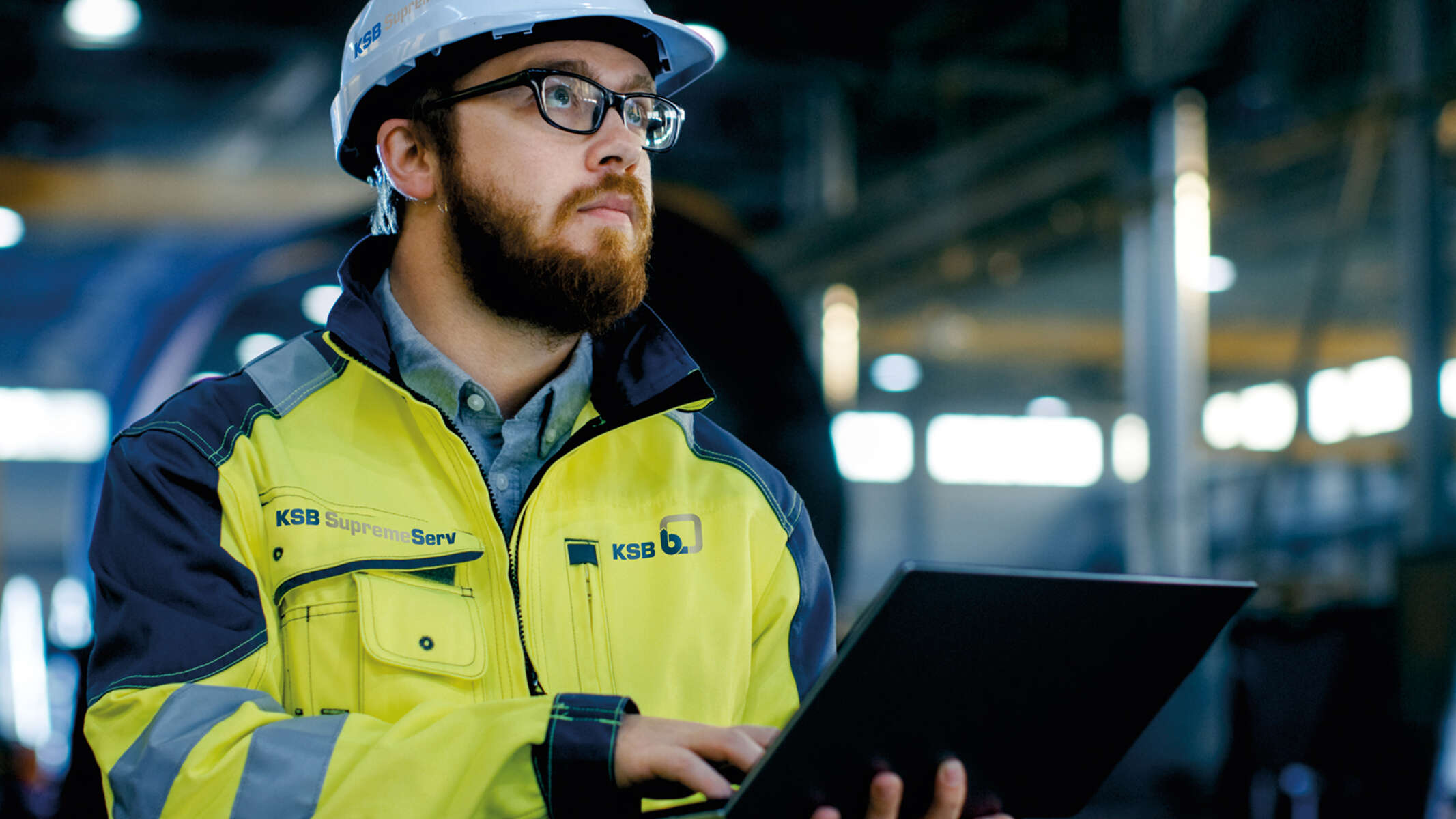
Onderhoud 4.0: hoe digitalisering het onderhoud zal vereenvoudigen.
De vierde industriële revolutie brengt veel nieuwe mogelijkheden met zich mee op het gebied van digitalisering en automatisering, die veel bedrijven al voor zichzelf hebben ontdekt. En daar zijn goede redenen voor.
De vierde industriële revolutie brengt veel nieuwe mogelijkheden met zich mee op het gebied van digitalisering en automatisering, die veel bedrijven al voor zichzelf hebben ontdekt. En daar zijn goede redenen voor.
Waarom onderhoudsbeheer zo belangrijk is
De toenemende kostendruk dwingt veel bedrijven om nieuwe manieren te zoeken om de efficiency te verhogen, maar het potentieel van veel besparings- en rationaliseringsmethodes is grotendeels uitgeput. Steeds meer ondernemingen zien onderhoud daarom als een echte waardeverhogende factor en spreken in dit verband van 'Maintenance 4.0' of 'Onderhoud 4.0'. Het voorkomen van ongeplande productie-uitval, door vroegtijdige detectie van slijtageverschijnselen en defecten biedt immers een enorm besparingspotentieel. Hier biedt Industrie 4.0 tal van mogelijkheden, die het onderhoud van de toekomst radicaal zullen veranderen. In dit artikel leest u meer!
Installaties zijn onderhevig aan voortdurende slijtage – en dat geldt niet alleen voor bewegende delen: ook bij weinig of geen gebruik kan de technische functionaliteit van een installatie aanzienlijk worden beperkt. IJzerhoudende componenten kunnen roesten, kunststof- of rubberafdichtingen kunnen poreus worden en de viscositeit van gebruikte oliën kan afnemen. Een verwaarloosd onderhoudsbeheer kan dus aanzienlijke negatieve gevolgen hebben op het kwaliteitsniveau van de productie en volledige bedrijfsprocessen.
In het ergste geval leidt een onontdekte fout of schade tot uitval van een complete installatie waarbij het volledige productieproces tot stilstand komt. Maar ook de gevolgschade van verwaarloosd onderhoud is niet te onderschatten: zo kan een defect van een enkel onderdeel, bijvoorbeeld door een materiaalfout, later tot ernstige gevolgschade leiden. Onderhoud wordt daarmee voor veel bedrijven een doorslaggevende factor voor succes.
Het belang van onderhoudsbeheer is toegenomen
Onderhoud is de afgelopen jaren steeds belangrijker geworden. Dit komt vooral door de voortdurend toenemende wereldwijde concurrentiedruk. Deze leidt ertoe dat het belang van Overall Equipment Effectiveness (OEE), d.w.z. de effectiviteit van de complete installatie – een kengetal voor de productiviteit van een installatie –, is toegenomen. Een zo hoog mogelijke beschikbaarheid en een efficiënt gebruik van hulpbronnen zijn hier de belangrijkste kerncijfers.
Verbeterde onderhoudsstrategieën hebben vooral tot doel de bedrijfstijden te verlengen, stilstandtijden te verkorten en ongeplande uitval te voorkomen, met andere woorden: de beschikbaarheid van een installatie te maximaliseren.
De technische complexiteit van installaties is de afgelopen decennia aanzienlijk toegenomen, omdat productiesystemen vaak nauw met elkaar verbonden zijn en veilige voorraden vaak worden vermeden. Een storing van een deelproces kan als snel leiden tot het uitvallen van hele procesketens, wat ernstige financiële gevolgen kan hebben. Zo wordt het onderhoud in de toekomst steeds meer afgestemd op de planning van productie en hulpbronnen en is het een doorslaggevende factor voor succes.
Hierbij kan met name het gebruik van digitale oplossingen nuttig zijn: op basis van gegevens over de toestand van een machine kan dreigende schade al van tevoren worden gedetecteerd, zodat vroegtijdig onderhoudswerkzaamheden kunnen worden gestart. Dit biedt de mogelijkheid om zowel de onderhoudskosten te verlagen als de kosten van uitval zoveel mogelijk te voorkomen.
Juist in een wereld van steeds complexere productieprocessen wordt het thema 'Onderhoud 4.0' steeds belangrijker
Onderhoud vroeger en nu
Net zoals de industriële geschiedenis kan worden onderverdeeld in verschillende generaties (Industrie 1.0 tot Industrie 4.0), kan ook het onderhoud in verschillende generaties worden onderverdeeld. In het algemeen wordt een onderscheid gemaakt tussen de verschillende onderhoudsstrategieën:
- Onderhoud 1.0, tot ongeveer 1960: reactief onderhoud, reparatie na uitval van een installatie, ook wel 'Breakdown Maintenance' genoemd.
- Onderhoud 2.0, tot ongeveer 1980: preventief, tijdafhankelijk onderhoud. De focus wordt gericht op beschikbaarheid, levensduur en lagere kosten.
- Onderhoud 3.0, tot ongeveer 2015: toestandsgericht onderhoud door handmatige maatregelen. Naast de aspecten van Onderhoud 2.0 stonden hier andere punten centraal: een constante of betere productkwaliteit, een grotere zekerheid van installaties en omgeving en een hoger rendement.
- Onderhoud 4.0, vanaf ongeveer 2015: toestandsgericht onderhoud door permanente digitale bewaking, Condition Monitoring, etc.
Maintenance 4.0 is tegenwoordig een belangrijk onderdeel binnen de waardeketen van een Smart Factory. Zo dient het onderhoud om de stabiliteit, functionaliteit en integriteit van de zeer complexe 4.0-systemen te waarborgen.Sensoren en cyberfysieke systemen en het IoT (Internet of Things) spelen daarbij een centrale rol.
Slimme sensoren en digitale tweelingen
In het tijdperk van Onderhoud 4.0 zijn machines 'intelligent' geworden: ze laten trends zien en wijzen zelfstandig op mogelijke storingen of uitval van componenten. Dit wordt mogelijk gemaakt door slimme sensortechnieken op afzonderlijke componenten of complete installaties, die continu gegevens (bijv. temperatuur, druk, stromen of trillingen) over de toestand van de machine verzamelen. Met behulp van deze verzamelde gegevens en alle andere bekende objectinformatie kunnen digitale tweelingen (Digital Twins) worden samengesteld: digitale 1:1-afbeeldingen van het reële object. Deze digitale tweelingen maken complexe analyses en simulaties mogelijk en vormen daarmee een basis voor Industrie 4.0.
Deze verzamelde gegevens worden gedocumenteerd als onderdeel van digitale 'feiten over de levenscyclus van installaties'. In dergelijke uitgebreide digitale dossiers worden de gegevens van alle in een installatie ingebouwde componenten opgenomen. Zij zijn met name bedoeld om de levenscyclus van een installatie volledig te documenteren, waarmee zij een schat aan kennis en informatie vormen voor werkzaamheden aan de installatie, besluitvorming over werkzaamheden, het aantonen van handelingen en als basis voor communicatie. Vaak zijn de gegevens echter afkomstig van verschillende fabrikanten – daarom zijn hier universele interfaces nodig om de beschikbare gegevens correct samen te voegen en te kunnen consolideren.
Aan de hand van de door het digitale levenscyclusdossier geleverde gegevens kunnen bijvoorbeeld onderhoudsactiviteiten nauwkeuriger worden gepland en in verschillende delen van de installatie worden geconsolideerd. Het dossier toont niet alleen alle uitgevoerde servicewerkzaamheden, maar ook aanpassingen van een installatie aan, wat met name voor het onderdelenbeheer essentieel is. Ook kunnen digitale bewakingseenheden zo worden ingesteld, dat in gevallen van een afwijking van het normale bedrijf automatisch een push-bericht naar de exploitant wordt verzonden. Dit bericht wordt op zijn beurt in het levenscyclusdossier bewaard en kan op ieder moment worden bewerkt of opgevraagd. Het onderhoudsteam houdt zo op elk moment overzicht op de toestand van de installatie en weet precies of er een storing zal optreden en of onderhoud noodzakelijk is. Met deze informatie is het team in staat om op tijd onderdelen te bestellen en services efficiënt te coördineren. Zo kunnen van tevoren al werkzaamheden worden uitgevoerd, waardoor stilstand van de installatie tot een minimum wordt beperkt.
Er kan dus worden geconcludeerd dat predictief onderhoud in de toekomst steeds relevanter wordt voor een concurrerende productie. Volgens een recent onderzoek* van het World Economic Forum en het consultancybedrijf Accenture zou 12% van de kosten kunnen worden bespaard met geplande reparaties ten opzichte van ongeplande reparaties en bijna 30% op de onderhoudskosten. Bovendien kan het percentage ongeplande stilstand volgens het onderzoek met 70% afnemen. Uit een ander onderzoek*, van Roland Berger, blijkt ook dat met predictief onderhoud nog slechts 15% van de tijd aan onderhoud wordt besteed, waar dit bij 'reactief' onderhoud 40% bedraagt.
Overzicht van de belangrijkste voordelen van Maintenance 4.0:
- Nog beter inzicht in processen door transparantie van de installatie
- Verbetering van het rendement door minder stilstandtijden en voorkomen van ongeplande uitval
- Geconsolideerd en planbaar onderhoud door permanente evaluatie van de verzamelde gegevens (Predictive Maintenance)
- Verbetering van de efficiëntie van machines door aantonen van potentiële verbeteringen.
Met behulp van digitale gegevens houdt het onderhoudsteam voortdurend overzicht op installatie en weet het precies of en wanneer storingen kunnen optreden.
Maintenance 4.0 aan de hand van het voorbeeld 'pompbewaking'
Inmiddels is er een groot aantal slimme producten en services om doelgericht de efficiëntie en de bedrijfszekerheid van een pomp te verhogen. Het principe van het slimme pompaggregaat is eenvoudig: sensoren en regeling worden met de pomp verbonden; de werking van de pomp wordt dan decentraal, automatisch en autonoom aangepast. Een van de meest succesvolle Smart Factory-oplossingen van KSB is KSB Guard, een holistische cloudoplossing voor bewaking op afstand van pomppopulaties en andere roterende machines.
KSB Guard, bestaande uit sensoren en een cloudtoepassing, biedt de mogelijkheid om de statusgegevens een pomp op elk moment te bewaken. De werking van KSB Guard is daarbij even eenvoudig als effectief: een Tech-unit (sensoreenheid) op de pomp bewaakt regelmatig temperatuur- en trillingswaarden en stuurt de geregistreerde gegevens via de zend- en batterij-eenheid naar de gateway, die een verbinding met KSB Cloud tot stand brengt. De meetgegevens en andere informatie over de pomp kunnen vervolgens gemakkelijk en eenvoudig via de KSB Guard-webportal of de KSB Guard-app worden opgevraagd.
Via het webportaal of app heeft de exploitant echter niet alleen voortdurend een overzicht van de belastingstoestand en de trillings- en temperatuurwaarden van zijn pomp: door de mogelijkheid om pompspecifieke grenswaarden voor de meetwaarden in te stellen, geeft KSB Guard vroegtijdig informatie over veranderende installatietoestanden, zowel via e-mail als via een push-bericht. Via de ingebouwde bedrijfsurenteller geeft KSB Guard aan wanneer een lager het einde van zijn levensduur heeft bereikt. Bovendien heeft de exploitant van de installatie via de app of de webportal altijd inzicht in de volledige onderhoudshistorie van de pomp, waarin details omtrent een bepaalde onderhoudsmaatregel kunnen worden vastgelegd. Door herkenning van trends, is het daarbij mogelijk om het onderhoud van het aggregaat vroegtijdig in gang te zetten, waardoor onderhoudswerkzaamheden beter gepland en ongeplande onderhoudswerkzaamheden voorkomen kunnen worden en de beschikbaarheid van de pompen in het algemeen aanzienlijk kan worden verhoogd. Handig: KSB biedt zijn klanten hierbij ondersteuning met uitgebreide servicediensten – bijvoorbeeld onderdelenservice of Reverse Engineering.
Succesvoorbeeld InfraServ Wiesbaden (ISW)
ISW is al sinds 1997 exploitant van het 96 hectare grote industriepark Kalle-Albert. Het door ISW gegarandeerde persluchtvoorziening in het industriepark levert 24 uur per dag ongeveer 22 duizend kubieke meter perslucht per uur met 5 bar overdruk. Om de koelwaterpompen van het persluchtsysteem daarbij betrouwbaar en continu te bewaken, vertrouwt ISW op de bewakingsunit KSB Guard. Dankzij KSB Guard hebben zowel de productieleiding van ISW als de KSB-technici via de webportal alle statusgegevens van de pompen 24 uur per dag in beeld.
Gelukkig: in oktober 2019 werd namelijk al een afwijking van de normale werking van een van de pompen gemeld. Nadat KSB Guard een waarschuwing wegens te hoge trillingen had gedetecteerd, werd InfraServ Wiesbaden onmiddellijk automatisch geïnformeerd. Daardoor kon ISW vroegtijdig een beginnende lagerschade opsporen en op een nog niet kritiek moment aan de reparatie van de pomp in de eigen werkplaats beginnen. Hoewel bij uitval een tweede pomp zou zijn gestart om de persluchtvoorziening storingsvrij te handhaven, kon een spontane uitval van de installatie met ongeplande stilstandtijden en zeer hoge reparatiekosten dankzij KSB Guard op tijd worden voorkomen.
In het industriepark Kalle Albert in Wiesbaden heeft KSB Guard hoge trillingen gedetecteerd op een van de pompen. De technici hebben op niet-kritieke tijden het onderhoud in gang gezet, waardoor een spontane uitval van de installatie en daarmee gepaard gaande ongeplande stilstandtijden en verstrekkende bedrijfsschade werd voorkomen.
Conclusie
Hoe het onderhoud dankzij Maintenance 4.0 radicaal kan worden vereenvoudigd
Het gebruik van slimme sensoren en IoT-technologieën biedt geheel nieuwe mogelijkheden voor verhoging van de OEE – dankzij Onderhoud 4.0. Want intelligente machines melden als het ware uit zichzelf dat ze afwijkingen van het normale bedrijf vaststellen. Het gebruik van de nieuwe technologieën is vooral aan te bevelen wanneer grote en dure machines 24 uur per dag draaien en wanneer onvoorziene uitval ernstige gevolgen heeft. Door de geringe investeringskosten is echter ook de digitalisering van minder complexe installaties het overwegen waard.
Heeft u nog vragen? Neem gerust contact met ons op: KSB heeft een uitgebreide expertise op het gebied van digitalisering van installatiecomponenten en kan ook uw bedrijf toerusten voor Onderhoud 4.0!
*https://digital.oup-fluidtechnik.de/o-p-fluidtechnik-4-2016/56531515/18
https://www.industry-of-things.de/amp/wartung-40-senkt-kosten-a-541428/
https://www.yumpu.com/de/document/read/62212195/industrieanzeiger-1118 (Seite 46/47)
Gebruikte producten
KSB Guard
Slimme en uitgebreide bewakingsservice voor pompen en andere roterende machines – 24/7 beschikbaar en fabrikantonafhankelijk. Samen met KSB om voorspellend onderhoud te voorspellen en te profiteren van uitgebreide transparantie, verhoogde beschikbaarheid, meer bedrijfszekerheid en efficiënte werking (van ongeregelde pompen). Belangrijke bedrijfsgegevens zoals trillingen, temperatuur, bedrijfsuren en belastingsstatus (van ongeregelde pompen) kunnen altijd en overal worden opgeroepen met KSB Guard. Indien er ook een afwijking van de normale werking optreedt, wordt er direct een melding verzonden via het KSB Guard webportaal/de app. Daarnaast bieden de experts van het KSB Monitoring Center ondersteuning bij de oorzaakanalyse.