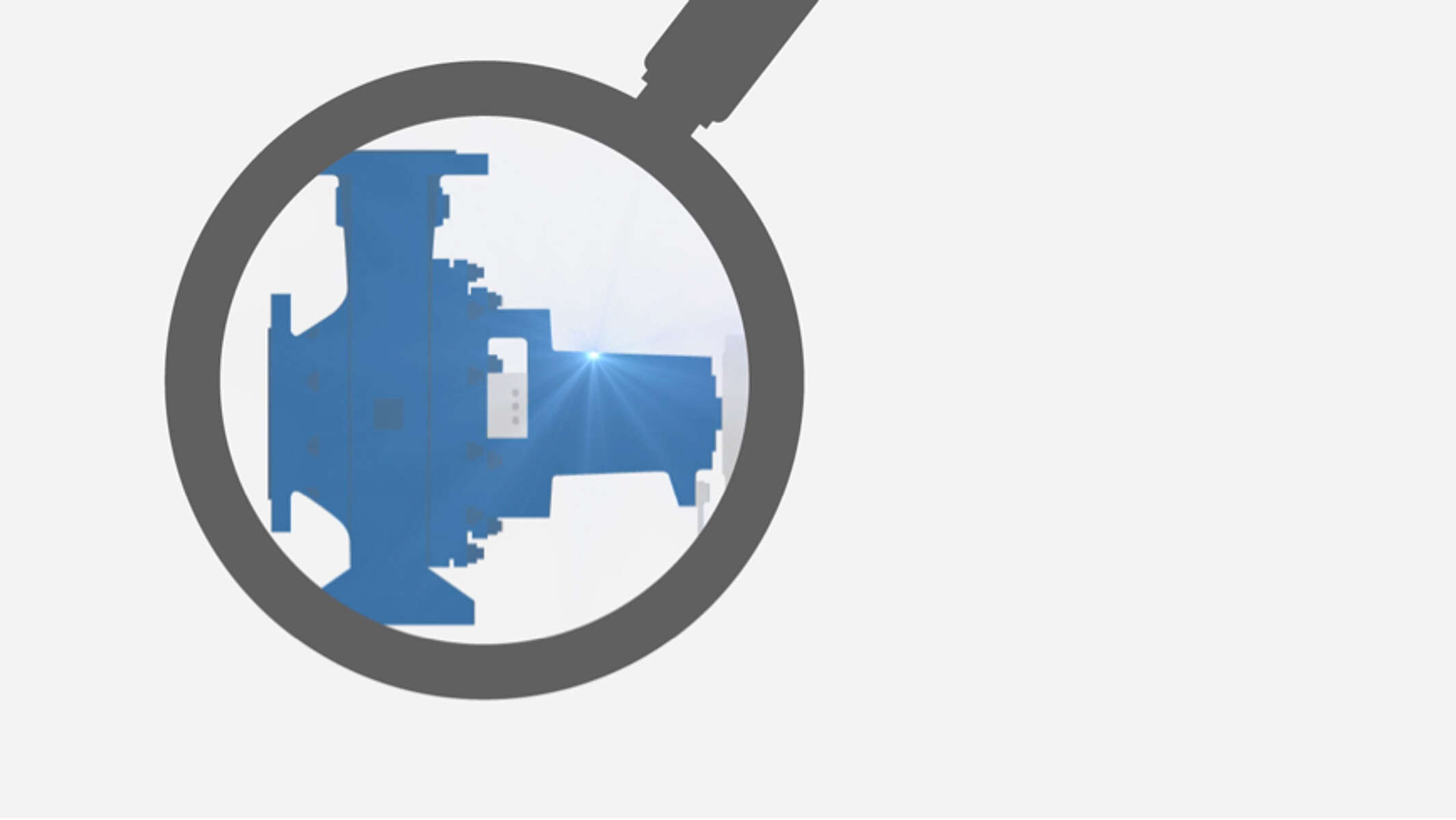
Discover our broad range of upgrade and retrofit solutions for optimising the reliability, availability, flexibility and energy input of your pumps.
Upgrades and retrofit solutions
Discover our broad range of upgrade and retrofit solutions for optimising the reliability, availability, flexibility and energy input of your pumps.
Retrofitting pumps: The smart alternative to buying new products
Upgrade
During repair work, pump components can be modified, replaced or added in order to match your pump better to your requirements. Frequently used measures are the adjustment of the hydraulic system to changed operating data, adaptations to increase the efficiency, retrofitting of sensors for enhanced monitoring or the use of different materials for a longer service life.
A pump upgrade by KSB makes your pump better than new, meeting your exact requirements.
Retrofitting
When your pump has reached its wear limit and replacing it with a current type series would require the system to be modified, KSB offers you tailored solutions: By keeping the same “footprint”, i.e. the mating dimensions of the system interfaces, a minimal shutdown time and cost-optimised implementation without requiring any structural modifications are ensured.
The existing stable infrastructure can thus often be retained. This avoids the high investments that would otherwise be required for modifications to the foundation or piping.
Retrofitting solutions from KSB for your pump will help you to improve your system’s productivity, lower CO2 emissions, reduce maintenance costs, increase production availability and fulfil legal requirements. Transform old into new.