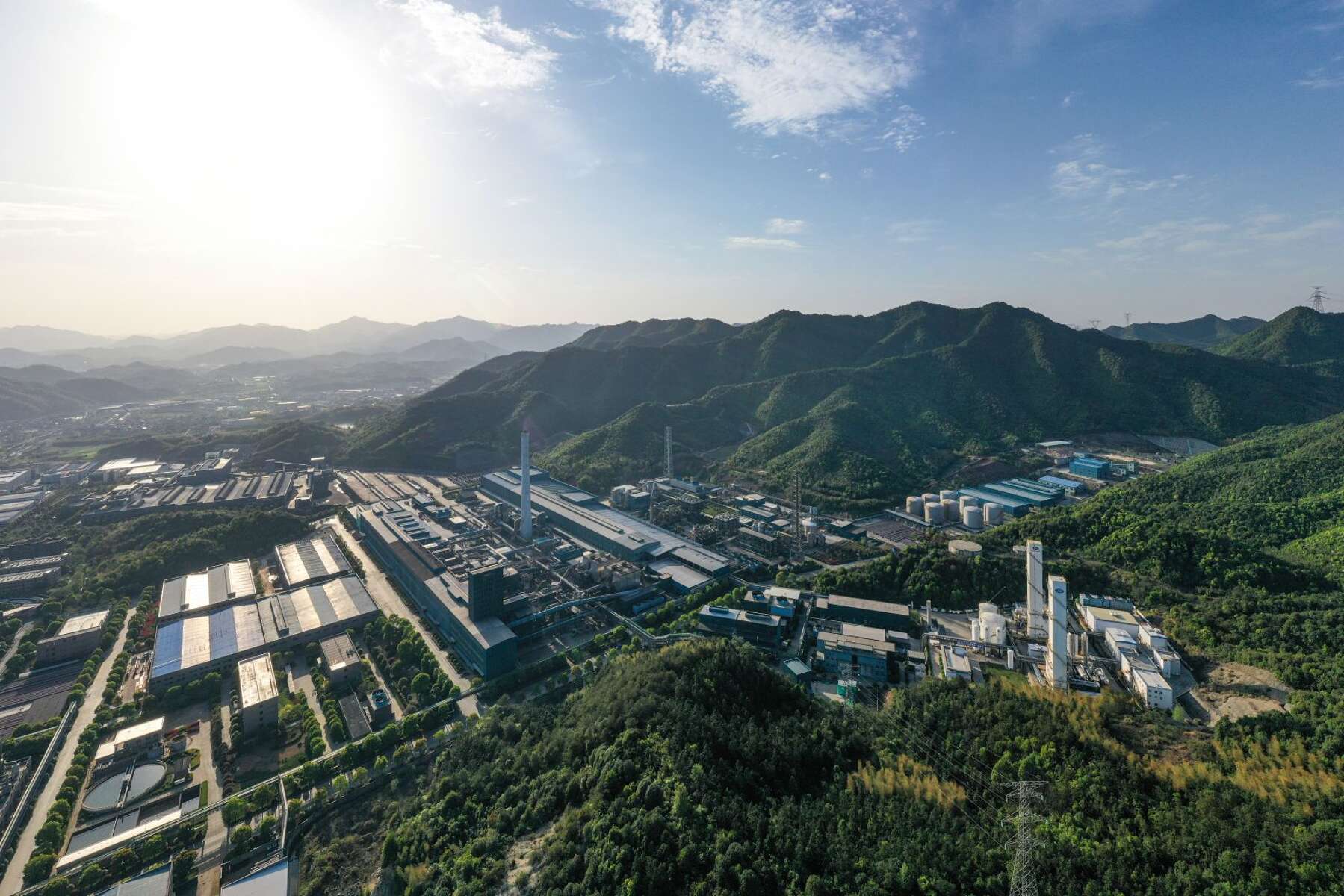
SES in chemical production: full performance, half the energy costs
In Germany, a global manufacturer of different chemical products operates a plant producing synthetic resins and synthetic resin dispersions. In 2022, experts from SES System Efficiency Service were commissioned to investigate the cooling water systems of the two production buildings to uncover potentials for optimisation and find ways of tapping into them.
In Germany, a global manufacturer of different chemical products operates a plant producing synthetic resins and synthetic resin dispersions. In 2022, experts from SES System Efficiency Service were commissioned to investigate the cooling water systems of the two production buildings to uncover potentials for optimisation and find ways of tapping into them.
Optimisation
The challenge:
A system comprising variable speed pumps and fixed speed pumps in two groups
The cooling water system's pump system to be investigated is divided into two groups of pumps that are connected with each other. Pump group 1 is made up of three pumps of the type Etanorm – two of them operated at fixed speed and one at variable speed. Pump group 2 is made up of two Etanorm pumps – one operated at fixed speed and one at variable speed. The pumps are fitted with drives of different sizes, ranging from 30 to 45 kW.
The SES System Efficiency Service experts were commissioned to analyse the system in depth and identify optimisation opportunities.
First, the goals of the analysis were defined:
- Analyse the overall system and identify the overall efficiency
- Create pump characteristic curves incl. the current operating point/range
- Check the power input incl. efficiency
- Recommend actions for operation to be efficient and reliable in the future
The KSB experts conducted a number of measurements at different points, including inlet pressure and discharge pressure, speed, flow rates and other variables. The results revealed:
For normal operation of pump group 1:
- The pumps' flow rate was between 0 and 465 m³/h.
- Control pressure of the collecting line: 5 bar
- The pressure at the hydraulic worst case fluctuates between 0.5 and 3.2 bar.
For normal operation of pump group 2:
- Flow rate between 80 and 200 m³/h
- Control pressure of the collecting line: 6 bar
- The pressure at bad-value point fluctuates between 1 and 4.6 bar.
Also, some problems had occurred in the system: Pressure losses were caused by the check valves installed as they were too small. Some of the motors were running at their ratings limit.
And: Frequent pressure drops were observed, that can be linked to various causes, such as operating a mix of fixed speed and variable speed machinery.
Based on an electricity price of 0.15 €/kWh and the previous operating parameters, the energy costs amount to over € 125,000 per year.
Easy to recognise: on the left, pump group 1 with 2 Etanorm pumps; on the right, pump group 2 with 3 Etanorm pumps.
The solution:
Upgrading the system and using new, variable speed motors
KSB's experts prepared the following optimisation concept for the customer:
- Increasing the pipe diameter between pump and collecting line to DN 150
- Replacing the current swing check valves and changing their installation position
- Using pumps with impellers of maximum impeller diameter
- Using new motors with frequency inverters of at least 45 kW for three of the five pumps
- KSB's engineered pump control system incl. frequency inverter, PLC with KSB software module for optimum pump operation
Performance measurements in the control cabinet
The result:
An efficient and reliable system with reduced CO₂ emissions
The customer decided to implement the suggested measures and now benefits from the following:
- In single-pump or dual-pump operation all operating points of PG 1 are covered in an energy-efficient manner.
- A higher pressure is available in the system, and one pump is always on standby.
- All operating points of PG 2 can now be covered by a single pump.
- Speed control enables operation over the entire system curve.
- A higher pressure is available in the system, and one pump is always on standby.
- In conclusion: higher system availability at constant pressure for all consumers
- Significant reduction of life cycle costs
- Massive energy savings equalling close to 50 %
- Marked reduction of CO₂ emissions (almost 150 tonnes per year)
- Plus a clearly enhanced operating reliability
Energy savings compared to current operation: almost 50 % equalling € 59,100 per year
Figures I Data I Facts
Application: Chemical industry
Project year: 2021
Scope: Investigating the pump system for cooling water supply
Prior to | After optimisation | |
Energy consumption [kWh/a]1,2 | 835,500 | 441,500 |
Energy costs [€/a]1,2 | 125,300 | 66,200 |
Cost savings [€/a]2 | 59,100 | |
Savings potential [%]2 | 47.2 | |
CO₂ emissions [t/a]1,2 | 306 | 162 |
Reduction of CO₂ emissions [t/a]2 | 144 | |
Payback period [a] | 1.7 years (PG 1) |
1 Based on an energy purchase price of 0.15 €/kWh
2 Production buildings 1 and 2 together