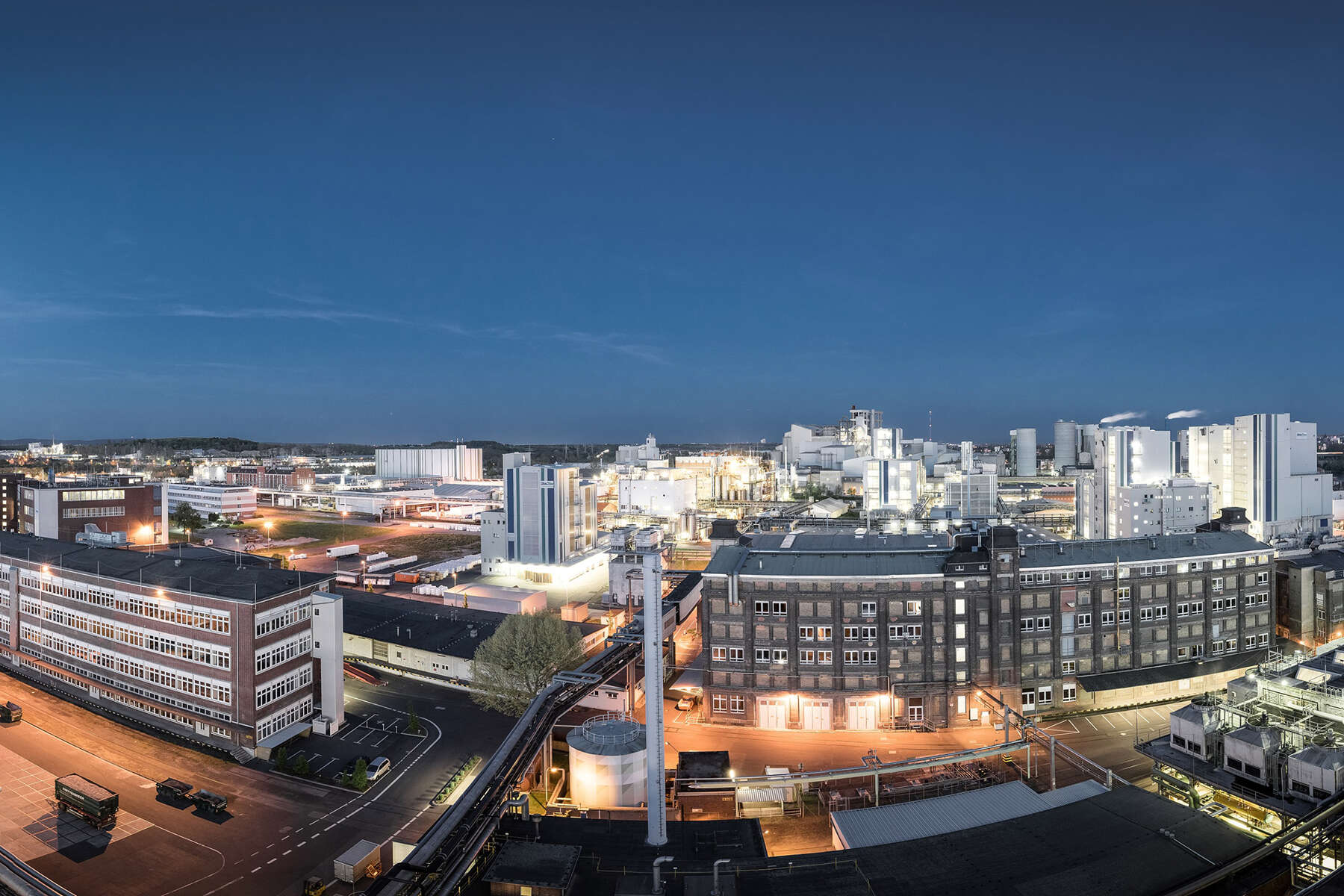
Predictive maintenance at the Kalle-Albert Industrial Park
75 different companies are located at the Kalle-Albert Industrial Park employing a total of around 6000 staff. A reliable supply of compressed air used for the mechanical control of large production systems is a technical requirement for numerous production plants. Failure of the compressed air supply would have serious consequences – and this is a good reason to ensure that impending changes in status data and potential faults are detected before they actually occur.
The project: Reliable monitoring of the cooling system
In the scope of the Industry 4.0 concept, ISW-Technik, a subsidiary of industrial park operator InfraServ Wiesbaden (ISW), uses innovative technologies to implement smart servicing and maintenance processes based on digital condition monitoring of machines and systems for small and medium-sized companies. Predictive maintenance has also achieved positive results indicative of future success. Late 2019 saw digital technology secure the production of compressed air essential for the industrial park and prevent the failure of an important pump used in this process.
The customer: InfraServ Wiesbaden
InfraServ Wiesbaden (ISW) has been operating the 96-hectare Kalle-Albert industrial park since 1997 and provides various utilities including power. The company employs about 900 people. Its subsidiary ISW-Technik has established itself among small and medium-sized companies based in the Rhine-Main region as an innovative service provider for applications including servicing and maintenance of machines and systems.
The challenge: Ensuring round-the-clock system availability
InfraServ Wiesbaden ensures that the industrial park is supplied with compressed air around the clock, providing about 22 thousand cubic metres of compressed air per hour at a gauge pressure of 5 bar which adds up to about 200 million cubic metres per year. ISW relies on two KSB components to keep the vital compressed air system running reliably and to cool the operating temperature continuously: Etanorm pumps and the reliable KSB Guard monitoring unit.
Having already had positive experience with KSB during previous projects, ISW was curious to see how the newly established system would prove its worth in this case. KSB Guard offers ISW production management and KSB technicians round-the-clock access to all pump status data (e.g. temperature, vibrations and load condition) via a web portal.
KSB Guard installed on a KSB pump
The solution: KSB Guard detects bearing damage at an early stage
A deviation from normal operation was reported on one of the pumps in October 2019. After KSB Guard had detected excessive vibrations and output a relevant warning, InfraServ Wiesbaden was informed automatically. Thanks to KSB Guard, ISW-Technik was able to detect impending bearing damage at an early stage – a normal sign of wear that makes bearing replacement necessary at varying intervals depending on the pump’s load.
ISW-Technik initiated a repair in its own workshop during periods when pump operation is not essential. This helped prevent in time a sudden system failure with unplanned downtimes and far-reaching resultant losses. If one pump had suddenly failed, a second pump would have cut in to maintain the production of compressed air. Nevertheless, the advantages of targeted and predictive maintenance measures are tremendous.
KSB technology has not only helped to increase the safe and reliable supply of energy at the industrial park, this positive experience has also prompted ISW-Technik to install KSB Guard on other customers’ systems located in the industrial park.
Vibration profile recorded by KSB Guard indicating a deviation from normal operation
Figures I Data I Facts
System: Cooling system for compressed air supply in the Kalle-Albert Industrial Park
End user: InfraServ Wiesbaden
Project:
- 2x Etanorm 200-150-400
- 2x KSB Guard
- 1x KSB Guard Gateway
Products used
Etanorm
卧式蜗壳泵,单级,额定功率和主要尺寸符合 EN 733 标准,带轴承托架,背抽式设计,带可更换轴套/轴护套和泵体密封环,带电机安装式转速调节系统。带能效等级为 IE4/IE5(依据 IEC TS 60034-30-2:2016 标准)的无磁体同步磁阻电机 KSB SuPremE(例外:尺寸为 0.55 kW/0.75 kW、转速为 1500 rpm 的泵带有永磁体),配合无转子位置编码器的 KSB PumpDrive 2 或 KSB PumpDrive 2 Eco 转速调节系统运行。固定点符合 EN 50347 标准,外壳尺寸符合 DIN V 42673 (07-2011) 标准。可选购 ATEX 型式。