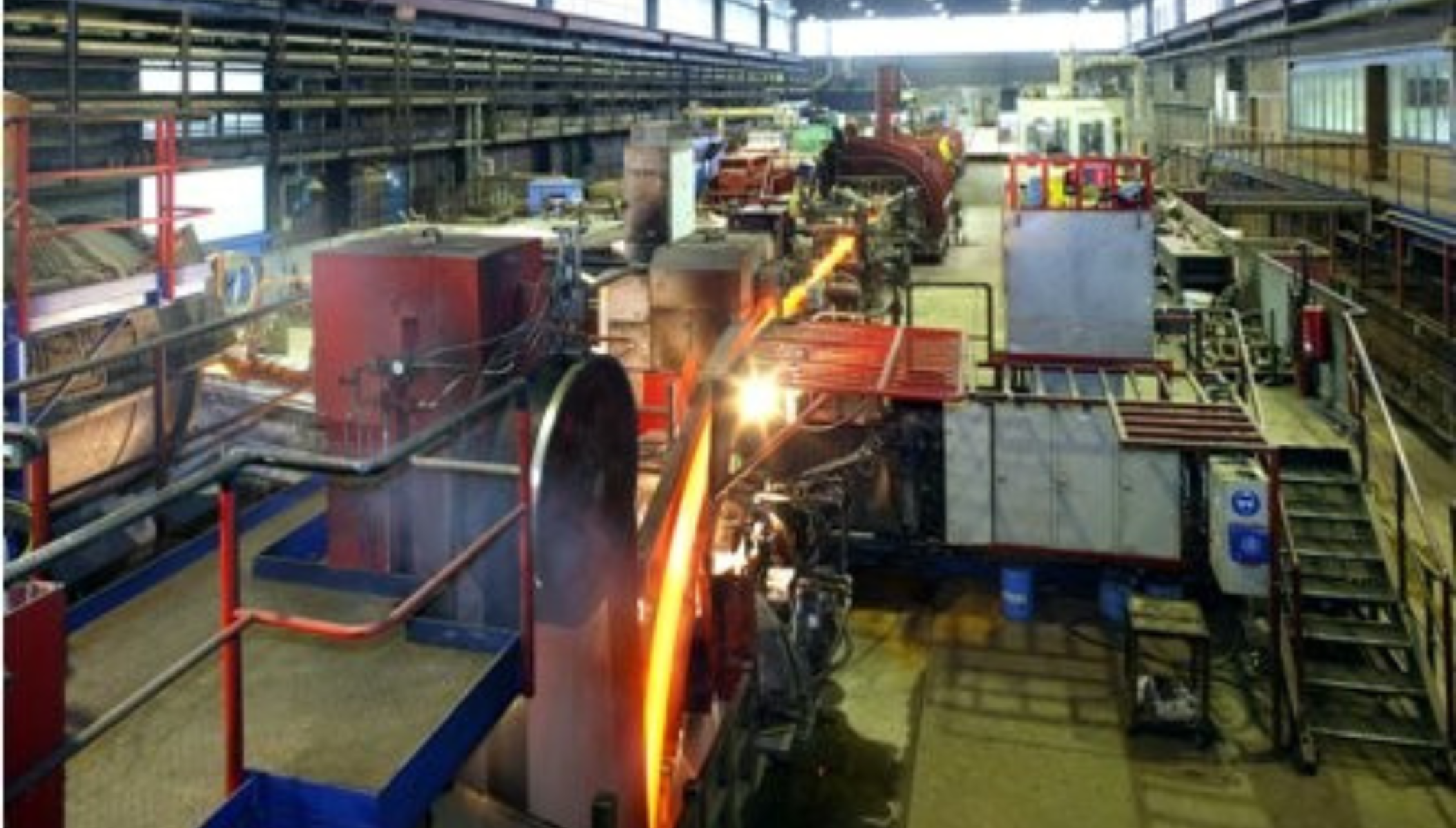
Controlo de bombas em sistema de captação e arrefecimento
Estudo de caso em fábrica de fio de cobre
O processo produtivo
A Deutsche Giessdraht é uma das empresas líder de mercado no fabrico de fio de cobre fundido de alta qualidade, e está sediada em Emmerich, no vale do Reno. Na sua fábrica de Emmerich, a empresa fabrica cerca de 257 mil toneladas de fio de cobre por ano, de diâmetros entre 8 e 16 mm, que exporta para todo o mundo. Como matéria-prima são utilizados cátodos de cobre produzidos por electrólise. Depois da fusão, o cobre líquido é fundido continuamente numa barra única à temperatura de 1.110 °C, através do processo chamado “Southwire”, que inclui uma roda de fundição.
Depois, num processo a alta temperatura, é dada à barra a forma de fio, num laminador de rolos. Devido ao facto do cobre estar no estado líquido e, por isso, extremamente quente, no início do processo de fabrico, os passos seguintes exigem um sistema de arrefecimento altamente fiável e eficiente.
A fábrica tem de eliminar cerca de 800 MJ de calor por ano ! A qualidade do fio fabricado depende muito de um controlo muito preciso do processo de arrefecimento, e da consequente precisão do cálculo do volume de água de arrefecimento. Devido ao dramático aumento do preço da electricidade, a eficiência do sistema de arrefecimento é agora mais importante que nunca. No entanto, o objectivo de todas as melhorias técnicas na fábrica é – em primeiro lugar e acima de tudo – aumentar a sua disponibilidade e, em simultâneo, manter a temperatura da água de arrefecimento sempre constante.
O sistema de captação e arrefecimento
Aproveitando a localização da fábrica, é utilizada água do rio Reno para arrefecimento (Fig. 2).
Fig.2: Localização da fábrica, junto ao rio Reno
O sistema de captação de água do rio é composto por dois ramais e três bombas de captação, instaladas na bacia de entrada das docas do Reno, depois existem três bombas de água de arrefecimento para o processo produtivo e uma única bomba auxiliar (ver esquema na Fig. 3).
Fig.3: Esquema hidráulico do sistema de arrefecimento
No seu caminho para a bacia de entrada, a água do rio atravessa uma grelha de filtragem; a partir daí é bombeada para um grande reservatório de água de arrefecimento, através de uma grelha móvel. O reservatório tem dois objectivos: como fonte de abastecimento de água e para misturar as várias entradas de água a uma temperatura constante. A partir do reservatório várias bombas fornecem água de arrefecimento à fábrica. As mudanças de temperatura e de nível da água ao longo do ano dificultam a manutenção da temperatura da água a um valor constante, necessário ao processo de arrefecimento. A temperatura da água de arrefecimento e a velocidade de produção são factores chave no processo de solidificação da roda de fundição e, consequentemente, na qualidade da microestrutura do fio de cobre, a qual por sua vez é decisiva para a qualidade do produto final. Os melhores resultados são obtidos com água de arrefecimento a uma temperatura de 21 °C. Ao mesmo tempo, a pressão da água de arrefecimento tem de ser mantida a uma pressão constante de 4.5 bar, para garantir que os aspersores de arrefecimento fornecem o caudal de arrefecimento adequado. Além disso, os regulamentos de protecção do ambiente das autoridades locais exigem que a água seja bombeada de volta para o rio à uma temperatura igual ou inferior a 30 °C.
O sistema de controlo
Para garantir que fossem cumpridas todas as exigências do sistema, foi necessário instalar um sistema de controlo de última geração. Para resolver os problemas da flutuação do consumo do processo produtivo e da variação das condições de captação de água (em termos de temperatura e pressão), e para garantir o menor consumo energético possível, todas as bomba foram equipadas com variadores de frequência. Todas as bombas são do tipo submersível com camisa de arrefecimento, do modelo Amarex KRT, fabricado pela KSB (Fig. 4).
Fig.4: Bomba submersível com camisa de arrefecimento, modelo Amarex KRT
Como as condições de produção variam muito, também o caudal de água necessário tende a oscilar bastante, fazendo variar os pontos de funcionamento das bombas com enorme frequência. Para dificultar as coisas ainda mais, o circuito de águsa de arrefecimento não pode afectar o sistema central de controlo do processo. Para o garantir foi decidido desenhar o sistema de água de arrefecimento, totalmente automático, como um sistema de controlo autónomo com circuito fechado, totalmente independente. As interfaces com o sistema de controlo do processo fabril só servem para troca de dados. Para permitir um funcionamento mais eficiente do controlo contínuo da velocidade, o sistema é composto por dois circuitos fechados, com dois sub-sistemas de controlo da velocidade das bombas, modelo Hyamaster SPS, da KSB (Fig. 5).
Fig.5: Sistema de controlo da velocidade das bombas, modelo Hyamaster SPS
Um dos sistemas é dedicado às bombas de captação, P1 a P3, o outro às bombas de água de arrefecimento, P4 a P6. Os dois sistemas têm uma construção modular, no que respeita ao hardware e software. Os circuitos fechados e abertos são controlados a partir de uma unidade PLC. Para além disso, todas as bombas são monitorizadas e todos os sensores têm redundância. No entanto, em caso de emergência, os operadores também conseguem intervir manualmente nos processos. O caudal de água captado do Reno é calculado em função da curva característica da bomba, considerando ainda parâmetros como potência absorvida, frequência e pressão diferencial. Como este caudal nunca ultrapassa o caudal necessário para arrefecimento, os custos com a água e com a electricidade têm diminuído consideravelmente.
O dimensionamento das bombas
O projectista calculou as alturas manométricas das bombas com extremo cuidado, para evitar margens de segurança desnecessárias, que teriam sobredimensionado a bomba sem necessidade. Quando se seleccionaram as bombas comparou-se continuamente os rendimentos das curvas de velocidade com o perfil de carga da instalação, o que permitiu obter o máximo rendimento total ao longo do período em análise. Foi ainda possível reduzir a potência absorvida pelas novas bombas de 90 para 75 kW, através do aumento do diâmetro das tubagens de ligação. Isto demonstra que, através do cuidadoso dimensionamento da instalação e das bombas, consegue-se obter ganhos muito relevantes na redução do consumo de energia. Sempre que necessário, algumas válvulas de borboleta de by-pass, automatizadas, garantem o caudal mínimo das bombas. O sistema transmite todos os sinais de entrada, estados de funcionamento e mensagens de avaria ao sistema de controlo do processo, através de uma interface Profibus DP. As bombas da bacia de entrada são comandadas de modo a que o nível de água de arrefecimento no reservatório nunca desça abaixo de 1,97 metros. Para cumprir este requisito, é necessário que uma das bombas esteja sempre em funcionamento, a caudal mínimo, para permitir o auto-arrefecimento. Sempre que o nível da água ultrapassa o nível superior do reservatório (2 m), a água é encaminhada para a tubagem de descarga para o Reno.
As bombas do reservatório de água de arrefecimento bombeiam a água para os pontos de consumo na fábrica, através de um colector. O comando de circuito fechado está regulado para uma pressão constante de 4.5 bar. Quando é atingido o caudal mínimo da bomba, uma válvula de borboleta abre o by-pass. O ponto de regulação para controlo da temperatura da água de arrefecimento é 21 °C, mas este não tem qualquer ligação ao comando da bomba. A temperatura é controlada através de duas válvulas de mistura (de cunha), com actuadores pneumáticos (Fig. 6).
Fig.6: Válvula de mistura, de cunha, com actuador pneumático
Este tipo de actuadores permitem que as válvulas respondam rapidamente. As suas posições são transmitidas ao PLC através de uma sensor de posição. O caudal de água quente que entra no reservatório de água de arrefecimento, para aumentar a temperatura da água, depende da posição da válvula de cunha.
Quando a temperatura da água de arrefecimento atinge 21 °C, a válvula de cunha fecha-se totalmente e a água transborda para o Reno. Como o fecho da válvula implica uma rápida mudança da temperatura, foi necessário ligar o controlo da válvula ao controlo das bombas da bacia de entrada, para garantir que a temperatura máxima de saída, de 30 ºC, nunca é ultrapassada – nem mesmo por um curto período. Consequentemente, é agora bombeada um pouco mais água fria do rio, através do topo do reservatório, sempre que a válvula de cunha se fecha.
Esta solução consegue lidar com os picos de temperatura à saída e permite que a temperatura da água de arrefecimento se mantenha exactamente nos 21 °C. Quaisquer mudanças bruscas no processo produtivo são sinalizadas ao sistema de controlo das bombas pelo sistema de controlo da fábrica. Isto significa que, se a roda de fundição parar, a posição das válvulas de cunha é gravada. Logo que a produção recomeçar, as válvulas de cunha voltam rapidamente à posição que tinham antes da paragem. Graças ao mecanismo de controlo agora existente, só um aumento da temperatura da água do rio acima de 21 °C fará aumentar a temperatura da água de arrefecimento.
Conclusão
É possível reduzir os custos da electricidade ao mínimo através da instalação de um sistema de controlo da velocidade que actue em função do consumo e de bombas de elevado rendimento, bem como através de um cuidadoso dimensionamento das bombas e da optimização das tubagens e das válvulas. É ainda importante o apoio técnico dos especialistas de bombas na fase de projecto, especialmente em situações complexas, de modo a garantir soluções optimizadas e actuais.