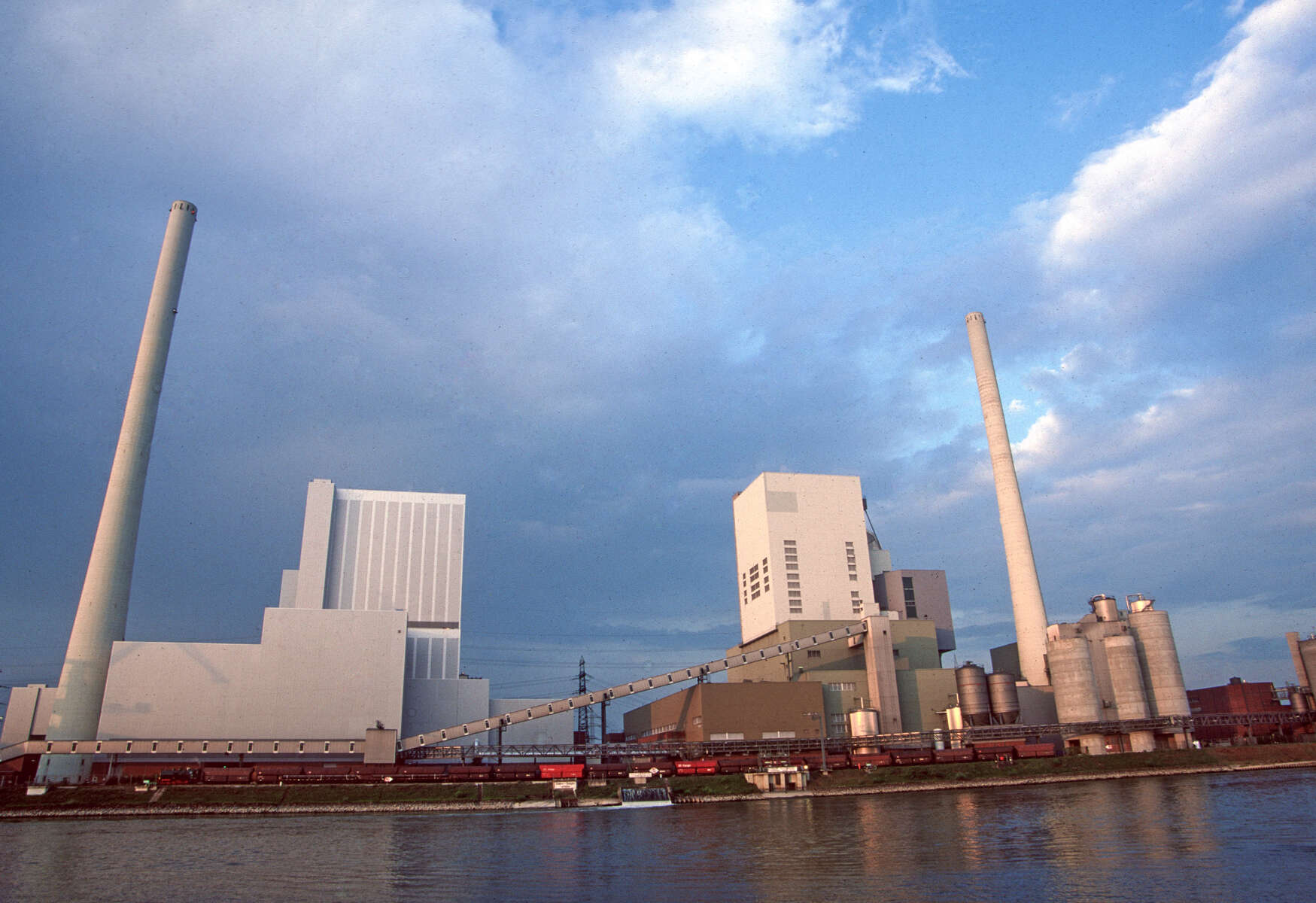
High performance in major power station: a reportage
Today's fossil-fuelled power stations need to be highly efficient as well as flexible. This requires high-performing valves which are resistant to extreme conditions. For these exact requirements, KSB has developed new high-performance valves, which have passed the acid test in the Großkraftwerk Mannheim power station. Two KSB engineers accompanied the project right from the start.
Today's fossil-fuelled power stations need to be highly efficient as well as flexible. This requires high-performing valves which are resistant to extreme conditions. For these exact requirements, KSB has developed new high-performance valves, which have passed the acid test in the Großkraftwerk Mannheim power station. Two KSB engineers accompanied the project right from the start.
"I have got my roots here at KSB," laughs Georg Bode, a mechanical engineer who has been working for KSB for 27 years. Here, at the Pegnitz site, he passed his initial training as a machine fitter. In the last ten years his main focus has been on valves, and since 2007 he has been working on a very special project: His team in Pegnitz, KSB's Bavarian site, has been developing new high-performance valves for fossil-fuelled power stations. These valves are able to handle high steam temperatures – making power stations ready for the future.
New challenges for fossil-fuelled power stations
The background: Operators of fossil-fuelled power stations are facing some demanding challenges. Their power stations need to be operated more efficiently and effectively – while keeping CO2 emissions to a minimum. To be able to respond swiftly to the fluctuating demand in power supply, the operation of power stations needs to be flexible. It is especially this flexible operating behaviour which requires extraordinarily high-performing valves which can handle such extreme conditions. The team developed two prototypes for this scenario – a high-pressure globe valve and a high-pressure gate valve. These were initially used for trial in a separately installed test loop in the Großkraftwerk Mannheim power station.
The valve is being tested in a separately installed test loop at the Großkraftwerk Mannheim station.
"We employed a new material especially adapted to the specific requirements of the high temperatures that occur in a power station," explains Roland Schmitt. The mechanical engineer joined the team in 2009, where he has been involved in designing the new high-performance gate valve. Its main components are made of nickel base alloy 617. Thermal stress is reduced by the newly developed gate valve's spherical body of homogeneous wall thickness.
On site, in the power station
The two prototypes were in service in the Mannheim power station for about two years, facing temperatures of up to 725 °C. Georg Bode and Roland Schmitt accompanied the project at the site. "It is exciting to observe first-hand how a valve copes with certain conditions," says Mr Bode. "This is where theory meets practice. It is also an opportunity for us to look at the project from different angles."
In Mannheim, the two KSB engineers not only worked closely with the power station operators but also with institutes such as the German Association for Technical Supervision TÜV, the materials testing institute and other companies involved. Stuttgart University also participated in the project. "Experiencing different perspectives was an interesting and useful aspect," reports Roland Schmitt. "Our challenge was to find a solution that took everything into account and to jointly work towards making this project a success."
Passed with flying colours
After the initial testing phase in the large power station the engineers were eagerly awaiting the outcome: Did the metal sealing elements handle the conditions? How did the extreme heat in the power station affect the material? After the valve was completely dismantled and inspected, the answer was clear: "The internal parts were free from any signs of wear," says Mr Bode. "Naturally, we were delighted about such a positive result."
Both the globe valve and the gate valve passing two years of service in the Großkraftwerk Mannheim without any functional faults is a major success and a good basis for developing the valve further at KSB. Georg Bode and Roland Schmitt will definitely continue their involvement also in this next phase.