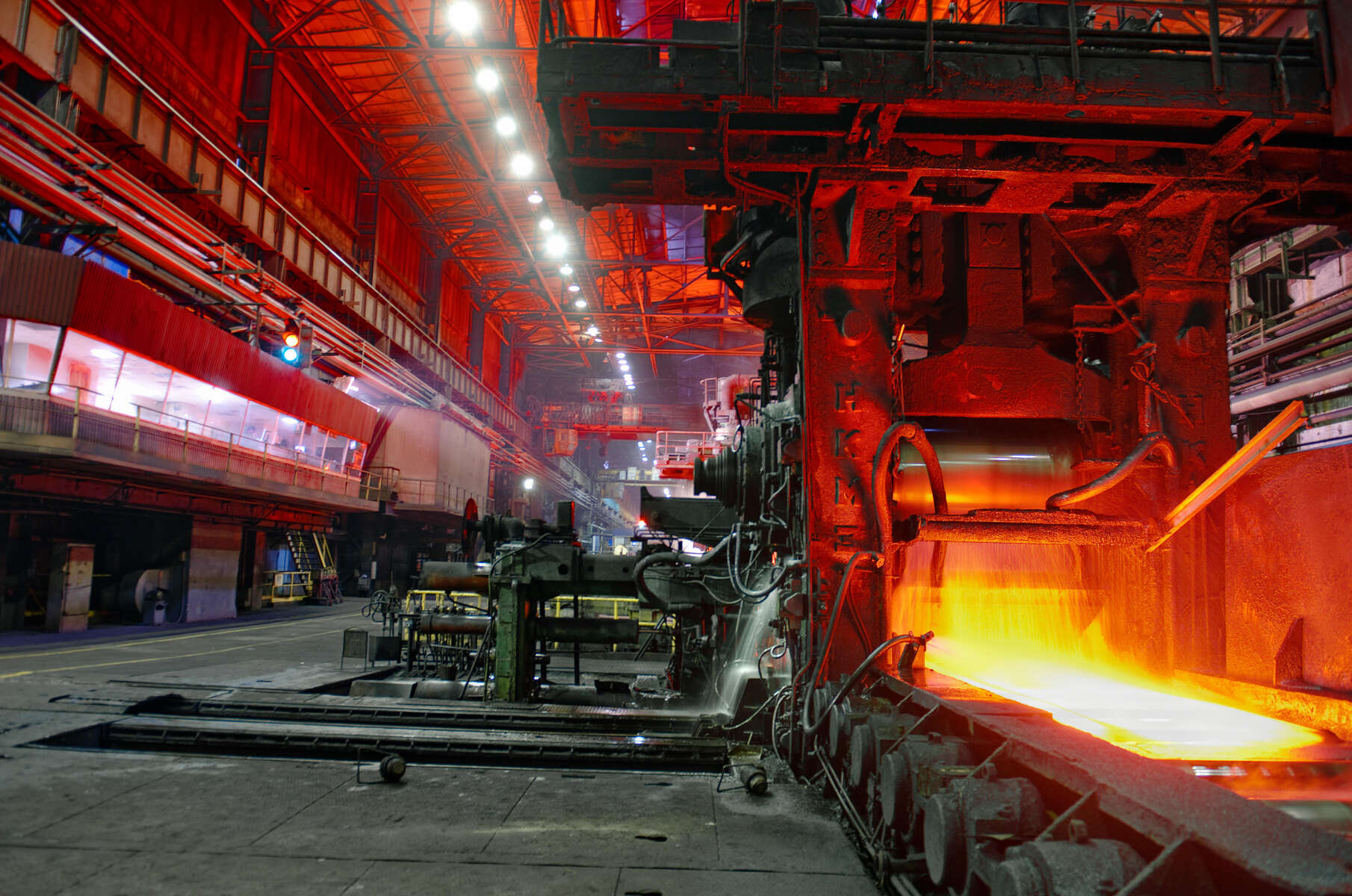
Efficiency optimisation at a steel producer – with SES System Efficiency Service
The production of steel requires a lot of energy. Optimised pump systems can play a significant role in reducing energy costs. For this reason, a large steel manufacturer commissioned KSB to check its pump system for potential energy savings and identify suitable measures that could be implemented.
The production of steel requires a lot of energy. Optimised pump systems can play a significant role in reducing energy costs. For this reason, a large steel manufacturer commissioned KSB to check its pump system for potential energy savings and identify suitable measures that could be implemented.
The optimisation
The challenge
To make the pump system of a very large steel manufacturer more efficient.
On average, the production of one ton of liquid steel requires around 500 kWh of melting energy (from electricity and natural gas). This makes steel manufacturing one of the most energy-intensive of all industries. There is also vast potential for savings in the pump systems used in the manufacturing process. This is because many pumps in the steel industry are not correctly sized, resulting in unnecessarily high energy consumption and carbon footprints.
A large steel manufacturer was aware of this and commissioned KSB to identify the causes for the high failure rate and potential energy savings in its pump system. The SES System Efficiency Service experts began by conducting a comprehensive analysis of the system.
- Identification of the current pumping behaviour of the pumps
- Assessment of the state of wear
- Checking of vibration levels to DIN ISO 10816 Part 3 and Part 7
- Identification of potential causes of failure
- Devise recommendations for action for more energy-efficient operation of the system while simultaneously increasing system availability
The experts discovered a whole series of weak points in the feed water pumps that were having a negative impact on the operating costs and energy balance, ranging from significant wear-induced power losses and acute bearing damage through to high cavitation-induced vibrations (which had already led to pump failures).
The solution
SES System Efficiency Service provides transparency about pump systems and thus improves the carbon footprint.
Fortunately, by choosing KSB, the company opted for a partner with extensive expertise and a broad product portfolio who is not only able to carry out comprehensive system analyses but also to provide suitable measures to remedy these problems and increase the efficiency of the pump system.
Based on the conducted analyses, KSB recommended the following optimisation measures:
- Reduce energy consumption: by reducing the required control pressure and by using variable speed pumps with more efficient hydraulic systems and high-efficiency motors
- Optimise uptime: by sizing the pumps in line with demand as well as intelligent speed control for a mode of operation close to the best efficiency point
In addition, it has been ensured that a sufficient power reserve to cover peak demand is always provided.
The result
More operating reliability, more efficiency – and a payback period of just 1.3 years
The plan is now to implement the measuers for optimisation. KSB installs two new variable speed pump sets and simultaneously increases the maximum flow rate. In addition, a new pump control system is installed. Very conveniently, the modifications are possible while the system is in operation, which means no downtimes.
Just by optimising the existing feed water pump by means of variable speed control, energy savings of over 20% are able to be achieved.
Employing the two new feed water pumps (incl. motors and speed control systems) results in total energy savings of around 60%, which equals approx. 1,250,000 kWh of electricity saved per year.
And the environment benefits too: The carbon footprint can be reduced by 592 tons of CO2 per year thanks to lower energy consumption.
Figures I Data I Facts
Applications: Steel production
Project year: 2021
Scope: Repair and optimisation in terms of speed control of one of the existing pumps and installation of 2 new variable speed feed water pumps
Existing pumps | Optimised pumps | |
Drive rating [kW] | 2x 315, fixed speed 1x 355, variable speed | 2x 250, variable speed 1x 355, variable speed |
Savings | - | 60 % |
Energy consumption p.a. [kWh] | 2,082,000 | 833,000 |
CO2 emission factor [g/kWh] | 474 | 474 |
Emissions p.a. [t CO2] | 987 | 395 |
Electricity price [€ / MWh] | 100 | 100 |
Payback period | - | 1.3 years |