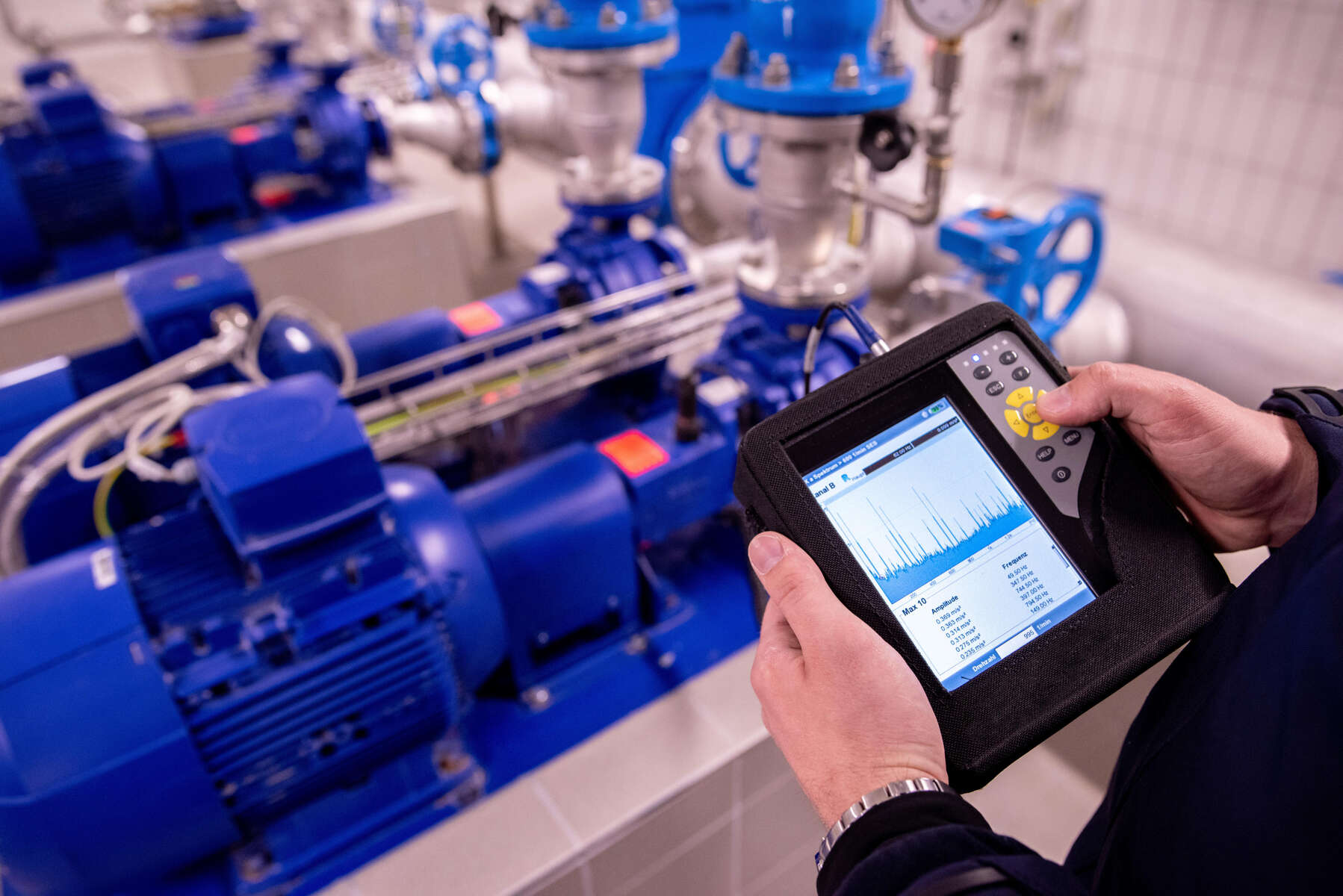
Managing TCO - it’s all about planning
With good planning it is possible to reduce TCO over the working life of the pumping system. There are many ways in which this can be achieved. Matching the pump to the application is all-important. Analyzing pump performance on existing applications, where possible, has to be part of the selection process. Over sizing pumps just to be safe is a common error made by many pump users and is one of the greatest contributing factors to excessive energy consumption.
With good planning it is possible to reduce TCO over the working life of the pumping system. There are many ways in which this can be achieved. Matching the pump to the application is all-important. Analyzing pump performance on existing applications, where possible, has to be part of the selection process. Over sizing pumps just to be safe is a common error made by many pump users and is one of the greatest contributing factors to excessive energy consumption.
How can we improve efficiency?
There is no single solution or answer to improving the operating efficiency of a pump because any number of factors will influence its performance once it has been installed and commissioned. What the pump manufacturer can do is to develop a pumping system that utilizes the optimum number of energy-saving devices and components and also assist the customer in the pump selection and specification process.
Efficiency: Reducing costs while increasing speed and quality. Copyright KSB 2018
Let’s not waste energy
The efficiency of the hydraulic parts has to be matched exactly to the performance required. The impeller diameter is a specific example of a hydraulic element that can influence performance. Oversized impellers waste energy, so trimming the outside of the impeller diameter to the exact flow rate required can yield energy savings of up to 10%. It can also help to reduce maintenance costs and improve longer service life.
Control the speed of your pumps
Then there is the matter of pump speed. Controlling the pump speed offers by far the greatest saving potential, but matching the power input to the actual demand is still far from standard practice. Technology is available to control pump speed exactly to the output that is needed. Using a Variable Speed Drive (also known as a Variable Frequency Drive) provides dynamic pressure compensation, which will deliver extra savings under low flow conditions. Using a throttling valve is another approach. However, variable speed drives can reduce power consumption by up to 60% and KSB’s motor-mounted PumpDrive allows frequency converters to be added and can be retrofitted to existing equipment. For pumps operating continuously, the extra up-front cost of the VFD will be offset very quickly by reduced energy costs.
Efficiency as a Service
KSB’s System Efficiency Services® (SES) offer customers a means of accurately identifying and, ideally, fully utilizing potential energy savings on their pumps and associated systems. SES is a comprehensive program that examines pump performance within the machine’s operating environment. Customers have been able to systematically realize energy saving opportunities to their full potential: savings of 20% - 40% tend to be the norm rather than the exception.
Know your BEP
All pumps have a “best efficiency point” (BEP), this being the combination of developed head and flow volume at which the pump will operate most efficiently. Operating pumps at or near their BEP avoids problems with cavitation or vibration, issues that can cause impeller erosion or accelerated wear to bearings and seals. Selecting a pump set with a BEP close to the system’s required duty point can help reduce long run operating and maintenance costs. Many of KSB’s water pumps are available in a wide range of closely-spaced sizes, making it possible to find a pump with head and capacity characteristics close to the required duty point of the application.
Measuring up with Pump Meter
A proven efficiency service like KSB’s SES makes use of sophisticated measurement and data logging equipment to determine the actual load profile of the pump and to compare this to design conditions. KSB’s Pump Meter measures the suction pressure, discharge pressure, differential pressure and head. Calculating these values produces a pump curve illustrating the operating range and produces a load profile of the pump. From this, the pump manufacturer/ supplier and the user can see if the load profile reveals if the pump is providing cost-saving operation or if its availability is compromised. The effect:
- Potential savings can be identified (energy efficiency analysis) and
- the causes of any damage detected (damage analysis).
In-situ measurements with instruments connected to a data logger create an operating record of process and vibration variables that help determine the operating characteristics of the pump. Using mobile performance measurements in the control cabinet, the effective power of the pump can be determined regardless of where it is located.
Reducing energy costs – tackling the biggest potential
Pumps are components of systems that consume large quantities of electricity, typically around 32% of TCO. This is where there are great savings potential and KSB has identified where these can be made through its “Fluid Future” concept. This global device functions on many levels.
With regard to the drive, the motor of the pumping unit can save about 10%. By working on optimizing the hydraulic efficiency of the pumps, savings can reach 20%. By analyzing and optimizing the entire circuit, the potential can rise up to 60%!
The four phases of System Efficiency Services
- Analysis of the hydraulic system in place and determination of the load profile.
- Selection of the adapted solution (hydraulic, drive, automation) resulting from the collected data.
- Control of the installation and/or commissioning by KSB SupremeServ specialists.
- Equipping the installation with technologies that contribute to the energy efficiency of the installation. Examples would be the KSB SuPremE® reluctance motor (IE5), PumpDrive 2 speed controller, and PumpMeter intelligent pressure sensor.