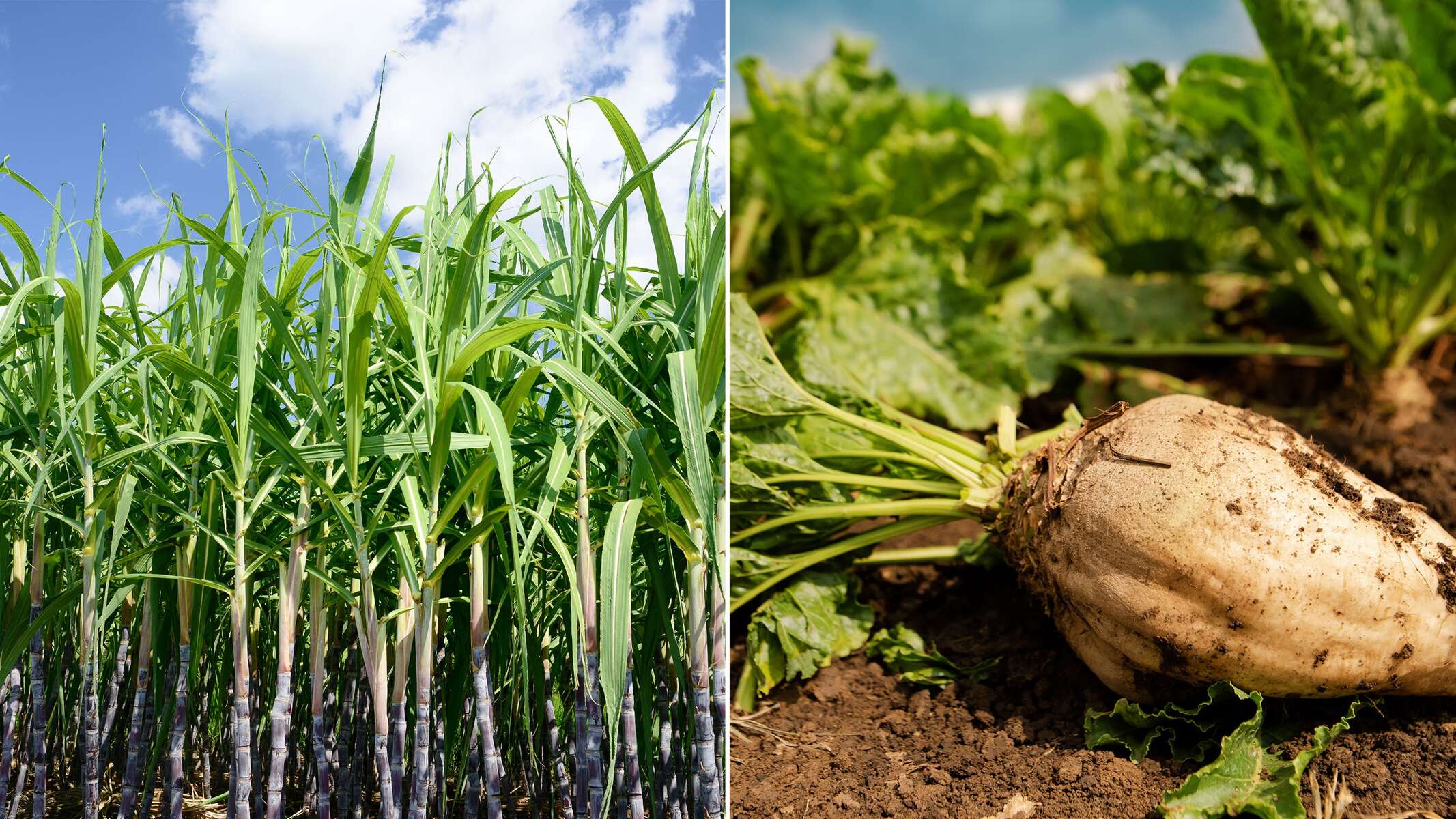
Pumps for sugar production and starch production
KSB offers all pumps and valves required for this sector – for both core and auxiliary processes.
Thanks to many years spent developing expertise in products and processes, KSB is on hand to offer the right pumps and valves for every step of the sugar and starch production process.
From beets to finished sugar: KSB offers pumps and valves for sugar production
Sugar production begins with the sugar beet harvest – it usually starts in mid-September and lasts 80 to 110 days. During this period, production needs to run as smoothly as possible so as not to bring the entire sugar production process to a standstill. And in case of a failure, service and spare parts must be available promptly.
Sugar production comprises a wide range of different fluid handling processes including pumping the cossette/juice mixture to the extraction tower and transporting sugar crystals dissolved in water. These complex processes require individual system solutions, and above all advanced products featuring optimised technology.
Many KSB components can be specifically adapted to meet the requirements of these applications. The KWP volute casing pump for example can be selected in special materials suited to handling abrasive media such as milk of lime, filter sludge or contaminated wash water. KSB also provides mechanical seals (including supply systems) specially designed and manufactured in-house for use with the KWP and other type series including Etanorm and MCKP.
KSB can thus offer the right pumps and valves for every aspect of sugar production – from beet washing to extraction and crystallisation.
From sugar beet juice to crystalline sugar: KSB offers solutions for every stage of production.
Whether for food or industrial applications: KSB offers high-performance pumps and valves for starch production.
Depending on region and climate, starch can be obtained from corn, potatoes, wheat, peas or even cassava. But no matter which plant serves as the raw material, KSB offers the right solution for every starch production application – a major plus for OEMs offering multiple systems for different starting materials.
Starch production is a global growth market. The market is not limited to hygienic starch production for the food industry: Other large-scale applications requiring so-called technical starch range from building material and cardboard production to the textile industry, cosmetics and pharmaceuticals.
KSB’s advantage: As a full-range supplier, it has the right products and service solutions for all applications and every stage of production.
KSB provides all of the products and services you need from a single source
At KSB, years of expertise in products and processes are combined with a broad range of products and services. The result: KSB supplies not only all pumps and valves required for core processes, but also those for peripheral systems, i.e. the auxiliary processes in sugar and starch production.
Many components can be specifically adapted to individual requirements – for example, the KWP volute casing pump is available in multiple material variants for use in core processes involving abrasive media such as milk of lime, filter sludge or contaminated wash water. In addition, KSB mechanical seals specially matched to application and pump type ensure long service lives.
These benefits are rounded off by KSB’s global service network. Here, more than 3000 specialists in over 170 service centres are available at short notice for maintenance, servicing and repairs.
KWP
Horizontal radially split volute casing pump in back pull-out design, single-stage, single-entry, available with various impeller types: closed multi-channel impeller, open multi-vane impeller and vortex impeller. ATEX-compliant version available.
MegaCPK
Horizontal radially split volute casing pump in back pull-out design, with radial impeller, single-entry, single-stage, to DIN EN ISO 5199, dimensions to DIN EN ISO 2858, complemented by nominal diameters DN25 and ≥DN200, in large range of material and seal variants; also available as a variant with "wet" shaft and conical seal chamber. ATEX-compliant version available.
Vitalobe
Sturdy rotary lobe pump in hygienic design, bi-directional operation possible, horizontal or vertical orientation of connections. Hygienic design, excellent CIP/SIP compatibility due to its almost complete lack of dead volume or narrow clearances. All wetted components made of 1.4404/1.4409 (AISI 316L/CF3M) stainless steel; various rotor types, shaft seals and process connections available. Installed as a pump set with gear unit and standardised motor. Vitalobe is EHEDG-certified. The pump elastomers comply with the FDA standards and EN 1935/2004. Accessories include a trolley, a heatable casing or casing cover and a pressure relief arrangement. ATEX-compliant version available.
Multitec
Multistage horizontal or vertical centrifugal pump in ring-section design, long-coupled or close-coupled, with axial or radial suction nozzle, cast radial impellers and motor-mounted variable speed system. ATEX-compliant version available.
Amarex KRT
Horizontal or vertical single-stage submersible motor pump in close-coupled design, with various next-generation impeller types, for wet or dry installation, stationary or transportable version, with energy-saving motor and models for use in potentially explosive atmospheres.
ISORIA 10/16
Centred-disc butterfly valve with ISO 5211 compliant square shaft end, sealed by elastomer liner, with lever or manual gearbox, pneumatic, electric or hydraulic actuator. Wafer-type body (T1), semi-lug body (T2), full-lug body (T4) or U-section body with flat faces (T5). Body types T2 and T4 are suitable for downstream dismantling and dead-end service with counterflange. Connections to EN, ASME, JIS.
DANAÏS 150
Double-offset butterfly valve with ISO 5211 compliant square shaft end, with plastomer seat (also in fire-safe design), metal seat or elastomer seat (FKM [VITON R] or NBR [nitrile]). Lever or manual gearbox, pneumatic, electric or hydraulic actuator. Body made of nodular cast iron, cast steel, stainless steel or duplex stainless steel (254 SMO). Wafer-type body (T1), full-lug body (T4), T4 suitable for downstream dismantling and dead-end service with counterflange. Connections to EN, ASME or JIS. Fire-safe design tested and certified to API 607. Fugitive emissions performance tested and certified to EN ISO 15848-1. ATEX-compliant version in accordance with Directive 2014/34/EU.
MIL 21000
Top-guided single-ported heavy post-guided control valve for a wide temperature range.