
KSB model testing: Gas pockets – and what can be done about them.
Undissolved gases trapped in high points of pipes can significantly increase flow resistance. Consequences include energy loss and reduced flow rates. But there are ways to avoid or eliminate gas pockets. KSB has investigated how this can be achieved at different flow rates in a comprehensive model test. Find out more.
Undissolved gases trapped in high points of pipes can significantly increase flow resistance. Consequences include energy loss and reduced flow rates. But there are ways to avoid or eliminate gas pockets. KSB has investigated how this can be achieved at different flow rates in a comprehensive model test. Find out more.
KSB gets to the bottom of gas pockets in piping as part of a model test
KSB regularly carries out model tests to simulate a wide variety of processes in pump systems and to obtain new findings for optimisation and improving efficiency. KSB experts have now developed a new functional model for a topic that concerns many plant operators: Gas pockets in pipes. Gas pockets are a troublesome issue for many plant operators because undissolved gases in pipes with pronounced high points can increase flow resistance, which can lead to costly energy losses and reduced delivery quantities.
KSB's functional model makes it possible to demonstrate various options for expelling air from pipes at different flow velocities. To make this simulation possible, KSB's functional model comprises piping with distinct high and low points. It is supplied with water from a pump installed in a water tank. At the end of the pipe, the water is returned back into the tank. The flow rate and, with that, the flow velocity can be controlled by means of gate valves on the inlet and the discharge sides. The required head is illustrated by the water column in the riser pipe. A display shows the flow rate.
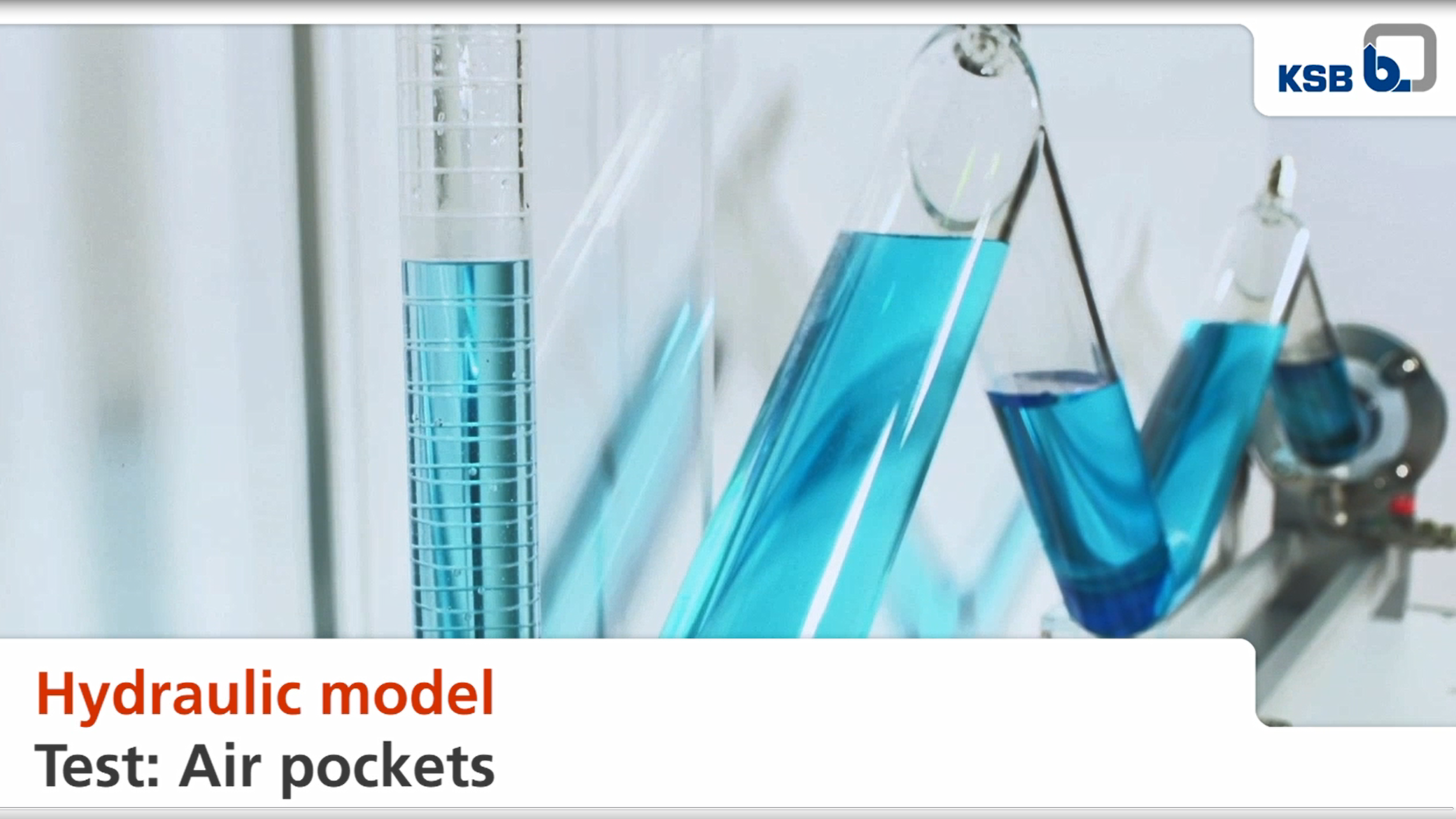
What you should know about gas pockets:
The movement of water can be greatly affected by air pockets in pipes with pronounced high points because they increase flow resistance. The term "air pocket" is, strictly speaking, misleading. The term "gas pocket" is more accurate since air is a mixture of certain gases in the appropriate ratio. This also covers the topic of waste water with gas emissions, methane gas development or the formation of gas of a chemical cause. Gas pockets can occur if the fluid handled tends to form gas or is already gas-laden.
Gas pockets can result in the projected flow rate of the designed pump not being reached – due to energy losses. KSB's model test has shown that, depending on their characteristics, pumps can enter transient operating conditions because the water column in the piping system is fluctuating. The additional pressure losses due to the gas pockets at the high points of the pipe increase the risk of part load operation of the centrifugal pump. The model test also showed that the head curve drops with increasing volumetric gas content.
How to prevent gas pockets
The KSB experts recommend:
- Evaluating the fluid to be handled with regard to its gas content or its potential for gas formation
- Paying attention to the design of the pump sump. A pump sump should be designed to prevent fluid from hitting the surface of the fill level and, with that, any gas from entering the fluid. If this cannot be avoided, the distance between the pump and this level should to be increased so that gas bubbles can rise and leave the fluid.
- Venting of the affected high points of the piping
- Calculation of the capacity for self-venting. In most cases, however, this is not feasible due to the restricted pump design: The prerequisite for this is a sufficiently large effective volume of the pump sump.
What pipes do gas pockets actually occur in?
Gas pockets can occur if the fluid handled tends to form gas or is already gas-laden. As the amount of gas per volume of pumped fluid increases, the pump performance is increasingly affected.
The more pronounced the geodetic high points in the piping layout, the greater the tendency for severe problems to occur during the pumping process.
Conclusion of the Gas pockets model test
All tests have shown: As the gas content per volume of pumped fluid increases, the pump performance is increasingly affected. As gas mixture is lighter than the fluid handled and the gas is separated by the rotation of the impeller when the fluid passes through the pump. Depending on the type of impeller, strong vibrations may occur at the pump. The transient behaviour of the entire system (pump - piping - fluid) changes. Accurate calculations (e.g. transient flow analysis) are thus made more difficult and they harbour a corresponding potential danger. In waste water pump stations the emission of gas can also lead to the formation of floating sludge on the water surface. Gas pockets can even occur when the piping is first primed.
Model testing by KSB: Thinking small, building big
In general, KSB conducts model tests for an object or procedure whenever the measurement of original conditions is not technically or economically feasible. Experimental investigations enable KSB to uncover new potential for increasing efficiency in pump systems.
The gas pocket hydraulic model test is just one of the many model tests with which KSB has gained valuable knowledge that we are happy to pass on to our customers. Expand your specialist knowledge also with the results of our other hydraulic model tests on topics such as benching, solids transport or gas pockets.
Good to know: When planning, performing and evaluating all model tests and transferring the results to the original-size machine and/or the original operating conditions, the affinity laws are observed and applied. Apart from maintaining geometric similarity, this involves considering changes in length due to elastic and thermal deformations, converting test results on the basis of affinity laws, observing fluid properties, and much more.
In other words, everything that allows a model test to optimise the daily operation of a pumping system in real life.
Do you have any questions? Please contact us. We look forward to hearing from you.
Suitable products
Amarex KRT
Horizontal or vertical single-stage submersible motor pump in close-coupled design, with various next-generation impeller types, for wet or dry installation, stationary or transportable version, with energy-saving motor and models for use in potentially explosive atmospheres.
Multitec
Multistage horizontal or vertical centrifugal pump in ring-section design, long-coupled or close-coupled, with axial or radial suction nozzle, cast radial impellers and motor-mounted variable speed system. ATEX-compliant version available.