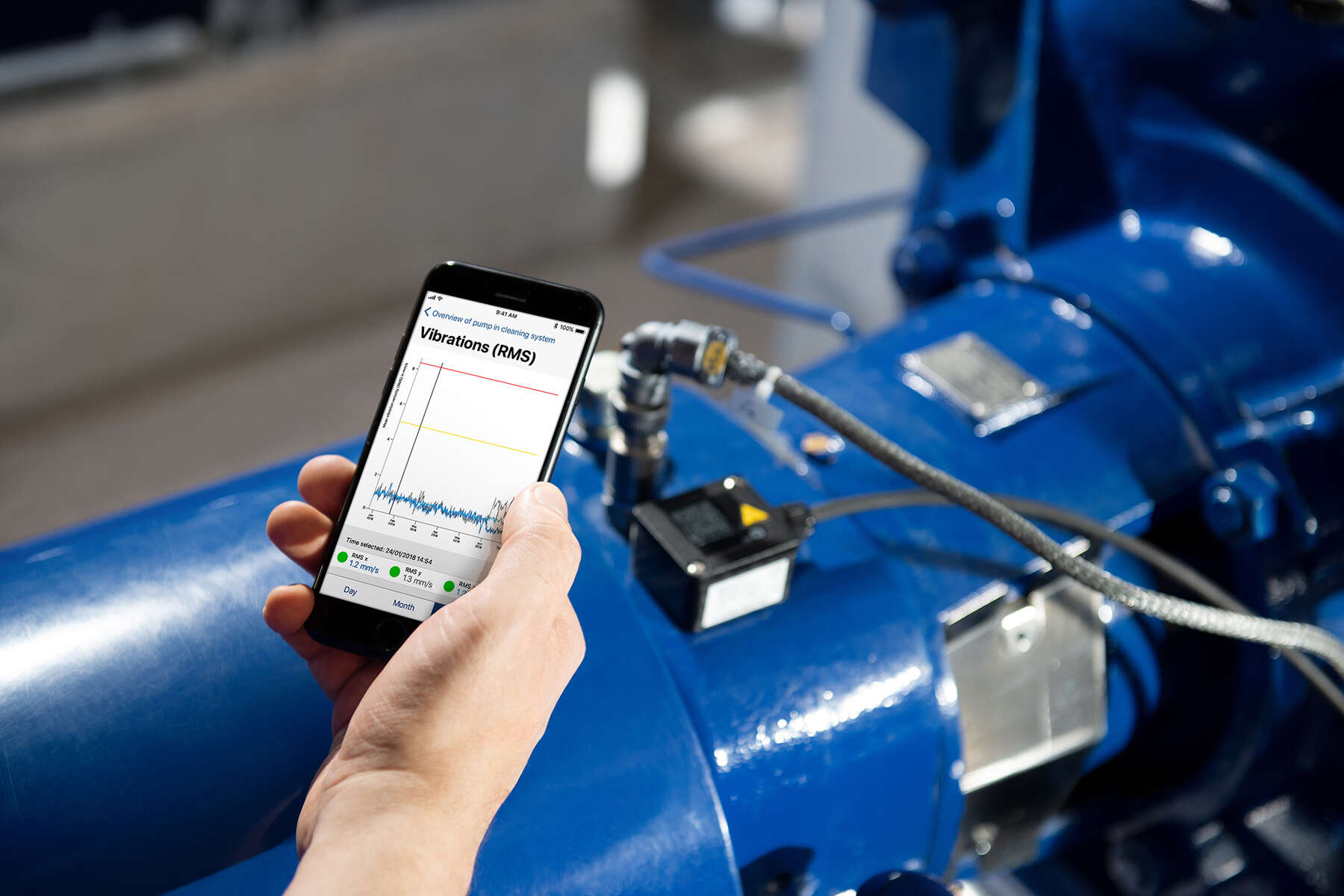
Digital monitoring tool KSB Guard continuously monitors pumps
Thanks to KSB Guard, it is now possible to avoid malfunctions and efficiently plan maintenance. The tool is in operation at the ROLF SANDVOSS INNOVATION CENTER of SAMSON AG.
The project: KSB equips unique development and test centre with monitoring tool and pumps
As well as being the world’s largest development and test centre for valve technology, it is also unique with regard to its form: the ROLF SANDVOSS INNOVATION CENTER (RSIC) operated by SAMSON. After two years of construction work, the RSIC in Frankfurt was officially inaugurated in 2017.
Since then, the 7,000 square metre facility has been used for research, development and testing. The goal of SAMSON’s innovation centre is to develop reliable and innovative products of excellent quality for a wide range of applications – and to do this as quickly as possible.
A high degree of reliability and quality can only be guaranteed when products are tested in advance under the most extreme conditions, which is exactly what SAMSON does at the innovation centre. The basis for this is a state-of-the-art testing system – the centrepiece of the facility. It enables tests to be performed in a wide variety of test scenarios with regard to the fluids used, process conditions and industrial application fields.
An important part of the system is the KSB Guard digital monitoring tool. It continuously monitors the pumps, which were also supplied by KSB. Continuous monitoring enables SAMSON to avoid unscheduled downtimes and efficiently plan pump maintenance, ensuring that the system is operated economically and smoothly.
In addition to striving for excellent quality products, SAMSON and KSB are also united by their successful collaboration on previous projects which fostered a spirit of mutual trust. In addition to opting for KSB products, SAMSON furthermore asked KSB to act as its full-service partner for this unique project.
The KSB pumps located in the cellar need to start smoothly at all times, even under the most extreme loads and with irregular operating times.
The customer: SAMSON AG is a manufacturer of control valve technology
Headquartered in Frankfurt am Main, SAMSON AG offers system and product solutions for controlling all types of fluids. The company produces valves, self-operated regulators, actuators, valve accessories, signal converters, automation systems, sensors, thermostats and digital solutions. Fields of application include chemical facilities, power stations, the distribution of district heating, food production and building automation. SAMSON was founded by Hermann Sandvoss in 1907 and today employs around 4,400 staff worldwide.
The challenge: Extreme conditions for the pumps to handle while simultaneously ensuring minimal monitoring and maintenance
The project entailed a whole series of challenges.
- SAMSON required a large number of different pumps which had to be able to withstand sometimes extreme conditions. As SAMSON measures Kvs values and tests pressure losses on its valves, the pumps had to be able to handle pressures of up to 120 bar and flow rates of up to 10,000 cubic metres per hour.
- Pump operation: the pumps are operated irregularly and with long downtimes. Nevertheless, the pumps must be able to be started up quickly and smoothly at all times.
- The pumps need to operate reliably and be easy to maintain. Removing the pumps and then reinstalling them again not only disrupts operations, it also costs time and money.
- The system is located in the cellar. However, a stable connection must be established between KSB Guard and the mobile phone network to ensure the exchange of data.
KSB Guard and KSB pumps only account for one part of the system. To successfully complete the project, effective collaboration with other companies involved was also required
The solution: KSB Guard identifies failure risks at an early stage, enabling maintenance to be precisely planned
The pumps need to operate smoothly despite extreme loads and irregular operating hours. At the same time, monitoring and maintenance needed to be reduced to a minimum. Thanks to the digital monitoring tool KSB Guard, both are possible. Vibration and temperature sensors installed on the pumps continuously monitor the pumps.
KSB Guard then sends the recorded data to the computer or app via the gateway. As the gateway can be positioned flexibly, this enables a stable connection to the mobile phone network to be established – even if KSB Guard is located in the cellar, as was the case with SAMSON.
This provides SAMSON with an overview of all information at all times. Failure risks can be identified at an early stage and maintenance can be precisely planned in advance. Not only does this reduce unscheduled downtimes and disruptions to operations, it also saves on costs.
A total of seven different KSB pumps are installed in the system with various different performance profiles. The individual pump models are Multitec, HPKL, MegaCPK, Etabloc, RDLO, HGM and Movitec.
The smaller pumps feature the PumpDrive variable speed system, which is especially recommended for use in systems with fluctuating demand – as is the case with the innovation centre. The flexible speed control system enables demand-driven operation. This saves energy and increases the efficiency and availability of the pump.
Detailed planning and structured organisation between SAMSON and KSB were crucial to the success of the project. Further success factors in the course of the project were a partnership-based approach to cooperation with all of the companies involved and the reliable supply and delivery of the products and services by KSB.
“Due to previous projects we were already very familiar with KSB’s products and were therefore confident that we had chosen the right partner to support us with such a complex project. KSB is also a pioneer in Industry 4.0 and digitalisation, as demonstrated for example by KSB Guard.”
Domagoj Vnucec, Head of ROLF SANDVOSS INNOVATION CENTER, SAMSON AG
Products used
Etabloc
Single-stage close-coupled volute casing pump, with ratings to EN 733, with replaceable shaft sleeve and casing wear rings, with motor-mounted variable speed system. With KSB SuPremE, a magnetless synchronous reluctance motor (exception: motor sizes 0.55 kW / 0.75 kW with 1500 rpm are designed with permanent magnets) of efficiency class IE4/IE5 to IEC TS 60034-30-2:2016, for operation on a KSB PumpDrive 2 or KSB PumpDrive 2 Eco variable speed system without rotor position sensors. Motor mounting points in accordance with EN 50347, envelope dimensions in accordance with DIN V 42673 (07-2011). ATEX-compliant version available.
HGM/HGM-S
Horizontal radially split product-lubricated multistage ring-section pump with radial impellers, axial and radial single-entry inlet.
MegaCPK
Horizontal radially split volute casing pump in back pull-out design, with radial impeller, single-entry, single-stage, to DIN EN ISO 5199, dimensions to DIN EN ISO 2858, complemented by nominal diameters DN25 and ≥DN200, in large range of material and seal variants; also available as a variant with "wet" shaft and conical seal chamber. ATEX-compliant version available.
Movitec
Multistage vertical high-pressure centrifugal pump in ring-section design with suction and discharge nozzles of identical nominal diameters arranged opposite to each other (in-line design), close-coupled. With KSB SuPremE, a magnetless synchronous reluctance motor (exception: motor sizes 0.55 kW / 0.75 kW with 1500 rpm are designed with permanent magnets) of efficiency class IE4/IE5 to IEC TS 60034-30-2:2016, for operation on a KSB PumpDrive 2 or KSB PumpDrive 2 Eco variable speed system without rotor position sensors. Motor mounting points in accordance with EN 50347, envelope dimensions in accordance with DIN V 42673 (07-2011). ATEX-compliant version available.
Multitec
Multistage horizontal or vertical centrifugal pump in ring-section design, long-coupled or close-coupled, with axial or radial suction nozzle, cast radial impellers and motor-mounted variable speed system. ATEX-compliant version available.
RDLO
Single-stage axially split volute casing pump for horizontal or vertical installation, with double-entry radial impeller, mating flanges to DIN, EN or ASME.
PumpDrive 2/PumpDrive 2 Eco
Modular self-cooling frequency inverter that enables continuously variable speed control of asynchronous and synchronous reluctance motors by means of analog standard signals, a field bus or the control panel. As PumpDrive is self-cooling, it can be mounted on a motor, on the wall or in a control cabinet. Up to six pumps can be controlled without needing an additional controller.